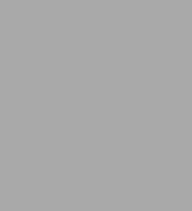
Handmade Tile: Design, Create, and Install Custom Tiles
208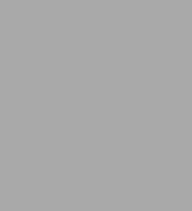
Handmade Tile: Design, Create, and Install Custom Tiles
208eBook
Available on Compatible NOOK devices, the free NOOK App and in My Digital Library.
Related collections and offers
Overview
Handmade Tile is a contemporary guide for ceramic artists and anyone interested in custom tile installations—from making, designing, and decorating to designing your space and installation.
No matter how many years of experience you have as a ceramic artist or how many home-improvement projects you’ve tackled, nothing prepares you for the unique world of ceramic tile. From concept and design, through firing and installation, ceramic tiling is one of the few places in a home where art is permanently installed as a feature of a room.
In Handmade Tile, Forrest Lesch-Middelton shares everything he’s learned as the founder and owner of the custom tile business FLM Ceramics and Tile. From his years as a one-man operation to his current production facility, Forrest has seen it all and helps you every step of the way. Whether you want to make your own tile, or want to use artistic and custom-made tile in your home, this book has everything you need.
Key features of the book include:
- Making Tile: key tools, rolling, cutting, extruding
- Decorating: glazes, image transfer, cuerda seca, underglaze, slip
- Designing Your Space: tile in context, choosing your tile, codes and standards
- Installation: removing old tile, backing, preparing surfaces, setting, grouting
Galleries and interviews with today’s top workings artists in tile round out the package. Featured artists include Allison Bloom, Boris Aldridge, Disc Interiors, PV Tile, and more.
Product Details
ISBN-13: | 9780760364314 |
---|---|
Publisher: | Quarry Books |
Publication date: | 09/17/2019 |
Sold by: | Barnes & Noble |
Format: | eBook |
Pages: | 208 |
File size: | 44 MB |
Note: | This product may take a few minutes to download. |
About the Author
Forrest Lesch-Middelton is the owner of FLM Ceramics and Tile in Petaluma, CA. His work has been widely featured, including the cover of Ceramics Monthly, The New York Times, Architectural Digest, and American Craft Magazine. In 2013, Ceramics Monthly and Ceramic Arts Daily chose Forrest as “The Ceramic Artist of the Year.” Forrest is the former president of The Association of Clay and Glass Artists, a graduate of Alfred University’s ceramics program as well as Utah State University’s MFA program, a former resident of Watershed Center for Ceramic Arts, a McKnight Fellow at Northern Clay Center, a recipient of the Creative Work Fund Grant, and former program director for Sonoma Community Center Ceramics. Forrest has taught at various Bay Area colleges and has lectured and demonstrated extensively throughout the United States, including workshops at The Penland School of Craft, The Arrowmont School of Arts and Crafts, Syracuse University, Greenwich House Pottery, the California College of the Arts, and The Northern Clay Center.
Forrest Lesch-Middelton is the owner of FLM Ceramics and Tile in Petaluma, CA. His work has been widely featured, including the cover of Ceramics Monthly, The New York Times, Architectural Digest, and American Craft Magazine. In 2013, Ceramics Monthly and Ceramic Arts Daily chose Forrest as "The Ceramic Artist of the Year." Forrest is the former president of The Association of Clay and Glass Artists, a graduate of Alfred University's ceramics program as well as Utah State University's MFA program, a former resident of Watershed Center for Ceramic Arts, a McKnight Fellow at Northern Clay Center, a recipient of the Creative Work Fund Grant, and former program director for Sonoma Community Center Ceramics. Forrest has taught at various Bay Area colleges and has lectured and demonstrated extensively throughout the United States, including workshops at The Penland School of Craft, The Arrowmont School of Arts and Crafts, Syracuse University, Greenwich House Pottery, the California College of the Arts, and The Northern Clay Center.
Read an Excerpt
CHAPTER 1
The Basics
It's true that, in its most basic definition, ceramic tile is a slab of clay cut into a shape and used as a means of decorating and protecting a surface. However, tile can also be a window through which we can glimpse our own history.
I admit that when I first started making tile, I didn't have a clear understanding of which lens to view it through. Although I encountered tile on a daily basis, it was rarely something I noticed. I soon found that if you pay attention, you will see that tile can tell a story. First you must understand the language of tile to understand what it has to share.
In this chapter, we'll take a brief look at tile's history, we'll learn key terminology that will be important throughout the book, and we'll also examine a few key types of tile as well as a handful of common setting styles. Though it's impossible to provide a complete crash course in the history of tile, my hope is that this chapter will begin to change your perspective, so you, too, will fall in love with this unique medium.
