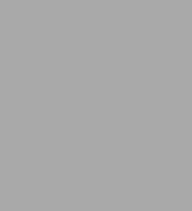
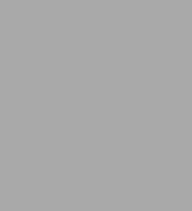
Paperback
-
PICK UP IN STORECheck Availability at Nearby Stores
Available within 2 business hours
Related collections and offers
Overview
Product Details
ISBN-13: | 9781466982871 |
---|---|
Publisher: | Trafford Publishing |
Publication date: | 05/16/2013 |
Pages: | 100 |
Product dimensions: | 8.50(w) x 11.00(h) x 0.26(d) |
Read an Excerpt
Freehand Machine Embroidery
Beginners Guide - Volume One
By Maggie Kruger
Trafford Publishing
Copyright © 2013 Maggie KrugerAll rights reserved.
ISBN: 978-1-4669-8287-1
CHAPTER 1
BASIC REQUIREMENTS:
Sewing Machine and all the basic requirements
Your sewing machine will need to have bobbins, darning foot or embroidery foot and an instruction manual. It is important that the feed dog (known as teeth) can be lowered or that there is a cover-plate to cover it. If your machine has neither of these, masking tape can be placed over the teeth.
Machine Needles:
The thread should slip through the eye easily to avoid fraying. The needle must be very sharp.
Types of needles to use are the Embroidery and Jeans needles. Both of these have large eyes and are easier to thread and are sharp.
Change your needle regularly to prevent damage to the thread, even a slightly damaged needle can cause threads to keep on snapping or skipped stitches, and it can break if stitching over the thicker parts of the embroidery.
Use a size 90/14 needle – this does not break easily and is good for practice.
Use a size 75\11 for embroidery.
Embroidery – Sharp with a large eye and groove, plus special coating and large scarf; prevents abrasion and shredding of delicate threads, especially metallics and rayons.
Universal – Used for most fabrics including wovens and some knits.
Ball Point – Rounded point penetrates between – rather than through – fabric yarns, preventing damage to knit fabrics.
Stretch – Rounded point similar to ball point.
Metalic – Designed to prevent abrasion of delicate metallic threads.
Double\Twin – Two or three needles attached to one shank.
Jeans\Denim – Sharp point for penetrating denim, plus stiff shaft to prevent bending and breaking. Large eye.
Wing – Sharp point with a non-cutting wing on each side; each stitch creates a small hole in the fabric without cutting; for hemstitching.
Scissors:
Good quality scissors for fabric and a small sharp embroidery scissors with fine points to cut loose threads close to the stitching. Those with curved points work the best.
Tweezers:
Useful for removing threads that may be wound around the bobbin case or jammed in the feed dogs.
Lint Brush:
These are usually supplied with the machine to remove the lint that builds up around the bobbin case and feed dogs. A small soft paint brush can also be used.
Sewing Machine Oil:
Some newer machines are self lubricating. Others require oil. Use oil sparingly and only use sewing machine oil.
Dressmakers carbon paper – tracing designs. Place the carbon paper between the design and the fabric and draw over the design with a sharp pencil or ball point pen.
Blue Pen – water soluble pen – tracing designs
Pritt Glue:
Light applications of glue are useful to hold motifs down while sewing them on.
Fabric Glue – Temporary Fabric Adhesive spray - Aerosol Can – comes in small or large tins
Fray Check –a small bottle of liquid – used for cut away edges of fabric to prevent it from fraying
Vilene Trace – Vilene for tracing patterns.
Light Box – A light under a glass in a box, or hold the fabric and design up against a glass window.
File:
A file with plastic sleeves for your samples.
Press and trim them neatly then paste on A4 paper and place in the plastic sleeve. Place in your file.
Stabilizers:
This is used for a backing on certain types of fabric.
* Stitch and Tear – tears off easily after embroidery – Normal fabric
* Iron-on Stitch and Tear for Knits
* Water soluble - Vilene type – for fabric and lace
Fabrics:
A firm, closely woven fabric will give the best results with machine embroidery; other fabrics may be backed with stabilizers. Calico is very good to begin with, for practicing and even for light-weight embroideries.
