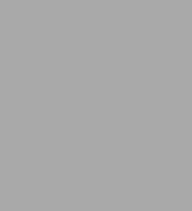
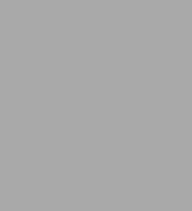
Paperback(Net)
-
PICK UP IN STORECheck Availability at Nearby Stores
Available within 2 business hours
Related collections and offers
Overview
Sailing
Whether you are shopping for a used fiberglass boat or prioritizing maintenance tasks on the one you already own, this book saves moneyand perhaps even disaster. With clear step-by-step drawings and instructions, Don Casey explains how to recognize problemsboth surface and hiddenand how to separate cosmetic flaws from serious faults.
Product Details
ISBN-13: | 9780071445450 |
---|---|
Publisher: | McGraw Hill LLC |
Publication date: | 07/27/2004 |
Edition description: | Net |
Pages: | 144 |
Product dimensions: | 7.40(w) x 9.10(h) x 0.30(d) |
About the Author
Read an Excerpt
INSPECTING THE AGING SAILBOAT
By DON CASEY
The McGraw-Hill Companies, Inc.
Copyright © 1997 International Marine, a division of The McGraw-Hill CompaniesAll rights reserved.
ISBN: 978-0-07-144545-0
Excerpt
CHAPTER 1
HULL
The hull is the most important component of any boat. It keeps the water out and the boat afloat, and it provides the foundation for all other components. A condemned mast, engine, or deck can be replaced, but a condemned hull dooms the boat. Always start your survey with the hull.
A fair number of wood hulls are still around, but the number gets smaller every year. While well-cared-for wood hulls are remarkably long lived, such care is sadly rare. An aging wood hull is infinitely more likely to have serious problems than one constructed of fiberglass. Effectively surveying a wood hull requires specialized techniques not covered here, but some guidance in probing wood for rot can be found in "Interior."
Metal is primarily a custom boat material in the United States, but a number of European production boats have been constructed of steel or aluminum. The main risk with metal hulls is corrosion. Determining their condition essentially requires examining every square inch for telltale signs—pitting and scaling, bubbled paint, or a powdery coating. A surveyor will bang suspicious spots vigorously with a hammer.
Fiberglass is the construction material of virtually all production sailboats built in the United States. If you own a sailboat or are looking to buy one less than 35 years old, there is an overwhelming likelihood that the boat's hull will be fiberglass. Unlike wood or metal, the troubles found in fiberglass hulls are rarely natural decomposition. More often they stem from poor construction techniques or impact damage.
Determining with a high degree of certainty the condition of a fiberglass hull requires little more than good observation skills and a basic understanding of the conditions you're looking for. Laboratory tests to determine the internal condition of the laminate are rarely employed, even by professional surveyors, because they rarely reveal conditions inconsistent with the surveyor's field observations.
Look, listen, and wonder. Sharp eyes, sensitive ears, and a deductive mind are the most important tools in the fiberglass-boat surveyor's kit.
FAIR AND TRUE?
Fair means smooth and regular—without humps or flat spots. True means accurately shaped—true to her designed lines. Both are good indicators of quality and may also reveal repairs.
HULL SIDES
Standing at the stern, position your eye near the hull, then slowly move sideways so you see more and more of the hull. Concentrate on the "horizon" of the hull, watching for it to jump or dip instead of move away smoothly. Glossy hulls are more revealing; wet the hull if it is dull, but don't confuse waves in the layer of water with irregularities in the hull. A flexible batten can help you position a flaw precisely.
Hardspots. Hardspots reveal themselves as bumps or ridges in the hull. Inside the boat you will generally find a bulkhead or other structural member at the hardspot. The hardspot is caused by the hull flexing over the rigid member. Most boats reveal hardspots to the observant eye, but if the bump is pronounced, the hinging may have broken the glass fibers. Suspect some weakening of the hull.