Tile Throughout History
Fired clay is one of the oldest and most enduring manufactured materials on earth; it bares record of the time and place that it was created. In many parts of the world, tile is the most lasting documentation of the people and places in which it is found. The cultural shifts, the commercial and social influences, and the hands in which it was created (and used) are forever ingrained upon its surface. Tile is unique even within the history of ceramics, as its durability and commodification ensure its lasting mark upon and from the history of humanity. Tile alone is the single greatest user of the world's clay resources, and because of this it is both revered and overlooked as a design material.
TILE BEFORE THE EARLY TWENTIETH CENTURY
Because of the durability and the relative ease in which ceramic tile is produced, it was used like a skin to cover and protect the sacred buildings of the world's oldest civilizations. As religions evolved, and texts faded and were rewritten, tile is often the most lasting record of the people who came before. Some of the oldest examples of tile are glazed brick from the Pre-Iranian, Elamite civilization circa the third millennium BCE. These brick tiles were used to construct ziggurats and record the legacies of the rulers who had constructed them.
As more enduring and lasting ceramic wares developed, so did the glazed brick and ceramic tile that was used as an architectural and aesthetic material surpassing the strength and beauty of common earthen brick. One of the most famous examples of ancient ceramic brick tile is the Ishtar Gate commissioned by King Nebuchadnezzar II. Constructed in approximately 575 BCE, the immense Ishtar Gate was the eighth gate of the inner city of Babylon. It was skinned in glazed brick meant to mimic the coveted lapis lazuli, with bas-relief animals and lowers glazed with golden earth tones representing Babylonian gods and goddesses. The Ishtar Gate, being part of the Walls of Babylon, was one of the original Seven Wonders of the World. As its cedar beams and earthen walls crumbled, the ceramic endured. In the photo opposite, you can see how it was reconstructed in the twentieth century. It is now housed in Berlin's Pergamon Museum.
As ceramic technology developed, we began seeing the inconceivably beautiful glazed brick and mosaic tile work that became synonymous with Islamic architecture beginning around the twelfth century. There is no substitute for the scrolling Kufic calligraphy and mind-bending geometric patterns on tile that arose from this period, adorning the great mosques and palaces of the time. We owe a great debt of gratitude to the dedication and elevation of ceramic tile of the Islamic world, as it heralded a global fascination with tile that spread across Northern Africa and into Europe through the Iberian Peninsula, and even into East Asia through both land and sea. As Moorish influence brought techniques such as zellige and cuerda seca across the region, they defined an aesthetic that is still a part of daily life in areas of Spain, Italy, and beyond.
From here began the golden age of tile, starting with porcelain and underglaze influences from Chinese trade along the Silk Road. Iznik, a city in Northern Turkey, went from a thriving earthen-ware pottery center to one of the most influential regions in the history of ceramics. The world experienced the unimaginable crossroads of East and West as the European thirst for Chinese porcelain paired with the Islamic aesthetic and development of underglazed fritware and tile. The deft hand of the Iznik painters combined the best of Chinese floral motifs with unique interpretations of Persian girih tessellations and mosaic to create electrifyingly vivid tile that adorns the palaces and mosques throughout the region to this day.
Forging its place at the top in the vast lexicon of architectural adornments, ceramic tile has become commonplace in virtually every part of the world. Each region now has its own tile history: from the maiolica in-glaze that defines the tile traditions of Spain and Italy, to faience tile in France, and of course Delft tile of the Netherlands with its omnipresent Dutch country scenes directly reminiscent of Chinese blue and white wares. Then there is the tile of the Americas, including the Mexican tile so popular in Southwestern architecture as well as the tile powerhouses that arose during the industrial revolution, including the American Encaustic Tiling Company of Zanesville, Ohio (once the largest tile company in the world) and the Moravian Pottery and Tile Works of Doylestown, Pennsylvania (founded by one of my personal tile heroes, Henry Chapmen Mercer).
CONTEMPORARY HANDMADE TILE
Now that you have some understanding of the rich history of tile, imagine adding the technological and scientific advancements of the last one hundred years to the picture. Ceramic engineering, as well as affordable and accessible fossil fuels, technological advancements in kilns, more robust mining practices, and the ability to source information from across the world at the push of a button have all played a key role in the growth of the tile industry. There are very few limitations, and yet somehow at times it seems like the world of commercial tile has become somewhat stiff. Mass production, though tremendously beneficial for the development of cheaper and more durable tile, often sacrifices aesthetic. It often takes for granted the true potential of the medium.
Although there is no substitute for the unique qualities and tactile nature of handmade tile, many makers today employ modern practices to achieve higher output levels in order to remain competitive in a field dominated by industry. These practices, coupled with a constant eye on aesthetics, and awareness of history and historic practices, can create the perfect marriage of artist and producer.