If the fabric is not firm enough, back it with water soluble Vilene This washes away when rinsed in water, or use Stitch 'n Tear, which will tear off after embroidering. The stabilizer helps to prevent puckering and the stabilizer adds to the firmness of the fabric.
Spray the water soluble Vilene with a little temporary adhesive spray (for fabrics) and press onto the back of the fabric square. Hoop both layers.
For Stitch'n Tear stabilizer - Hoop fabric first and then place stabilizer under hoop when it is in the machine ready to stitch.
Silk, Organza, tulle and net is an excellent fabric for light-weight embroideries. With these fabrics you will need to use water soluble Vilene as the design will have to be traced on the water soluble Vilene, and the same with toweling, and knit fabrics.
Embroidery Hoop:
Wooden embroidery hoops approximately 15 to 20cm in diameter, 1cm in depth, are best sizes to use. The embroidery hoop must be narrow to fit under your machine needle at its highest point and the hoop must have an adjustment screw, which can be tightened with a screwdriver.
The hoop should also be smooth, so it does not snag the fabric or scratch the bed of the sewing machine.
A larger hoop will knock the body of the machine from the movement of the hoop while you are embroidering, and the fabric will not stay drum tight as the movement of the hoop and stitching of the embroidery can loosen the fabric therefore the smaller the hoop the more tightly the fabric will be.
It is a must to have at least two hoops – one for practicing for colour and techniques, the other hoop for the actual embroidery piece, as mistakes are very difficult and hard to unpick. The second hoop can be a smaller one – 15cm.
Threads:
There are a variety of threads designed especially for machine embroidery work. Almost any thread will work if the sewing machine is properly adjusted. You may want to try a variety of threads to find the one that works best with your sewing machine.
Special effects of texture and design can be created with different types of thread. The thread should fill in the design smoothly and create a silky shine or a matt look and it should not break easily as you work.
Threads used for freehand machine embroidery can be cottons, rayons, polycottons and metallics. For metalic thread a Metalic needle should be used, the larger eye prevents the thread from fraying. Check upper tension, maybe the tension will have to be loosened.
Crochet cotton, wool and different novelty yarns can also be used for special effects.
The knit fabrics needs iron-on Stitch 'n Tear on the back, where the embroidery will be. Cut a piece large enough for embroidery and iron on the back of fabric. This will keep it from stretching when placed in the hoop. Stitch 'n Tear can be torn off after embroidery has been done
Design:
The design for embroidery can be anything you wish.
Select designs from ordinary hand embroidery designs, colouring books, pictures or create your own interesting shapes and designs.
After a design is selected, it must be transferred to the fabric. This can be done with dressmaking carbon or a water soluble pen. Do not use a ballpoint pen as the ink might stain and may not wash out. A pencil can be used but must be covered with embroidery as the lead does not wash out. Do not use a pencil when working with white embroidery thread only, as it will come out grey.
HOW TO WASH EMBROIDERY
Soak embroidered article in luke warm water with a few drops of dishwashing liquid. Rinse in clean water.
Take out of the water, while sopping wet and lay it on a clean dry towel and roll up together. Shake out all the excess water.
Lay the nearly dry article on a clean towel or dry clean surface and leave until slightly damp, then iron.
Ironing of Embroidery Article
For normal ironing, the article is placed upside down onto a surface, which has been covered with a towel, and steam pressed.
A not too bad pulled surface which is the result of a poor tension in the embroidery hoop, can be rectified by wetting the article thoroughly, towel dry, and then press it on the wrong side. Place it in a larger embroidery hoop and stretch it till all the puckering and folds are out and leave for a day or two.
Working Area
Work in a well-lit area as freehand machine embroidery can put a lot of strain on the eyes.
Adjust seating so that you can see the top of the work. Sit in front of the needle. Your chair should be pulled well in for good back support.
Push the machine back as far as possible on the working surface, in order to rest your left elbow on the table and left hand on the edge of the machine bed. In this position you will be able to move the hoop more evenly.
