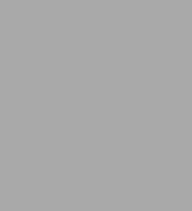
Bemrose on Traditional Woodworking: Carving, Fretwork, Buhl Work and Marquetry
208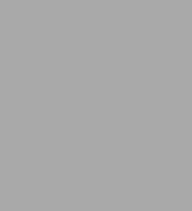
Bemrose on Traditional Woodworking: Carving, Fretwork, Buhl Work and Marquetry
208eBook
Available on Compatible NOOK devices, the free NOOK App and in My Digital Library.
Related collections and offers
Overview
Filled with practical instructions, helpful diagrams, and illustrations of finished projects, this manual presents time-tested techniques that remain valid for modern woodworkers—only the tools differ. A Victorian-era expert on woodworking, ceramics, and decorative arts, author William Bemrose offers tips on choosing the right wood, staining and polishing, and engraving. His projects range from undertakings as small as picture frames, book rests, and letter racks to such ambitious endeavors as bookshelves, chests, cabinets, and screens. A source of useful methods, this book also serves as a wellspring of design inspiration.
Product Details
ISBN-13: | 9780486156262 |
---|---|
Publisher: | Dover Publications |
Publication date: | 01/25/2013 |
Series: | Dover Crafts: Woodworking |
Sold by: | Barnes & Noble |
Format: | eBook |
Pages: | 208 |
File size: | 11 MB |
Note: | This product may take a few minutes to download. |
About the Author
A noted writer on woodworking and ceramics, William Bemrose (1831-1906) was a scion of Bemrose & Sons, a printer of products ranging from religious treatises to railway timetables.
Read an Excerpt
Bemrose on Traditional Woodworking
Carving, Fretwork, Buhl, Work and Marquetry
By William Bemrose
Dover Publications, Inc.
Copyright © 2014 Dover Publications, Inc.All rights reserved.
ISBN: 978-0-486-15626-2
CHAPTER 1
Manual of Wood Carving.
* * *
THE purpose of the present Work is to provide for the amateur carver such information and assistance as will enable him to produce various articles of furniture, tasteful in their character, and durable in their quality. Hence we have illustrated it with detailed designs which are easily carried out, and when completed, will be found worthy of a place in any modern household.
Descriptions of the plates will be found in the accompanying letterpress; and the taste of the carver will guide him in the selection of such designs as may best suit the piece of furniture he intends to produce. We have thought it better to give separate details, and leave the selection to the carver, than arbitrarily to force upon all our readers the same completed design. It is not desirable that a number of pieces of furniture should be made alike in every detail; and the probability is that by leaving the amateur to select for himself, the results will in each instance be far more pleasing, because they will be more varied in their character.
The choice of wood is an important matter, and influences much the progress of the amateur. Dry English oak, walnut, or limetree, are the best woods for carving purposes, but the former is the most durable. The two former are best adapted for domestic and church furniture. It should be chosen of a "kind nature," straight grained, and if prettily grained will be all the better.
A beginner should practise on a soft wood—red pine—until he has mastered the handling of the tools and the difficulties of cutting with and across the grain.
The simplest form of wood carving is "Diaper Carving," which consists in the groundwork, or parts usually cut away in carving, being punched in patterns, thus throwing up the design with such force that the effect is almost equal to carving itself. Most designs of simple character can be utilized for this method of carving.
Furniture made up entirely on this plan is rapidly executed and small pieces look remarkably well; and in larger carved work the "Diaper" is recommended instead of plain end-panels.
The beginner will frequently experience a difficulty in deciding the proportions most suitable for the piece of furniture he is desirous of making ; the best guide is an existing piece similar in character to that required. This can generally be found and measured and the new piece made to scale, either larger or smaller, as may be desired, or any variations can be introduced with a good idea as to how the finished article will appear; failing this, it is best to make a full-sized drawing, showing plan and front and end elevations before commencing the work. The proportion of one part to another is of the utmost importance, so that the whose may be well balanced, as also is the uniformity of period and style selected for the decoration.