Like vessel makers, those who make tile by hand can fall into a few categories. I categorize them as "architectural tile makers," "tile muralists," and a third category I call "tile artists." These three categories can overlap and do share some similarities — and many who make tile do all three — but for the sake of conversation I find it easiest to speak about them this way.
Someone who makes modular tile designed to be used functionally makes architectural tile. This type of tile is meant to be used to protect as well as beautify a space. Architectural tile makers often sell tile by the square foot rather than by the installation. Although primarily made by hand, these tile makers can also employ the use of machinery. Those who make architectural tile usually have a method for making tile en masse, producing hundreds, even thousands, of tiles that are similar in appearance and made for covering and protecting specific areas. (I could be considered someone who makes architectural tile.)
Tile muralists primarily make permanent, project-based work that is different from location to location and has a certain theme. The work is like a permanent painting made with tile. A muralist would not fulfill an order by the individual piece or by the square foot, but by the whole project. Mosaic artists are muralists. Muralists often work within the public art spectrum.
Tile artists are not always bound to the medium. They use tile as a means to an end within a single piece of artwork that could illustrate something completely outside the realm of tile itself. Here the object stands alone and can often be impermanent or unafixed, like a piece of sculpture or a painting. A tile artist has free reign with the medium, with the only thing holding them to the category of tile at all being the tile itself. Jim Melchert, Robert Sperry, Kala Stein, Jason Green, and Jim Bachor are just a few examples of tile artists.
Understanding Tile
Ceramic tile encompasses a broad spectrum, from a covering in a subway that's designed to keep it sanitary to a one-off handmade accent tile or coaster. As a potter, I developed the mindset that industry is competition. However, over time I've grown comfortable with the idea that handmade and industrially made pots and tile can coexist synergistically. For example, in 1974 Kohler developed an artist-in-residence program where artist participants integrate with Kohler staff and technology and are encouraged to develop new ways of thinking and making. Similarly, the European Ceramic Workcentre in the Netherlands invites artists, designers, architects, and technicians to work side by side, share ideas, and grow new understandings of the medium.
In the field, many designers I work with will often use industrial tile to maintain affordability and consistency for their clients throughout a project, and then use handmade tile to bring a more personal feel, adding character and context to a job. As a tile maker, I welcome this crossover as it allows me to see my tile in a greater context and understand its use better. Let's explore this intersection.
INDUSTRY VS. HANDMADE
There used to be a time when a machine-made object, or even a machine itself, was thought of as a novelty. We fantasized about a romantic future when Jetsons-style automatons would serve us dinner, and we would communicate by simply speaking into a picture box. Now we depend on machinery for virtually everything, even building more machinery. All day long we work from behind a desk depending on computers and machines to provide consistent results down to the millionth of an inch, and then we come home exhausted from staring at a box all day. We remind ourselves how important it is to get our hands dirty by toiling in the kitchen, gardening, taking hikes, or even taking a pottery class at the local community studio. We crave narrative. An object's visual history reminds us of our actual history; it makes us feel whole. Our acute appreciation for objects with laws and eccentricities arises out of a desire for the things we can no longer have enough of: things that are rare and things made by hand. We take in and elevate these handmade objects because they tell us a story rather than provide us with answers.
As this book progresses, you will see references to industry and production methods that are favored by certain tile makers. With tile, the term "hand-made" can have a relatively loose connotation, and you will notice that at times the line between mass-produced and handmade tile may blur to some degree. We will explore a number of ways that you can make tile by hand, and even include equipment to make your life easier while still staying within the realm of the handmade.
I consider handmade tile to be any tile that is either primarily formed or decorated by hand. Many of the tiles in this book are made from methods that purists might consider suspect; artists use machines to form the tile, and yet they may decorate, cut, sand, load and unload it from the kiln, ire it, and pack it by hand. They touch each and every tile, and when you see the final product, there is no question that even with the aid of computers and machines, it is truly handmade.
This book is not meant to be a purist's approach to handmade tile, but one that I hope will encourage you to experiment with different methods that may benefit your level of production — wherever that may lie. From a single backsplash in your own home to owning a small business that depends on machinery to stay competitive, my goal here is to present a broad view of what it can mean to make handmade tile and to give you permission to play and experiment with it.
NOMENCLATURE
There are a few important terms and phrases you should know before launching into making or setting your own tile. Even after a lifetime of working with clay, when I first jumped into making tile I found myself unprepared to speak about my own work within the greater context of the field. This left me at a detriment when speaking with designers and tile setters. For this reason, I want to quickly lay out some words and phrases that might be helpful for you when making, installing, marketing, and speaking about your own tile.
Accent tile:Tile that is often decorative or different and used as an accent within an installation.
Base layer or backing:Any base material over which tile is meant to be installed. Common names are cement board, HardieBacker, and cementitious layer.