CHAPTER 2
INTRODUCTION TO YOUR MACHINE
How a Sewing Machine Works
A sewing machine uses two continuous threads to make a line of stitches.
The first comes from a reel of thread which is held on top of the machine on a cotton holder above the fabric and goes down through the eye of the needle.
The second thread is wound onto a bobbin which is located in the base of the machine below the fabric.
The machine needle is held in the needle bar with a screw, and moves up and down vertically. When it moves through the fabric, it enters the base of the machine and locks with the bobbin thread to make a stitch.
The machine needle is moved up and down by power generated by electricity.
The Feed Dog
The fabric is moved forward for each stitch by the movement of several rows of little steel teeth, set into the bed or base.
These teeth move every time the needle moves. They are called the feed dog.
The Presser Foot
The fabric to be sewn is held down in position by a presser foot, which is controlled by a presser foot lever. The presser foot lever also controls the tension – when up there is no tension when down there is.
Preparing the machine:
Before attempting to embroider with your machine, read the machine manual for specific instructions, be sure you understand the various adjustments and settings that your machine requires for machine embroidery.
When a sewing machine is used for embroidery, it should be clean, well oiled, and in good running order and it requires cleaning and oiling regularly. When you clean the machine, remove all the fluff and oil it lightly following the manufacturer's instructions in the handbook.
Some of the newer models do not need oiling.
Check carefully for excess oiliness that could stain your project. Wipe the needle, needle bar, needle plate, and entire work surface of the machine carefully before stitching is begun As mentioned before that any sewing machine with a straight and zigzag stitch can be used. There are however, certain features on a machine, which will make freehand machine embroidery much easier.
* Practical and decorative stitches
* Different motor speed settings
* Needle stop function
* Easy adjustment of feed-dog control
* Comfortable large sewing table – Singer Sewing Machine – Model 9960
TENSION
Preset thread tension
Upper and bobbin thread will lock approximately in the middle of fabric.
When thread tension is increased
Bobbin thread will appear on the top side of fabric.
When thread tension is decreased
Upper thread will appear on the bottom side of fabric.
Thread tension for zigzag stitch
Thread tension for zigzag stitch is set to a slightly lower tension than when sewing straight stitch. You will obtain a nicer stitch when upper thread appears on bottom side of fabric.
Correct thread tension is very important for machine embroidery. The top tension usually needs to be looser than the bottom.
Adjust the machine to allow the bottom tension to pull the top thread down showing slightly on the under side of the fabric. It should not be too loose to cause loops on the wrong side of your work. See Picture C as above.
A looser tension will also stop the thread from breaking when moving hoop fast and slow and the thread will lie smoothly in machine embroidery.
It will also pucker the fabric less in satin fill-in embroidery, and will prevent the bobbin thread from showing through on the right side of the work.
If you are still bringing up bobbin thread even with the top tension all the way to zero, you may need to tighten your bobbin tension by slightly turning the bobbin tension screw to the right.
Darning Foot:
Most machines have a darning foot. If not, freehand machine embroidery can be done by removing the foot altogether, but be careful of your fingers.
The darning foot is designed not to put any pressure on the fabric, but will prevent the fabric from lifting when the needle comes out of the fabric after a stitch has been formed. It may be that certain machines will only perform while it is attached.
Many sewing machine shops keep accessories for very old, as well as new machines.
When doing freehand machine embroidery it is important to have as much visibility as possible. Darning feet are closed in front, some are open. The front of your darning foot needs to be cut if closed. This will improve visibility. See your sewing machine dealer
SET UP YOUR MACHINE FOR FREEHAND EMBROIDERY
Singer Model 9960
This machine has all the features and all the accessories and the large sewing table needed for freehand machine embroidery.
Instruction Manuel 9960
Centre Needle Position
1. Lower the feed dogs by moving the drop feed lever to the left.
2. Remove the presser foot and holder.
3. Arm of the darning/embroidery foot should ride onto the shaft of the needle clamp screw.
4. Slide the plastic attaching head from your left to right so that it is fitted into the presser bar.
5. Tighten the presser foot thumb screw.
MACHINE SETTINGS:
Slow motor speed (if available)
Drop or cover the feed dog (as for darning)
Set the machine for straight stitch
Darning or embroidery foot.