Further, a full-sized drawing shows whether the proposed dimensions will be productive of a useful piece of furniture so far as its capacity is concerned, and will be most useful for the cabinet-maker to work to.
The first question which naturally suggests itself to a beginner is as to what outlay is necessary; and therefore at the outset we reply that a few shillings will purchase the tools which are requisite for carving many of the following designs. It will be found most advantageous to employ a cabinet-maker to prepare the wood for carving, and to put the piece of furniture together when carved; although anyone may learn to carve moderately well, it is not easy to put the carved pieces properly together.
Tools (Plate I.).
IN the choice of tools, have those of the best makers, with six or eight-sided handles, 4 inches long. It is requisite for good carving, and pleasure in working, to have the tools as sharp as possible. There are several sizes of each kind of tool, and it will be well to have two or three sizes of each, viz. :—
Entering Chisel (spoon shape). For levelling the groundwork in confined spaces, and where a flat chisel cannot be used. (No. 3.)
Entering Gouge (spoon shape). For hollowing out the undulations in foliage, &c. (No. 4.)
Partying Tool (straight). For the veining of leaves, or cutting the outline of a design. (No. 5.)
Bent Parting Tool. For the above purposes, where a straight tool cannot be used; as in the hollow of a leaf. (No. 5.)
Macaroni Tool. For removing wood on each side of a stalk or vein of a leaf. Skew or Corner Chisel. For removing wood out of the corners of a design, where an ordinary chisel is useless. (No. 6.)
Carving Chisel. For cutting round the design on commencing to carve, also for removing superfluous wood and grounding. (No. 7.) 1/8", 1/4", 1/2", 5/8", 3/4", and 1".
Carving Gouges. For cutting curves and removing superfluous wood. (Nos. 8 and 10.)
Double Bent Fluting Gouge. For removing wood from the hollows of leaves, &c., where a straight gouge cannot be used. (No. 9.)
Oil Stone (Arkansas preferred), and slips or smaller stones to fit the inside of the gouges.
Unless the tools are "set" or sharpened when purchased, they will require to be ground on a grindstone, and as but few amateurs will possess one, it will be well to have them ground and "Set" by a wood carver or cabinet-maker. In "setting" the tools, apply a few drops of sweet oil to the Arkansas stone, and take care not to hold the tool too perpendicularly. In using the gouge slip it should be spanned by the thumb and finger of the right hand, and the shaped side of the slip applied to the inside of the tool, which may be held as in illustration or in a vertical position—cutting edge upwards—in the left hand, the slips can then be worked backwards and forwards as desired, the object being to remove any burr and not to form a bevel. Slips can be purchased of various shapes to fit different tools. Too much attention cannot be given to the state and care of the tools, as neither pleasure in using, nor good work, can proceed from dull instruments. In addition to the above, it will be necessary to have glued to a piece of wood, a strip of thick and soft buff leather, about 12 inches by 3 inches, which should be well moistened with sweet oil, dusting on it some fine emery powder. The tools may be drawn over it occasionally in the intervals of use. The tools are best kept separate, either in wooden trays, or placed under loops of leather sewn on to a piece of flannel or leather, with a flap on each side to prevent them slipping out when the case is rolled up and not in use.
Fig. 2 is a mallet, which should be made of tough wood; they can be obtained in various sizes. Only one size of each tool is shown, but it is requisite to have several sizes of each. Other shaped tools are, however, occasionally required, as those shown are a limited selection.
Figs. 11 to 20 are punches. These the amateur will in most cases himself be able to make; if not, the aid of the whitesmith must be called in. Nos. 11 to 19 are made out of pieces of rod iron, 3 1/2 inches long and 1/4 of an inch thick, the ends being filed or cut to the required shapes; when used, the punch is held perpendicularly, and smart but uniform blows struck with the mallet, the impressions being close together, but separate or distinct from each other.
No. 21 is the point used in tracing the design on to the wood, also as a punch, each dot being distinct. No. 20 is a hollowed-out punch, which forms small button-like impressions. No. 23 is a frame-saw, for cutting fretwork or removing pieces of wood out of carved work, where required, such as perforated carving.
