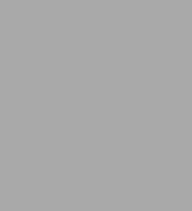
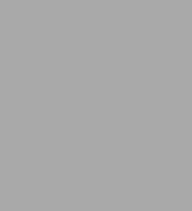
Paperback(Revised and Expanded)
-
PICK UP IN STORECheck Availability at Nearby Stores
Available within 2 business hours
Related collections and offers
Overview
Developing a compromise method of stone construction that is both simpler and truer to the stonemason's art than the popular slipform method, the Longs built an aesthetically satisfying home of stone on a limited budget and no previous construction experience. In this classic how-to book, the author describes the complete building process in clear, easy-to-follow steps and, in so doing, dispels the myth of difficulty that surrounds stone construction.
Product Details
ISBN-13: | 9781552092989 |
---|---|
Publisher: | Firefly Books, Limited |
Publication date: | 10/01/1998 |
Edition description: | Revised and Expanded |
Pages: | 128 |
Sales rank: | 803,962 |
Product dimensions: | 9.00(w) x 11.00(h) x (d) |
About the Author
Read an Excerpt
Architecture is inhabited sculpture Constantin Brancusi
Fieldstone is an ideal medium for amateur builders. The massive strength in solid walls of stone comes more from the material than from skill. And if the lines are not exactly straight, no critic's eye can tell which wiggles are the builder's and which of them came with the stone. Little mistakes can disappear in the rough-hewn texture of the rock.
Despite the forgiving nature of the material and its undeniable beauty, surprisingly few amateur builders are willing to tackle a homemade house of stone. Such reluctance is unfortunate because it is too often based on unfounded fears. As our own stone walls began to grow visible from the road, we attracted a steady stream of passing admirers and critics. The first was a real estate agent, teethed-no doubt-on stockbroker Tudor and relocatable anything. He watched for a while, then shook his head and muttered, "Gonna make a hell of a noise when it comes down."
Others have been more polite but no more confident in the capacity of two green exurbanites to raise a stone house from scratch. The doubts are usually voiced in one of three ways:
"What if it falls?"
"It must be more complicated than that!"
"That stuff must weigh a ton!"
Only the last of those doubts has any basis in reality. A house-worth of stone weighs more than a ton it can weigh hundreds of tons. Taken one stone at a time, though, it is no more than any other middle-aged, out-of-shape weekend putterer could handle or, indeed, could benefit from.
"What if it falls?" is a fear that makes much less sense. Gravity ensures that every stone presses directly down on the ones beneath. Of course it wants to fall, but it wants to fall straight down through the other stones. It can't go anywhere unless some force pushes it sideways out of the wall, and such a force would have to be extremely potent to push out a stone that is held in place by tons of rock above. In reality, there might be a danger that a whole wall section would begin to tip in unison. Good foundations and a few simple design rules make such a catastrophe very unlikely.
"It must be more complicated than that!" is the usual comment of those who watch us work for a while or even try a hand themselves. The answer is, "It doesn't have to be." With the greatest respect for the professional masons and engineers who design and build the truly complex jobs, I must distinguish such work from the very plain and simple skills that suffice to build an ordinary wall in an ordinary house. Real stonemasons are a rare and talented breed. Their skills take years to learn and develop. They have the ability to build airy spires, flying buttresses and fanciful designs that reach the limits of the material. A simple wall in a simple house, however, is the sort of thing that untrained yeomen and illiterate peasants have built for themselves for millennia past. It is only in this recent era of the specialist that we have begun to doubt our ability to do such simple things for ourselves.
Weekend builders don't hesitate to go after wood with hammer and saw, though few are master carpenters. Amateur painters abound, though professionals could do better. Why, then, should building with stone be any different? There is a myth about stone that makes newcomers disbelieve the ease with which they can create beauty and strength. "It must be more complicated than that." Of course it is, but even the most amateurish efforts are still capable of producing a house that will outlast anything made of wood.
A few years ago, we found ourselves living in a too-small house surrounded by fencerows and and fields full of stone. Heartbreak and frustration for farmers but a bonanza for the builder. With the basic material so freely at hand, building in stone was an easy choice. The hard part was in deciding how. Full of all the doubts that our roadside critics later voiced, we set about looking for an easy way.
Blessed with an abundance of old stone buildings in the area, we found no shortage of examples of different styles from which to choose. Sandstone, limestone and granite abound. Fine houses and official buildings, the heritage of craftsmen who emigrated from Scotland 150 years ago, set a benchmark for skill and polish that we knew was beyond us. Cruder buildings, barns and cellars, obviously built by the settlers themselves, were clearly within the limited range of amateur talents we could muster but didn't seem up to the building code or up to our expectations of what a house should be.
Building with forms, the method first described by Edward Flagg, expanded by Helen and Scott Nearing and adopted by Karl and Sue Schwenke (Build Your Own Stone House Using the Easy Slipform Method) seemed, at first, to meet our needs. In the end it proved to be more complex and expensive than were simpler, more basic techniques.
To the casual observer, a wall of traditional stone construction may appear more neat and orderly than it really is. The closely fitted stones in the visible face are just that a façade. Chances are, only a few of them extend through the full thickness of the wall. If you could walk inside and look at the back of the wall, you would not see the expected mirror image of the front but a whole different face. The two faces are tied together with a few large stones that reach from one side to the other, and the rest of the core is of rougher construction, rubble or even air space.
The two-faced approach is one of the reasons that older stone buildings have such massively thick walls. Accommodating the rough back sides of two faces meant that a wall could rarely be less than 2 feet thick. Some masons deliberately left air spaces in the core as the only concession to insulation. It worked to a degree-but required an even thicker wall.
Even with air spaces in the core, lath and plaster, paneling, paper or anything else the shivering inhabitants were wont to add, early stone houses were cold and often damp as well. Modern renovators add new stud walls on the inside with a full thickness of insulation or resign themselves to leaving an oil truck backed up to the furnace all winter. With an inner lining of fiberglass and studs, the walls get thicker. And the inevitable result of thicker walls is smaller rooms or having to start with a bigger house.
The bigger-house alternative brings us to the other disadvantage of the traditional technique: its extravagant use of material. The massive walls require more stone, and building two faces requires more of the better stones, the flat-sided ones or the carefully cut ones. When masons worked with teams of horses and underpaid apprentices to haul and cut the stone, such extravagance might have been warranted.
We, however, were set on going it alone. The two of us together weighed only 250 pounds, and we hardly had a callus between us. An 18-inch wall would weigh 80,000 pounds less than a 24-inch wall. A mere 6 inches would save us 40 tons of digging, hauling, dragging and lifting. And then, to keep us warm, the extra inside face would have to be covered anyway. It was hardly worth the effort.
Slipform building is virtually a poured concrete wall with stones set in the outer face. The builder begins with a large number of portable wooden forms that are bolted and wired together to contain the pour. After the forms are aligned and braced, stone is set in the front and concrete is worked between and behind them. When a section has set, the lower forms are unbolted, removed and replaced on top of the higher forms, leapfrogging up the wall.
This was at first appealing because it required only a single face of decent stones, backed with concrete and rubble. Ergo: thinner walls and 40 tons less we
Table of Contents
The Myth of Stone
Plans
Footings and Foundations
Framing
Tools and Supplies
Stone
Laying Stone
Arches
Special Touches
Fireplaces and Chimneys
Variations
Epilogue