Injection Mold Design Engineering 2E / Edition 2 available in Hardcover, eBook
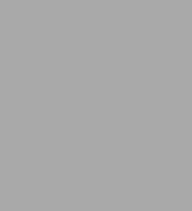
Injection Mold Design Engineering 2E / Edition 2
- ISBN-10:
- 1569905703
- ISBN-13:
- 9781569905708
- Pub. Date:
- 04/11/2016
- Publisher:
- Hanser Publications
- ISBN-10:
- 1569905703
- ISBN-13:
- 9781569905708
- Pub. Date:
- 04/11/2016
- Publisher:
- Hanser Publications
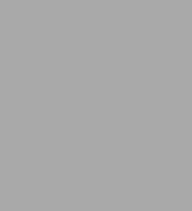
Injection Mold Design Engineering 2E / Edition 2
Buy New
$149.99Buy Used
$103.23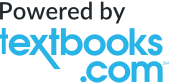
-
-
SHIP THIS ITEM
Temporarily Out of Stock Online
Please check back later for updated availability.
-
Overview
Product Details
ISBN-13: | 9781569905708 |
---|---|
Publisher: | Hanser Publications |
Publication date: | 04/11/2016 |
Edition description: | 2nd Revised ed. |
Pages: | 529 |
Product dimensions: | 6.90(w) x 9.60(h) x 1.10(d) |
Age Range: | 18 Years |
About the Author
Prior to his current appointment, he was an Applications Engineer at General Electric and Director of Research and Development at Synventive HotRunners. He is a licensed professional manufacturing engineer, and is a fellow of the American Society of Mechanical Engineers and the Society of Plastics Engineers. He is also the recipient of the ASME Kos Ishii-Toshiba Award for sustained, meritorious contributions to the field of design for manufacturing.
Table of Contents
Preface V
Nomenclature XV
1 Introduction 1
1.1 Overview of the Injection Molding Process 1
1.2 Mold Functions 3
1.3 Mold Structures 4
1.3.1 External View of Mold 4
1.3.2 View of Mold during Part Ejection 6
1.3.3 Mold Section and Function 7
1.4 Other Common Mold Types 9
1.4.1 Three Plate, Multi-Cavity Family Mold 9
1.4.2 Hot Runner, Multi-Gated, Single Cavity Mold 11
1.4.3 Comparison 12
1.5 The Mold Development Process 13
1.6 Chapter Review 15
2 Plastic Part Design 17
2.1 The Product Development Process 17
2.1.1 Product Definition 18
2.1.2 Product Design 18
2.1.3 Business and Production Development 19
2.1.4 Scale-Up and Launch 19
2.1.5 Role of Mold Design 19
2.2 Design Requirements 20
2.2.1 Application Engineering Information 20
2.2.2 Production Data 21
2.2.3 End Use Requirements 22
2.2.4 Product Design Methodology 24
2.2.5 Plastic Material Properties 26
2.3 Design for Injection Molding 28
2.3.1 Uniform Wall Thickness 28
2.3.2 Rib Design 29
2.3.3 Boss Design 29
2.3.4 Corner Design 30
2.3.5 Surface Finish and Textures 31
2.3.6 Draft 33
2.3.7 Undercuts 34
2.4 Chapter Review 35
3 Mold Cost Estimation 37
3.1 The Mold Quoting Process 37
3.2 Cost Drivers for Molded Parts 39
3.2.1 Effect of Production Quantity 40
3.2.2 Break-Even Analysis 41
3.3 Mold Cost Estimation 43
3.3.1 Cavity Cost Estimation 44
3.3.1.1 Cavity Set Cost 45
3.3.1.2 Cavity Materials Cost 45
3.3.1.3 Cavity Machining Cost 46
3.3.1.4 Cavity Discount Factor 51
3.3.1.5 Cavity Finishing Cost 51
