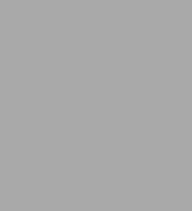
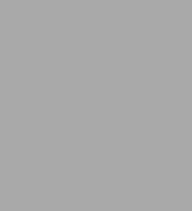
eBook
Available on Compatible NOOK devices, the free NOOK App and in My Digital Library.
Related collections and offers
Overview
Craft beautiful, sweet-smelling milk-based soaps safely and easily. In this fun and informative guide, Casey Makela shares her specialized techniques for producing lusciously creamy soaps. With straightforward instructions and thorough explanations, Makela teaches you how to fashion your own soaps from vegetable oils and tallow bases, giving dozens of suggestions for relaxing scents and specialty colors that will let your product shine. You’ll soon be creating enticingly unique soaps that will keep your glowing skin smelling and feeling good all day.
Product Details
ISBN-13: | 9781612122649 |
---|---|
Publisher: | Storey Publishing, LLC |
Publication date: | 01/09/1997 |
Sold by: | Hachette Digital, Inc. |
Format: | eBook |
Pages: | 112 |
File size: | 5 MB |
About the Author
Read an Excerpt
CHAPTER 1
A Glance Back
There is nothing in this world except the history you do not know.
— Harry S. Truman
Soapmaking is a unique marriage of science and art. As a science, soap is the chemical combination of fat (either vegetable or animal) and alkali; in home soap production, the alkali used most often is sodium hydroxide, known commonly as lye. The soapmaking process is called saponification, meaning "to convert a fat or oil into soap by the action of an alkali."
As an art, it inspires experimentation with colors, textures, scents, and shapes, offering an open invitation to be creative.
Cleansing agents are mentioned in the Bible in Job 9:30, Jeremiah 2:22, and Malachi 3:2. Malachi mentions "the lye of laundrymen." A more specific description of soap is found in the writings of a first-century naturalist-historian, Pliny the Elder, in 77 a.d. Pliny described various forms of hard and soft soaps renowned as rutilandi capilli, "making hair shine." These soaps were used by women to cleanse and enhance hair color.
GROWTH OF SOAP INDUSTRY
Ancient history reveals that soap in its early forms was regarded as a mere necessity and was in no way comparable to the giant cosmetic counterpart of today, in either development or commercial popularity. When advancements in the production of soap led to increased public demand and created new markets, the soap industry grew by leaps and bounds. With a heritage steeped in the lavish history of the famous bath-houses of Rome, soap became a valuable article of commerce in early Europe, despite efforts by the early Christian church to discourage bathing as an immodest practice.
In the thirteenth century the soap industry was introduced to France from Italy. At that time most soap was made by boiling goat tallow with beechwood ash (the source of the alkali or lye) and water. Inspired by what they had learned from Italian soapmakers, French soapmakers experimented further to improve soap quality and developed a method of making soap from olive oil instead of animal fats. Around the year 1500 they introduced their discoveries to England, where the industry grew rapidly.
EARLY FACTORY
A remarkably extensive soap factory was found by excavators among the ruins of Pompeii, an ancient city of Italy considered a "resort" area to the Romans.
Colonial American Soap
In the early American colonies, soapmaking was an individual household task as important as spinning, weaving, candlemaking, and other common domestic skills. Hardwood ashes were kept and put into a "leaching barrel," a large wooden barrel with a plugged hole near the base. A thin layer of stones was put in the bottom, and a layer of straw on top of the stones filled up the rest of the barrel. These barrels were kept near the house or barn, where they could catch water runoff from the roof on rainy days. Once the ashes in the leaching barrel were saturated, the plug was removed and the "lye-water" was allowed to drain out into a nonmetal container in the amount needed for a batch of soap. A common test of the lyewater's strength was to dip a feather in it: If the feather dissolved, the lye-water was strong enough to make a batch of soap. If not, the water was poured back into the leaching barrel. These homemade soaps were a soft type that would not be very desirable by today's standards — including a reputation for smelling bad — but they were effective enough for everyday cleaning.
In 1621, soap-ash was an important and lucrative export from the colonies to England, providing the colonies with a much-needed source of income. Factory demand in England for both soap-ash and animal fats was enormous. Fifty years later settlements in what is now Maine and New Hampshire gained great wealth from soap-ash and fat exports.
SOAP TRENDS
Shaving soap was one of the most popular soaps of the 1800s, due to the popularity of beardless faces.
Modernization of Process
The method of acquiring the necessary alkali through wood ashes was tedious, time consuming, and labor intensive. In 1791 Nicolas Leblanc discovered a process for manufacturing caustic soda inexpensively and on a large scale. This revolutionized the industry and eliminated the need to import soap from the colonies. Equally important was new research by the chemist M.E. Chevreul in the 1800s, which clarified the principal differences between fats and oils.
Chevreul's research deciphered the underlying principles of saponification. No discovery has contributed more to the basic, comprehensive understanding of soapmaking.