Bullnose tile:Tile with a finished edge that is meant to be exposed.
Buttering or back buttering:Spreading an adhesive coat to the back of a tile prior to setting rather than setting the tile in the adhesive.
Caulking:A water-resistant sealing material (usually silicone) designed for filling grout lines when water resistance is paramount, such as in showers.
Ceramic tile:This category describes tile that is more durable than terra-cotta tile, yet less than porcelain tile. Ceramic tile is a cousin to porcelain tile, but it has an absorption rate greater than 0.5 percent.
Cure/cured/curing:The time in which an adhesive or sealant must be left undisturbed to be considered usable and at full strength.
Epoxy:A two-part adhesive that consists of a bonding resin and hardening catalyst. Epoxy is time sensitive, and the two parts must be mixed together to be activated.
Epoxy grout:A two-part (or three-part) grout that consists of an epoxy resin and hardening catalyst. Epoxy grout is time sensitive, and the two parts must be mixed together to be activated.
Field tile:The primary covering tile in an installation. Often blank tile.
Float:There are a few types of floats. A tile float is a rubber rectangular tool (about 3"×10" [7.5 ×25.5 cm]) with a handle used to push grout into grout lines. A cement float (or bull float) is a long-handled tool with a large lat metal piece on the end used to smooth out concrete after it is poured.
Floating:A method of laying tile without attaching it to the sub floor; the tile is literally attached to itself only. This is also the term used for smoothing and finishing a concrete surface.
Floor tile:A tile that can withstand floor traffic and has enough traction to minimize slip and fall concerns.
Glazed tile:Tile that has a glazed face. Glaze is used to protect and beautify tile.
Grout:A cement-like material used for filling joints between tile. It keeps tile bonded together and makes an entire surface act like one whole object rather than multiple pieces.
Impervious:Tile that does not absorb moisture. It is fully vitrified.
Notched trowel:A grooved or notched trowel used for applying mortar.
Pointer:A small handheld spatula type tool for applying mortar and cement.
Porcelain tile:This is the most durable and impervious tile available. It has a water absorption rate of 0 .5 percent or less. Porcelain tile is fine grained, fully vitrified, and is usually dry pressed by machine.
Quarry tile:Large, machine-made, and unglazed ceramic floor tile that is more than 6" (15 cm).
Setting tile:Adhering the tile to a surface with the use of tile mortar or adhesive.
Spacers:Rubber inserts designed to evenly space individual tiles from one another to form a consistent grout line when setting tile.
(Continues…)
Excerpted from "Handmade Tile"
by .
Copyright © 2019 Quarto Publishing Group USA Inc..
Excerpted by permission of The Quarto Group.
All rights reserved. No part of this excerpt may be reproduced or reprinted without permission in writing from the publisher.
Excerpts are provided by Dial-A-Book Inc. solely for the personal use of visitors to this web site.
Table of Contents
Foreword, 4,
Introduction, 8,
CHAPTER 1 | THE BASICS, 10,
Tile Throughout History, 13,
Understanding Tile, 20,
Types of Tile, 25,
Artist Feature: Boris Aldridge, 31,
CHAPTER 2 | MAKING TILE, 32,
Clay Considerations for Tile, 34,
Artist Feature: Bobby Silverman, 43,
Rolling Slabs for Tile by Hand, 44,
Rolling Slabs for Tile with a Slab Roller, 49,
Cutting Clay into Tiles, 54,
Extruding Tiles, 62,
Making a Tile Mold, 65,
Using a Tile Mold, 71,
CHAPTER 3 | SURFACE: GLAZE, DECORATION, AND FIRING TILE, 74,
Surface, 76,
Artist Feature: Gordon Bryan, Blue Slide Art Tile, 81,
Testing Your Clay and Glazes, 82,
Glazing, 88,
Applying Glaze, 90,
Decorative Ideas, 97,
Image Transfer: Printing on Clay, 102,
Artist Feature: Susanne Redfield, founder of Kibak Tile, 109,
Cuerda Seca (Dry Cord), 112,
Plaster Transfer, 118,
Firing, 122,
CHAPTER 4 | DESIGNING YOUR SPACE, 128,
Artist Feature: David Dick and Krista Schrock, DISC Interiors, 131,
Understanding Tile in the Context of Your Home, 132,
Designing with Tile, 140,
Artist Feature: Allison Dehn Bloom, 145,
Choosing Your Tile, 148,
Measuring a Space for Tile, 160,
CHAPTER 5 | INSTALLATION, 166,
Do it Yourself?, 169,
Removing Old Tile, 170,
Backing and Preparing the Subfloor, 172,
Setting the Tile, 176,
Final Sealing, 194,
Recipes 200 Resources, 198,
Acknowledgments, 202,
About the Author, 204,
Index, 205,