Flat spots. Because thin fiberglass depends upon curvature to make it stiff, designed flat areas of the hull will be thicker and/or stiffened to compensate. Flat spots in the curved parts of a hull indicate trouble. They occasionally occur because the manufacturer removed the hull from the mold too soon, but more often they indicate weakness, damage, or a poorly executed repair. Rigging tension can dimple a flimsy hull around the chainplate attachment points. A weak hull may permanently deflect if stored in a cradle or supported by screw stands for a long time. Any impact that flattens the hull has broken or delaminated the fiberglass. Amateur repairs often "bridge" a hole rather than matching the original contour of the hull. All of these require corrective measures.
Print-through. Often the weave of the underlying fabric is visible in the surface of the hull, especially if the gelcoat still has its gloss. Dark colors show print-through more. A light print-through is probably not serious, but anything more than that suggests poor layup technique. Hull construction begins with a layer of gelcoat sprayed into the polished mold, then one or two layers of chopped-strand mat (CSM) begins the laminate schedule. Mat is important because it is the most watertight fabric and it provides the best foundation for a strong gelcoat bond. That it also yields the smoothest surface is an ancillary benefit, so if you see significant print-through, the manufacturer failed to put sufficient mat between the woven fabric and the gelcoat. Premature gelcoat failure is a likely consequence.
LINES
Walk (or row) away from the hull, then circle it slowly, looking at the shape of the hull.
Symmetry. From directly forward and astern, the hull should appear symmetrical and the keel perpendicular to the deck. Sighting the hull through the gridwork of a plastic plotter simplifies this determination. Any detectable difference from one side to the other suggests major trouble.
Distortion. From either side, look for any change in the flow of the sheer. Overtight stays can permanently distort the hull, revealed by a break in the sheerline, usually at the mast station. Improper support during storage can also cause permanent hull distortion.
SCANTLINGS
Older fiberglass hulls are generally of consistent thickness, but hulls built in the last 15 years are likely to be thinner above the waterline than below. This lowers costs and may improve performance, but it makes a weaker hull. Current models may be more than 1 inch thick near the keel and less than ¼ that at the rail. Whether or not the loss in strength matters depends on how the boat will be used.
Without special equipment, you need a hole in the hull to determine its thickness. Any through-bolted hardware on the hull provides an opportunity to observe the hull thickness because you can extract a bolt. You can measure the thickness at through-hull fittings by dismantling just the hose connection. Hulls sometimes have extra thickness at through-hull locations, but you should be able to determine this by examining the inside of the hull around the through-hull. Except in extreme cases, determining the hull thickness has limited absolute value, but comparative hull thicknesses can be useful in evaluating boats from different manufacturers.
SIGNS OF STRESS OR TRAUMA
Fiberglass generally reveals stress problems with cracks in the gelcoat. The cracks can be very fine and hard to see; get close to the hull and lay your finger against the spot you are examining to ensure that your eyes focus properly. A dye penetrant such as Spot Check (available from auto-parts suppliers) can highlight hairline cracks.
Don't confuse stress cracks with surface crazing; crazing is a random pattern of cracks—something like the tapped shell of a boiled egg just before you peel it—that occurs over large areas of the boat. Stress cracks are localized and generally have an identifiable pattern to the discerning eye.
IMPACT DAMAGE
A collision serious enough to damage the hull usually leaves a scar, but sometimes the only visible record of the event is a pattern of concentric cracks in the gelcoat. Impact with a sharp object, like the corner of a dock, leaves a bull's-eye pattern. Impact with a flat object, like a piling or a seawall, tends to put the stressed area in parentheses. Tap the hull with a plastic mallet or a screwdriver handle in the area of the impact and listen for any dull-sounding areas, which indicate delamination. Examine the hull inside for signs that the impact fractured the glass.
PANTING
Panting occurs when poorly supported sections of the hull flex as the boat drives through the waves. This problem is also called oilcanning, taking its name from the domed bottom you push in and let spring back on a small oilcan. Panting usually occurs in relatively flat areas of the hull near the bow, but it may also occur in flat bilge areas and unreinforced quarters. The classic sign is a series of near-parallel cracks, sometimes crescent shaped, in the gelcoat. If you can move any portion of the hull by pushing on it, the hull lacks adequate stiffness. Left unchecked, panting can result in fatigue damage to the laminate and eventually a hinge crack all the way through the hull.