3.3.2 Mold Base Cost Estimation 53
3.3.3 Mold Customization 55
3.4 Part Cost Estimation 60
3.4.1 Mold Cost per Part 60
3.4.2 MaterialCost per Part 61
3.4.3 Processing Cost per Part 62
3.4.4 Defect Cost per Part 65
3.5 Chapter Review 66
4 Mold Layout Design 67
4.1 Parting Plane Design 67
4.1.1 Determine Mold Opening Direction 67
4.1.2 Determine Parting Line 70
4.1.3 Parting Plane 71
4.1.4 Shut-Offs 73
4.2 Cavity and Core Insert Creation 74
4.2.1 Height Dimension 74
4.2.2 Length and Width Dimensions 75
4.2.3 Adjustments 76
4.3 Mold Base Selection 77
4.3.1 Cavity Layouts 77
4.3.2 Mold Base Sizing 79
4.3.3 Molding Machine Compatibility 81
4.3.4 Mold Base Suppliers 83
4.4 Mold Material Selection 84
4.4.1 Strength vs. Heat Transfer 84
4.4.2 Hardness vs. Machinability 85
4.4.3 Mold-Maker's Cost vs. Molder's Cost 86
4.4.4 Material Summary 88
4.5 Chapter Review 89
5 Cavity Filling Analysis and Design 91
5.1 Overview 91
5.2 Objectives in Cavity Filling 92
5.2.1 Complete Filling of Mold Cavities 92
5.2.2 Avoid Uneven Filling or Over-Packing 92
5.2.3 Control the Melt Flow 93
5.3 Viscous Flow 94
5.3.1 Shear Stress, Shear Rate, and Viscosity 94
5.3.2 Pressure Drop 95
5.3.3 Rheological Behavior 96
5.3.4 Newtonian Model 98
5.3.5 Power Law Model 99
5.4 Validation 102
5.5 Cavity Filling Analyses and Designs 104
5.5.1 Estimating the Processing Conditions 104
5.5.2 Estimating the Filling Pressure and Minimum Wall Thickness 107
5.5.3 Estimating Clamp Tonnage 109
5.5.4 Predicting Filling Patterns 112
5.5.5 Designing Flow Leaders 114
5.6 Chapter Review 117
6 Feed System Design 119
6.1 Overview 119
6.2 Objectives in Feed System Design 119
6.2.1 Conveying the Polymer Melt from Machine to Cavities 119
6.2.2 Impose Minimal Pressure Drop 120
6.2.3 Consume Minimal Material 121
6.2.4 Control Flow Rates 122
6.3 Feed System Types 123
6.3.1 Two-Plate Mold 123
6.3.2 Three-Plate Mold 125
6.3.3 Hot Runner Molds 130
6.4 Feed System Analysis 132
6.4.1 Determine Type of Feed System 133
6.4.2 Determine Feed System Layout 134
6.4.3 Estimate Pressure Drops 138
6.4.4 Calculate Runner Volume 140
6.4.5 Optimize Runner Diameters 141
6.4.6 Balance Flow Rates 145
6.4.7 Estimate Runner Cooling Times 148
6.4.8 Estimate Residence Time 149
6.5 Practical Issues 150
6.5.1 Runner Cross-Sections 150
6.5.2 Sucker Pins 154
6.5.3 Runner Shut-Offs 155
6.5.4 Standard Runner Sizes 157
6.5.5 Steel Safe Designs 157
6.6 Chapter Review 158
7 Gating Design 161
7.1 Objectives of Gating Design 161
7.1.1 Connecting the Runner to the Mold Cavity 161
7.1.2 Provide Automatic De-Gating 161
7.1.3 Provide Aesthetic De-Gating 162
7.1.4 Avoid Excessive Shear or Pressure Drop 162
7.1.5 Control Pack Times 163
7.2 Common Gate Designs 163
7.2.1 Sprue Gate 163
7.2.2 Pin-Point Gate 164
7.2.3 Edge Gate 165
7.2.4 Tab Gate 166
7.2.5 Fan Gate 167
7.2.6 Flash/Diaphragm Gate 168
7.2.7 Tunnel/Submarine Gate 169