If a work-board, about 18 inches by 30 inches superficially, and 1 inch thick, be obtained and placed upon a firm table, a joiner's bench may be dispensed with, and the carving of small objects carried on in the dining-room, or elsewhere, without at all interfering with the comfort of the household. An improved work-board for small and delicate work can be made (see illustration) so that the centre portion, on which the work is fixed, can be turned round without moving the whole work-board, thus giving greater access to the work from different points and without the carver moving his position. This board is constructed of two thicknesses of wood, a portion in the upper board being turned out so as to admit of what may be termed a turn-table; this is so bevelled at the edge that the circular portion, when inserted from the lower side, before the boards are screwed together, cannot come out, but can readily be turned round at well, or by a screw it can be fixed in any position for the time being. The work is fixed on the turn-table by nails or screws. Although an ordinary table answers most purposes, there is no doubt that a strong workbench, as shown in the accompanying illustration, is far preferable. This improved bench measures 36 inches by 22 inches, and is fitted with a drawer for tools, a bench-screw at the end, and five bench-pegs, which admit all sizes of work to be held firmly whilst being carved; if for a small piece of wood, the peg nearest to the screw is knocked up to the required height, the piece is then placed between it and the screw-peg and screwed up tight. The bench-screw at the end is also adapted for holding wood in a perpendicular position for carving and fret-cutting. The hole in the centre of the bench is for the insertion of the holdfast, as shown in the illustration. The knob being placed upon the wood about to be carved, the screw at the top is screwed up until the wood is immovable. This holdfast is very well adapted for holding peculiar-shaped pieces of wood, and also very thin pieces, which would spring if placed between the bench-pegs. If the work in hand is very small it is best to glue or screw it to a larger piece of common wood, which can then be fastened to the bench or table. Having procured the necessary tools (see Plate I.), and determined upon a design for a panel, the carver first proceeds to transfer the design to the wood. This can be done by drawing, in pencil, direct on the wood, or by tracing from an existing design on to the wood by means of carbon paper. The carbon paper is placed between the design and wood and the outline traced down by a point or pencil. In the case of mouldings, &c., where so much accuracy is not required as in panels, the amateur may pencil the design at once upon the wood. Or in some cases cut a piece of cardboard the shape of the design and draw the pencil round the model, moving the card on as required.
The work being now ready for carving, the operator must take the holdfast (Fig. 1) and screw the work-board and wood to be carved to the table, or to the carving bench, and we should recommend him to begin with DIAPER CARVING, which we now describe.
Instructions for Diaper Carving,
AS APPLIED TO BOOK SIDES, JEWEL BOXES. AND OTHER SMALL FANCY ARTICLES.
THE best wood for these purposes is Walnut. We will choose a book side, t and explain the method of "Diaper Carving."
The wood should be at least a quarter of an inch in thickness, with a bevel from a quarter to half an inch, according to the size of the book. The wood having first been French polished on the face, pin the design (which should be drawn upon tough paper) upon it, and with a fine point (similar to Fig. 21) trace it over, taking care to give sufficient pressure to produce a fine indented line upon the wood, or use carbon paper, as described on page 10. Instead of using the parting tool (Fig. 5) as before described, for large work, use chisels, gouges, &c., according to the shape of the required incision, holding the tools perpendicularly, and with a little downward pressure from the wrist make the indentations. In this style of carving no wood is removed, it being in fact punched with the various tools. Having thus formed the outline, proceed to punch the groundwork of the design as before described.
The wood being liable to warp until fastened to the book, it will be well to paste a piece of brown paper at the back, and when not in use, it should be kept under a weight.
Illuminations on vellum and Wedgwood medallions may be inset with good effect, in panels, centres, &c. In the former case the vellum must be sunk a little below the level of the surface.
