Automated Continuous Process Control / Edition 1 available in Hardcover
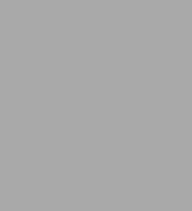
Automated Continuous Process Control / Edition 1
- ISBN-10:
- 0471215783
- ISBN-13:
- 9780471215783
- Pub. Date:
- 03/05/2002
- Publisher:
- Wiley
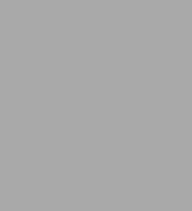
Automated Continuous Process Control / Edition 1
Hardcover
Buy New
$179.95Buy Used
$139.96-
-
SHIP THIS ITEM
Temporarily Out of Stock Online
Please check back later for updated availability.
-
Overview
Beginning with the very basics of process control, Automated Continuous Process Control builds upon each chapter to help the reader understand and efficiently practice industrial process control. This complete presentation includes:
- A discussion of processes from a physical point of view
- Feedback controllers and the workhorse in the industry–the PID controller
- The concept and implementation of cascade control
- Ratio, override (or constraint), and selective control
- Block diagrams and stability
- Feedforward control
- Techniques to control processes with long dead times
- Multivariable process control
Applicable for electrical, industrial, chemical, or mechanical engineers, Automated Continuous Process Control offers proven process control guidance that can actually be used in day-to-day operations. The reader will also benefit from the companion CD-ROM, which contains processes that have been successfully used for many years to practice tuning feedback and cascade controllers, as well as designing feedforward controllers.
Product Details
ISBN-13: | 9780471215783 |
---|---|
Publisher: | Wiley |
Publication date: | 03/05/2002 |
Edition description: | BK&CD-ROM |
Pages: | 240 |
Product dimensions: | 7.30(w) x 10.40(h) x 0.75(d) |
About the Author
Read an Excerpt
AUTOMATED CONTINUOUS PROCESS CONTROL
PREFACE
This book was written over a number of years while teaching short courses to industry. Most of the participants were graduate engineers, and a few were instrument technicians. For the engineers, the challenge was to show them that the control theory most of them heard in college is indeed the basis for the practice of process control. For the technicians, the challenge was to teach them the practice of process control with minimum mathematics. The book does not emphasize mathematics, and a serious effort has been made to explain, using readable language, the meaning and significance of every term used< that is, what the term is telling us about the process, about the controller, about the control performance, and so on.
The book assumes that the reader does not know much about process control. Accordingly, Chapter 1 presents the very basics of process control. While several things are presented in Chapter 1, the main goals of the chapter are (1) to present why process control is needed, (2) to present the basic components of a control system, (3) to define some terms, and (4) to present the concept of feedback control with its advantages, disadvantages, and limitations.
To do good process control there are at least three things the practitioner should know and fully understand< (1) the process, (2) the process, and (3) the process! Chapter 2 presents a discussion of processes from a very physical point of view. Everything presented in this chapter is used extensively in all remaining chapters.
Chapter 3 presents a discussionof feedback controllers, and specifically, the workhorse in the process industry< the PID controller. A significant effort is made to explain each tuning parameter in detail as well as the different types of controllers, with their advantages and disadvantages. In the chapter we describe how to tune, adjust, or adapt the controller to the process. Finally, we discuss the important topics of reset windup, tracking, and tuning flow and level loops. Throughout the presentation, the use of distributed control systems (DCSs) is stressed. Problems are presented at the end of Chapters 2 and 3 to practice what was presented.
As discussed in Chapter 1, feedback control has the limitation that in some cases it does not provide enough control performance. In these cases some other control strategy is needed to obtain the control performance required. What is usually done is to provide assistance to feedback control; feedback control is never removed. Cascade control is a common strategy to improve simple feedback control. In Chapter 4 we present the concept and implementation of cascade control.
In Chapter 5 we describe ratio, override (or constraint), and selective control. To implement these strategies, some computing power is needed. The chapter starts with a presentation of how DCSs handle signals as they enter the system and a description of different programming techniques and computing power. Ratio, override, and selective control are presented using examples. The chapter ends with some hints on how to go about designing these strategies. Many problems are given at the end of the chapter.
Once feedback and cascade control have been presented, it is worthwhile to discuss the important subject of control system stability. Chapter 6 starts with the subject of block diagram and continues with the subject of stability. Block diagrams are used in subsequent chapters to explain the implementation of other control strategies. Stability is presented from a very practical point of view without dealing much with mathematics. It is important for the practitioner to understand how each term in the control system affects the stability of the system.
The detrimental effect of dead time on the stability of a control system is presented in Chapter 6. Chapter 7 is devoted exclusively to feedforward control. Various ways to design and implement this important compensation strategy and several examples are presented. Several techniques to control processes with long dead times are described in Chapter 8, and multivariable process control in Chapter 9. Appendix A provides some process examples to design the control strategies for an entire process. Finally, Appendix B describes the processes presented in the compact disk (CD). These processes have been used for many years to practice tuning feedback and cascade controllers as well as designing feedforward controllers.
The author believes that to practice industrial process control (as opposed to "academic" process control), there is generally no need for advanced mathematics. The author is also aware that the reader is interested in learning "just enough theory" to practice process control. The main concern during the writing of this manuscript has been to present the reader with the benefits obtained with good control, and in doing so, to motivate him or her to learn more about the subject. We hope you do so, and now wish you good controlling!