7.2.8 Thermal Gate 172
7.2.9 Valve Gate 174
7.3 The Gating Design Process 175
7.3.1 Determine Type of Gate 175
7.3.2 Calculate Shear Rates 176
7.3.3 Calculate Pressure Drop 178
7.3.4 Calculate Gate Freeze Time 179
7.3.5 Adjust Dimensions 182
7.4 Chapter Review 182
8 Venting 185
8.1 Venting Design Objectives 185
8.1.1 Release Compressed Air 185
8.1.2 Contain Plastic Melt 185
8.1.3 Minimize Maintenance 186
8.2 Venting Analysis 186
8.2.1 Estimate Air Displacement and Rate 186
8.2.2 Identify Number and Location of Vents 186
8.2.3 Specify Vent Dimensions 189
8.3 Venting Designs 192
8.3.1 Vents on Parting Plane 192
8.3.2 Vents around Ejector Pins 194
8.3.3 Vents in Dead Pockets 196
8.4 Chapter Review 197
9 Cooling System Design 199
9.1 Objectives in Cooling System Design 199
9.1.1 Maximize Heat Transfer Rates 199
9.1.2 Maintain Uniform Wall Temperature 199
9.1.3 Minimize Mold Cost 200
9.1.4 Minimize Volume and Complexity 200
9.1.5 Minimize Stress and Corrosion 200
9.1.6 Facilitate Mold Usage 201
9.2 The Cooling System Design Process 201
9.2.1 Calculate the Required Cooling Time 201
9.2.2 Evaluate Required Heat Transfer Rate 206
9.2.3 Assess Coolant Flow Rate 208
9.2.4 Assess Cooling Line Diameter 209
9.2.5 Select Cooling Line Depth 211
9.2.6 Select Cooling Line Pitch 213
9.2.7 Cooling Line Routing 216
9.3 Cooling System Designs 219
9.3.1 Cooling Line Networks 219
9.3.2 Cooling Inserts 222
9.3.3 Conformal Cooling 222
9.3.4 Highly Conductive Inserts 223
9.3.5 Cooling of Slender Cores 224
9.3.5.1 Cooling Insert 225
9.3.5.2 Baffles 226
9.3.5.3 Bubblers 227
9.3.5.4 Heat Pipes 227
9.3.5.5 Conductive Pin 229
9.3.5.6 Interlocking Core with Air Channel 229
9.3.6 One-Sided Heat Flow 230
9.4 Chapter Review 232
10 Shrinkage and Warpage 233
10.1 The Shrinkage Analysis Process 235
10.1.1 Estimate Process Conditions 235
10.1.2 Model Compressibility Behavior 235
10.1.3 Assess Volumetric Shrinkage 237
10.1.4 Evaluate Isotropic Linear Shrinkage 241
10.1.5 Evaluate Anisotropic Shrinkage 242
10.1.6 Assess Shrinkage Range 244
10.1.7 Establishing Final Shrinkage Recommendations 245
10.2 Shrinkage Analysis and Validation 247
10.2.1 Numerical Simulation 247
10.2.2 "Steel Safe" Mold Design 249
10.2.3 Processing Dependence 249
10.2.4 Semi-Crystalline Plastics 251
10.2.5 Effect of Fillers 251
10.3 Warpage 252
10.3.1 Sources of Warpage 252
10.3.2 Warpage Avoidance Strategies 256
10.4 Chapter Review 257
11 Ejection System Design 259
11.1 Objectives in Ejection System Design 261
11.1.1 Allow Mold to Open 261
11.1.2 Transmit Ejection Forces to Moldings 262
11.1.3 Minimize Distortion of Moldings 262
11.1.4 Actuate Quickly and Reliably 262
11.1.5 Minimize Cooling Interference 263
11.1.6 Minimize Impact on Part Surfaces 264
11.1.7 Minimize Complexity and Cost 264
11.2 The Ejector System Design Process 265
11.2.1 Identify Mold Parting Surfaces 265
11.2.2 Estimate Ejection Forces 265