For larger work with the parting tool (Fig. 5) cut the outline of the design, holding the tool in the right hand in a slanting direction (see illustration on previous page); the left hand should be hollowed and rest on the tool; the wrist and tips of the fingers resting upon the work to steady the hand and prevent the tool from slipping forward. The tool is thus easily guided round the curves, &c., or for finer work the outline may be incised by chisels and gouges. This being done, the panel has to be stained (see Staining, p. 18), and when dry, the ground work of the design is to be punched with one or other of the punches (Figs. 11 to 20). The punching throws up the design and gives it a rich relief, and, when the work is well varnished, this simple method of carving has a most pleasing effect.
Carving in Relief.
IF the work is to be carved with the pattern standing up in relief, the carver proceeds as before directed, except that, instead of the parting tool, a chisel (Fig. 7) or gouge (Fig. 8) is used, taking care that the tool fits the outline of the design, particularly where curves occur. When carving by pressure the handle of the carving tool should be held firmly in the right hand, the left hand resting on the tool in front so as to steady the blade, the left arm and wrist rest on the work and so enable a readier adjustment of the tool to the design. This not only steadies the pressure applied by the right hand, but also prevents the tool slipping forward. If these instructions are followed there can be no danger of injury either to the hands or work. With hard wood, or when a greater depth is required, the same tools are used, holding them perpendicularly a little away from the design so as not to crush the edge, the blade of the chisel or gouge being held between the thumb and fingers, the little finger resting on the wood to steady it whilst giving the handle a smart stroke with the mallet. This being done, he next, with a small gouge, scoops out the parts to be cut away, and uses the chisels (Figs. 3 or 7) to level the ground to an uniform depth, carefully cutting close up to the design without using the mallet. The levelling may be done by using a kind of router, the blade of which is set to the desired depth and worked like a plane to suit the grain; this is done before the portion in relief is carved up. Then the grain of the wood must be observed, not merely as to whether the carver is cutting across or along the grain, but whether up or down (as in planing), so that the chips may come out clean, instead of tearing deeper than is wished. If the grain run downwards, turn the wood round and work the reverse way, or sideways. The work is now said to be boasted. The raised design is then roughly cut or grooved, according to the drawing, using the different sized chisels and gouges according to the shape of the modelling required. When the proper effect of relief is obtained, proceed to finish the work by going again carefully over it. Always be careful to take too little off rather than too much; more wood can be removed, but none can be added thereto. In imitating the veins of leaves, &c., the amateur had better at first sink them by using the parting or macaroni tools, and, when more proficient, proceed to cut raised veins. Some carvers gain additional steadiness by passing the little finger underneath the blade, as by this means the edge or point is more easily applied to the exact spot. In preparing heavy work, and using a large mallet, it is a great relief to acquire the habit of laying the latter on the work-board between the strokes, while adjusting the chisel for the next blow. The panel can now be left of the natural colour, or, if preferred, it can be oiled, bees-waxed, varnished, or stained and varnished (see page 18), and the groundwork punched or left plain at the option of the carver.
(Continues...)
Excerpted from Bemrose on Traditional Woodworking by William Bemrose. Copyright © 2014 Dover Publications, Inc.. Excerpted by permission of Dover Publications, Inc..
All rights reserved. No part of this excerpt may be reproduced or reprinted without permission in writing from the publisher.
Excerpts are provided by Dial-A-Book Inc. solely for the personal use of visitors to this web site.
Table of Contents
Contents
DOVER BOOKS ON WOODWORKING AND CARVING,Title Page,
Copyright Page,
Introduction to the Dover Edition,
A Manual of Wood Carving,
Manual of Wood Carving.,
Tools (Plate I.).,
Instructions for Diaper Carving, - AS APPLIED TO BOOK SIDES, JEWEL BOXES. AND,
OTHER SMALL FANCY ARTICLES.,
Carving in Relief.,
Perforated Carving.,
Staining and Polishing.,
Inlaying.,
Engraving and Shanding.,
Decriptions of Plates.,
Fret Cutting and Perforated Carving,
PREFACE.,
FRETWORK.,
CARVED FRETWORK.,
SUGGESTIONS AND EXPLANATIONS OF THE DESIGNS.,
Manual of Bull-Word and Marquetry,
TOOLS.,
BUHL-WORK.,
MARQUETRY,,