Extension Table – This gives you a wide sewing space so that the hoop can lie flat on the table.
Stitch Length:
Set the stitch length to '0', to stop the feed-dogs moving. The stitch length setting controls the back-and-forth movement of the feed-dogs.
If you cannot set your machine at '0' select the lowest possible number. Some machines prefer to have a small amount of stitch length.
Stitch Width:
Set the stitch width to '0'
Put in a new 90\14needle. An embroidery needle or Jeans needle if it is available.
If your machine has an extension table, you will need to put it on to give you a wider area on which to place your hoop on.
Stitching:
Remove your foot from the foot control when threading up. Thread the machine with ordinary sewing thread. Fill the bobbin with a white or you can use one of your bobbins that is filled with cotton already. In this way you can empty all your full or half filled bobbins.
Pull up your bottom cotton thread
Always pull up your bottom cotton thread before you start sewing. Hold the top thread out to the side, turn the flywheel one turn and as the needle comes up and out of the needle plate, pull the thread up and out to the side, bringing the bobbin thread with it.
CHAPTER 3
PREPARING THE FABRIC AND THE HOOP FOR FREEHAND EMBROIDERY
It is best to wash your fabric first to pre-shrink it. Press the fabric to remove any creases.
The size of the fabric to be worked on, should be a square at least 5cm wider than the diametre of the hoop.
If the design is too large for the hoop, you will need to move the hoop.
Embroidery Hoop
The inner ring of each hoop should be bound with cotton tape, 1.5 cm wide, to hold the fabric more firmly and to prevent your work from slipping.
Secure one end of narrow, cotton tape to inner ring of the hoop with fabric glue. Wrap ring in diagonal direction, over lapping tape by half its width, pull firmly while wrapping. Secure other end of tape with glue. Allow glue to dry before using the hoop. If you find that the screw is too small now that the inner ring has been taped, you can buy a longer one from a hardware store.
The fabric is placed on the underside of the hoop, that is, the opposite way around to hand embroidery the back of the fabric should to be touching the table.
For freehand machine embroidery you stitch in the inside of the hoop.
Placing the fabric in the hoop – this is the foundation of your embroidery.
The fabric should be placed tightly in a 15cm or 20cm hoop that has an adjustment screw.
Separate the hoop and loosen the adjustment screw slightly.
It is important that the fabric to be worked on in the embroidery hoop is pulled firm, evenly stretched and very tight - drum tight.
If your fabric is not properly stretched in your embroidery hoop, your embroidery will never look right. It will become distorted and puckered. Puckers never press out. Loose fabric can cause needles to bend or break, threads to snap, and skipped stitches.
Stand at your table and place the outer ring (larger ring) on a flat surface and centre the fabric on the hoop with the design up. Place the inner ring (smaller ring) that has been bound with cotton tape, over the fabric and press down into the outer ring, securing the fabric in the hoop.
Tighten the adjustment screw while pulling the fabric around the edges until it sounds like a drum when tapped. Whilst tightening the fabric, make sure that the grain lines are kept straight, pull carefully.
(Continues...)
Excerpted from Freehand Machine Embroidery by Maggie Kruger. Copyright © 2013 Maggie Kruger. Excerpted by permission of Trafford Publishing.
All rights reserved. No part of this excerpt may be reproduced or reprinted without permission in writing from the publisher.
Excerpts are provided by Dial-A-Book Inc. solely for the personal use of visitors to this web site.
Table of Contents
Contents
INTRODUCTION.................... 6
PART ONE....................
CHAPTER ONE....................
CHAPTER TWO....................
CHAPTER THREE....................
CHAPTER FOUR....................
CHAPTER FIVE....................
CHAPTER SIX....................
PART TWO....................
STITCHES.................... 37
LESSON ONE....................
LESSON TWO....................
LESSON THREE....................
LESSON FOUR....................
LESSON FIVE....................
LESSON SIX....................
LESSON SEVEN....................