TRANSVERSE DAMAGE
An impact on one side of a boat often results in damage to the opposite side as the force is transferred by some rigid member or just by the box effect—push on one corner of a box and all corners are distorted. Because hulls are designed to resist outside assault, the damage to the nonimpacted side—where the stress is applied from inside the hull—is often greater than to the impacted side. When you find any evidence of impact damage, always check the opposite side of the boat for collateral damage.
WEEPING
Any spot on the hull that remains damp more than a few hours after the boat is hauled indicates water has penetrated the surface of the hull. Scrape away paint and you are likely to find a crack that requires repair. Weeping from an encapsulated keel can indicate a serious problem if the ballast is iron; water incursion causes the iron to rust and swell, distorting and even bursting the fiberglass. Examine the bottom of the keel and the rudder most carefully for signs of weeping.
REPAIRS
Done well, a repair is almost impossible to detect, but this is not a concern because a proper repair will be just as strong as the original laminate. Inferior repairs are generally easier to detect. We have already mentioned flat spots. Also look for variations in the color and texture of the hull surface. It is hard to match gelcoat exactly, and careful observation will usually reveal any patching. Gelcoat paste used in a repair can also develop a porous look compared to the billiard-ball smoothness of the original gelcoat. If the hull has been painted, look for a crescent-shaped ridge that will mark a less-than-perfectly-sanded patch.
Repairs are more visible inside the hull. Any signs of lifting around the edge of a patch suggests grinding—essential for a strong repair—was inadequate. The repair shouldn't be trusted. Where you find evidence of a repair, sound the hull in a regular pattern over the entire repair area to detect voids or delamination.
DELAMINATION
Delamination in fiberglass is the functional equivalent of rot in a wooden boat. Well-constructed solid-fiberglass hulls (meaning not cored) almost never delaminate unless they have suffered impact damage or unless water has penetrated the gelcoat (see the next section). This is because proper hull-construction technique—adding each layer before the previous one has cured—results in the resin linking chemically into a solid mass. Occasionally a manufacturer defeats this by leaving an uncompleted hull in the mold over a weekend; but most know—and do—better.
Introduce core into the formula and the likelihood of delamination increases dramatically. A core divides the hull into three distinct layers—the outer skin, the core, and the inner skin—with the bond between them strictly mechanical. Polyester resin adheres chemically to itself with amazing tenacity, but it has never been very good at adhering to other materials. At the slightest provocation it will release its grip on the core material, regardless of what it is.
PERCUSSION TESTING
Tapping a fiberglass hull is akin to spiking a wooden one. Use a plastic mallet or the handle of a screwdriver to give the hull a light rap. If the laminate is healthy, you will get a sharp report. If it is delaminated, the sound will be a dull thud. Your hull is sure to play more than two notes, but map all suspect returns; then check inside the hull to see if a bulkhead, tank, or bag of sail is responsible. If not, it is the laminate.
It is essential to do a thorough evaluation of a cored hull because core delamination is unfortunately common and robs the hull of much of its designed strength. Tap every 2 or 3 inches over the entire surface of the hull. Be especially suspicious of the area around through-hull fittings and near signs of skin damage or repair. Percussion testing can also reveal filler patches.
GELCOAT PROBLEMS
Most gelcoat problems are cosmetic, but a few suggest underlying structural defects.
CHALKING
Well-applied gelcoat will last a decade with little or no maintenance, perhaps twice that long if protected with a regular application of wax. Eventually the exposed surface erodes and the gelcoat loses its gloss. To determine whether the gloss can be restored, buff an inconspicuous area with rubbing compound (formulated for fiberglass). If the gloss returns before the gelcoat becomes transparent, you may get a few more years from the surface; otherwise, painting is the preferred way to restore the gloss.