It is impossible to write a book like this one without receiving help and encouragement from other people. The author would first like to acknowledge the encouragement received from the hundreds of engineers and technicians who have attended the short courses and offered suggestions and examples. The author would also like to sincerely thank his friends, colleagues, and most outstanding chemical engineers, J. Carlos Busot and Armando B. Corripio (coauthor of Principles and Practice of Automatic Process Control). Their friendship, human quality, professional quality, and ability to frustrate the author have had a great positive impact in my life. Thanks to both of you! ABC also provided the material presented in Section 8-2. The author also remembers very dearly his former student, the late Dr. Daniel Palomares, for his contributions to the simulations presented in the CD. accompanying this book. Finally, the author would like to thank his graduate student and friend, Dr. Marco Sanjuan. Marco's friendship, support, and continuous encouragement have made these past years a tremendous pleasure. Marco also put the final touches to the CD.
Carlos A. Smith, Ph.D., P.E.Tampa, FL
2001
Table of Contents
Preface xi1 Introduction 1
1-1 Process Control System 1
1-2 Important Terms and Objective of Automatic Process Control 3
1-3 Regulatory and Servo Control 4
1-4 Transmission Signals, Control Systems, and Other Terms 5
1-5 Control Strategies 6
1-5.1 Feedback Control 6
1-5.2 Feedforward Control 8
1-6 Summary 9
2 Process Characteristics 11
2-1 Process and Importance of Process Characteristics 11
2-2 Types of Processes 13
2-3 Self-Regulating Processes 14
2-3.1 Single-Capacitance Processes 14
2-3.2 Multicapacitance Processes 24
2-4 Transmitters and Other Accessories 28
2-5 Obtaining Process Characteristics from Process Data 29
2-6 Questions When Performing Process Testing 32
2-7 Summary 33
Reference 33
Problems 34
3 Feedback Controllers 38
3-1 Action of Controllers 38
3-2 Types of Feedback Controllers 40
3-2.1 Proportional Controller 40
3-2.2 Proportional–Integral Controller 44
3-2.3 Proportional–Integral–Derivative Controller 48
3-2.4 Proportional–Derivative Controller 50
3-3 Reset Windup 50
3-4 Tuning Feedback Controllers 53
3-4.1 Online Tuning: Ziegler–Nichols Technique 53
3-4.2 Offline Tuning 54
3-5 Summary 60
References 60
Problems 60
4 Cascade Control 61
4-1 Process Example 61
4-2 Implementation and Tuning of Controllers 65
4-2.1 Two-Level Cascade Systems 65
4-2.2 Three-Level Cascade Systems 68
4-3 Other Process Examples 69
4-4 Closing Comments 72
4-5 Summary 73
References 73
5 Ratio, Override, and Selective Control 74
5-1 Signals and Computing Algorithms 74
5-1.1 Signals 74
5-1.2 Programming 75
5-1.3 Scaling Computing Algorithms 76
5-1.4 Significance of Signals 79
5-2 Ratio Control 80
5-3 Override, or Constraint, Control 88
5-4 Selective Control 92
5-5 Designing Control Systems 95
5-6 Summary 110
References 111
Problems 112
6 Block Diagrams and Stability 127
6-1 Block Diagrams 127
6-2 Control Loop Stability 132
6-2.1 Effect of Gains 137
6-2.2 Effect of Time Constants 138
6-2.3 Effect of Dead Time 138
6-2.4 Effect of Integral Action in the Controller 139
6-2.5 Effect of Derivative Action in the Controller 140
6-3 Summary 141
Reference 141
7 Feedforward Control 142
7-1 Feedforward Concept 142
7-2 Block Diagram Design of Linear Feedforward Controllers 145
7-3 Lead/Lag Term 155
7-4 Extension of Linear Feedforward Controller Design 156
7-5 Design of Nonlinear Feedforward Controllers from Basic Process Principles 161
7-6 Closing Comments on Feedforward Controller Design 165
7-7 Additional Design Examples 167
7-8 Summary 172
References 173
Problem 173
8 Dead-time Compensation 174
8-1 Smith Predictor Dead-Time Compensation Technique 174
8-2 Dahlin Controller 176
8-3 Summary 179
References 179
9 Multivariable Process Control 180
9-1 Pairing Controlled and Manipulated Variables 181
9-1.1 Obtaining Process Gains and Relative Gains 186
9-1.2 Positive and Negative Interactions 189
9-2 Interaction and Stability 191
9-3 Tuning Feedback Controllers for Interacting Systems 192
9-4 Decoupling 194
9-4.1 Decoupler Design from Block Diagrams 194
9-4.2 Decoupler Design from Basic Principles 196
9-5 Summary 197
References 197
Problem 198
Appendix A Case Studies 199
Case 1: Ammonium Nitrate Prilling Plant Control System 199
Case 2: Natural Gas Dehydration Control System 200
Case 3: Sodium Hypochlorite Bleach Preparation Control System 201
Case 4: Control System in the Sugar Refining Process 202
Case 5: Sulfuric Acid Process 204
Case 6: Fatty Acid Process 205
Reference 207
Appendix B Processes For Design Practice 208
Installing the Programs 208
Process 1: NH 3 Scrubber 208
Process 2: Catalyst Regenerator 211
Process 3: Mixing Process 213
Index 215