11.2.3 Determine Ejector Push Area and Perimeter 269
11.2.4 Specify Type, Number, and Size of Ejectors 271
11.2.5 Layout Ejectors 273
11.2.6 Detail Ejectors and Related Components 276
11.3 Ejector System Analyses and Designs 278
11.3.1 Ejector Pins 278
11.3.2 Ejector Blades 280
11.3.3 Ejector Sleeves 282
11.3.4 Stripper Plates 283
11.3.5 Elastic Deformation around Undercuts 285
11.3.6 Core Pulls 287
11.3.7 Slides 291
11.3.8 Early Ejector Return Systems 294
11.3.9 Advanced Ejection Systems 296
11.4 Chapter Review 296
12 Structural System Design 299
12.1 Objectives in Structural System Design 300
12.1.1 Minimize Stress 300
12.1.2 Minimize Mold Deflection 304
12.1.3 Minimize Mold Size 305
12.2 Analysis and Design of Plates 306
12.2.1 Plate Compression 306
12.2.2 Plate Bending 309
12.2.3 Support Pillars 312
12.2.4 Shear Stress in Side Walls 317
12.2.5 Interlocks 319
12.2.6 Stress Concentrations 321
12.3 Analysis and Design of Cores 325
12.3.1 Axial Compression 326
12.3.2 Compressive Hoop Stresses 327
12.3.3 Core Deflection 329
12.4 Fasteners 332
12.4.1 Fits 332
12.4.2 Socket Head Cap Screws 336
12.4.3 Dowels 338
12.5 Review 340
13 Mold Technologies 343
13.1 Introduction 343
13.2 Coinjection Molds 343
13.2.1 Coinjection Process 345
13.2.2 Coinjection Mold Design 346
13.2.3 Gas Assist/Water Assist Molding 347
13.3 Insert Molds 350
13.3.1 Low Pressure Compression Molding 350
13.3.2 Insert Mold with Wall Temperature Control 351
13.3.3 Lost Core Molding 353
13.4 Injection Blow Molds 355
13.4.1 Injection Blow Molding 355
13.4.2 Multilayer Injection Blow Molding 357
13.5 Multi-Shot Molds 358
13.5.1 Overmolding 359
13.5.2 Core-Back Molding 360
13.5.3 Multi-Station Mold 362
13.6 Feed Systems 364
13.6.1 Insulated Runner 364
13.6.2 Stack Molds 365
13.6.3 Branched Runners 368
13.6.4 Dynamic Melt Control 369
13.7 Mold Wall Temperature Control 372
13.7.1 Pulsed Cooling 372
13.7.2 Conduction Heating 373
13.7.3 Induction Heating 375
13.7.4 Managed Heat Transfer 377
13.8 In-Mold Labeling 378
13.8.1 Statically Charged Film 379
13.8.2 Indexed Film 380
13.9 Ejection 381
13.9.1 Split Cavity Molds 381
13.9.2 Collapsible Cores 383
13.9.3 Rotating Cores 384
13.9.4 Reverse Ejection 387
13.10 Review 388
Appendix 389
Appendix A Plastic Material Properties 390
Appendix B Mold Material Properties 394
B.1 Non-Ferrous Metals 394
B.2 Common Mold Steels 395
B.3 Other Mold Steels 396
B.4 Notes 397
Appendix C Properties of Coolants 398
Appendix D Statistical Labor Data 399
D.1 United States Labor Rates 399
D.2 International Labor Rates 399
D.3 Trends in International Manufacturing Costs 401
Appendix E Unit Conversions 402
E.1 Length Conversions 403
E.2 Mass/Force Conversions 403
E.3 Pressure Conversions 403
E.4 Flow Rate Conversions 404
E.5 Viscosity Conversions 404
E.6 Energy Conversions 404
Appendix F Advanced Derivations 405
Bibliography 409
Subject Index 413