SCRATCHES
If scratches don't penetrate the gelcoat, they can usually be buffed out with rubbing compound. Deep scratches are easily repaired with gelcoat putty.
CRAZING
Close examination of the gelcoat, especially on boats built in the '60s and '70s, may reveal a random egg-shell-like pattern of fine cracks which is usually caused by temperature expansion (and contraction) of the hull. It is prevalent in older boats because the gelcoat was thicker and thus less flexible. Correcting this condition requires filling the cracks with epoxy and painting the repaired surface.
STRESS CRACKING
Unlike crazing, stress cracks are usually localized and exhibit a discernible pattern. As previously mentioned, stress cracks can indicate impact damage or panting. They are a valuable clue for a number of other conditions detailed in this chapter. If you find cracks in the gelcoat, figure out why they are there before moving on.
VOIDS
The reluctance of glass fabric to take a sharp bend causes it to pull away from the gelcoat on inside corners during the layup process, creating voids. On a hull, this condition is generally confined to the stem, the corners where the hull sides intersect the transom, and the turn of the hull flange. Percussion testing reveals voids and may break them open. Voids are a cosmetic flaw and easily repaired with gelcoat putty.
BLISTERS
Blisters reveal themselves as bumps in the surface of fiberglass and are easily detected by simply examining the hull. A blister can be as small as a ladybug or as big as your hand.
GELCOAT BLISTERS
Blisters occur because free water-soluble chemicals inside the laminate exert an osmotic pull on water outside, and some water molecules find a way through the slightly permeable gelcoat. As more water is attracted into the enclosed space, internal pressure builds. The water molecules aren't squirted back out the way they came in because they combine with the attracting chemicals into a solution with a larger molecular structure. Instead, the pressure pushes the covering gelcoat into a dome—a blister.
Break a sample blister to assess the condition. Wear goggles because pressures can exceed 150 psi and the liquid that comes spraying out is acid. Scrub out the blister with water and a brush and examine the underlying laminate. If the laminate is perfect—the usual finding—the blister is primarily a cosmetic flaw, although taking steps to prevent water from reaching the laminate may be prudent.
LAMINATE BLISTERS
If the laminate is damaged, repairs will be more extensive, but this is still not a dangerous condition as long as the number of blisters is small. Use a knife point to find the depth of the damage. Laminate blisters most often occur between the initial layer(s) of mat and the first layer of woven roving—probably because the manufacturer was religious about getting the initial mat laid into the mold while the gelcoat was still chemically active, but was less exacting about the timing for completing the layup. Or it may be due to a failure to roll the roving sufficiently against the resin-stiffened mat to eliminate all voids. Whatever the reason, laminate blisters below the first layers of mat are no more dangerous than gelcoat blisters.
If additional layers of the laminate are involved in the blister, the area will have to be treated like any other delamination. How serious the problem is depends on the number and size of the laminate blisters.
POX
For pox, examine the bottom as soon as it comes out of the water. In the early stages blisters can shrink and even disappear altogether. If the bottom is covered with hundreds of blisters, the boat has pox. Boat pox is a much more serious condition than a handful of blisters scattered over the bottom of a 15- year-old hull. It is a systemic condition and will only worsen unless remedial action is taken.
To cure boat pox you must grind away all the gelcoat below the waterline. Just opening and filling the blisters won't do because a hull with pox is saturated throughout and won't dry out unless the gelcoat is removed. Once the hull is dry, which can take several months, the usual process is to apply a new barrier coat of epoxy. The cost to have this done professionally is between $300 and $400 per foot of boat length. Most of this is labor, so the cost if you do it yourself is much more modest, but it is a nasty job at best.
(Continues...)
Excerpted from INSPECTING THE AGING SAILBOAT by DON CASEY. Copyright © 1997 by International Marine, a division of The McGraw-Hill Companies. Excerpted by permission of The McGraw-Hill Companies, Inc..
All rights reserved. No part of this excerpt may be reproduced or reprinted without permission in writing from the publisher.
Excerpts are provided by Dial-A-Book Inc. solely for the personal use of visitors to this web site.