By the first half of the nineteenth century, both the process and extent of commercial soap production were modernized, and large-scale manufacturing operations developed. It was common for soap to be processed in huge kettles containing from 100,000 to a staggering 1 million pounds of liquid soap. These kettles were heated by open fires and the contents had to be stirred constantly, until the mixture was hand-ladled into large wooden molds, where the saponifying soap hardened until it was ready to be cut.
One of the early American establishments of the soap trade was founded in 1806 by William Colgate of New York. By 1850, New England was the principal center of soap manufacturing in the United States. With the introduction of fancy soaps — perfumed and colored — began soap's unending popularity and variety, leading to the multibillion-dollar soap industry of today.
Commercial soapmaking hardly resembles the simplicity of early production in either ingredients or manufacturing procedures. Most store-bought soaps are now laden with synthetic fillers and additives; and although labeled "pure," soaps are not necessarily wholesome.
WHALE SOAP
Whale oil was used for soapmaking after the process of hydrogenation was invented, which enabled the oil to be hardened to the correct consistency, as well as deodorized.
Use of Milk
Today cosmetic companies include milk in a variety of skin-care-related products. The specific origins of milk-based soaps are not clear, though milk has been used as an ingredient in cosmetics and therapeutic treatments in different cultures for thousands of years. The soothing and moisturizing qualities of milk have made it an increasingly popular ingredient in commercial soaps, especially over the last 30 years.
Because commercial soaps contain additives many of us would like to avoid, however, you may wish to recreate the fundamentals of soapmaking, earning for yourself, as your ancestors did, the deep satisfaction that comes from mastering this ancient art.
A PROFITABLE PURSUIT
In 1622 James I of England granted a monopoly to a soapmaker who was allowed to produce 3,000 tons of soap a year and had to pay the king $100,000 a year for the "privilege." At 4 ounces per bar of soap, that's 24 million bars of soap!
In 1853 a British tax of a penny and a half per pound of soap brought in an annual revenue of more than $5 million.
CHAPTER 2
The Fundamentals of Soapmaking
We learn through experience and no one teaches anyone anything. This is as true for the infant moving from kicking to crawling to walking as it is for the scientist with his equations. If the environment permits it, anyone can learn whatever he chooses to learn; and if the individual permits it, the environment will teach him everything it has to teach.
— Viola Spolin
Soapmaking is the chemical combination of fats and alkalis. The process of converting fat or oil into soap by the action of an alkalis is, as I have noted, called saponification. Disregarding all variables, saponification basically boils down to:
Fat + Lye = Soap
Understanding the variables is what allows you to experiment. There are endless varieties that you may wish to explore.
Before beginning there are a few safety practices you must know about. Then we'll take a look at the equipment you will need to make your first batch of soap, with an in-depth discussion of the lye, molds, water, and fats that are critical parts of your soapmaking project. Finally, we'll be ready to go on to our first recipe for basic soapmaking.
Learning successful soapmaking starts with developing excellent and uncompromising safety habits. The alkalis ingredient called for in the soap recipes in this book is sodium hydroxide, commonly known as lye. Sodium hydroxide is a powerful caustic agent that cannot be handled with bare hands, and its fumes must not be inhaled. Companies that manufacture the product warn on their labels that sodium hydroxide burns and is "harmful or fatal if swallowed." Until the fat/lye mixture fully saponifies into soap (approximately 48 hours after being poured into the mold), it will burn the skin.
Working with Lye
Never forget that lye is a powerful and dangerous chemical that must be handled with great care. Everyone who undertakes soapmaking assumes full responsibility for his or her own safety.
Please strictly observe these safe practices:
* Read and observe the precautionary statements on your lye container.
* Do not undertake soapmaking when tired or rushed, or while caring for young children. Making soap requires 100 percent undivided attention.
* Always wear safety glasses, keeping them on from start to finish. Don't risk exposing your precious eyesight to the perils of a lye burn.
* Always wear rubber gloves. If you do happen to get any lye on your skin, immediately run cold water on the area.
* Work in a well-ventilated room, near an open window, preferably. Do not inhale the fumes. If you live in a region where you must close up the house for the winter, wait for spring!
* Set aside utensils, pans, and any other soapmaking equipment for soapmaking use only, not to be used later for food preparation.
* Thoroughly clean every utensil, container, counter, and tabletop that was used for soapmaking immediately after the soap is poured into molds.
BASIC EQUIPMENT AND SUPPLIES
The tools needed to make basic soap are minimal and probably already available in your kitchen. Remember to dedicate your equipment for soapmaking only — do not use it for food preparation. You will need the following:
* 16-ounce (454 g) glass measuring cup
• 2 plastic or stainless-steel spoons
• 2-quart (1.9 l) stainless-steel saucepan
• 8-quart (7.5 l) stainless-steel pot
• Plastic spatula
• Plastic ladle
• Paring knife
• Scale
• Plastic wrap and newspaper
• Glass candy thermometer
• Molds (discussed below)
• Spray-on corn oil, mineral oil, or petroleum jelly
Your equipment should primarily be made of glass, stainless steel, or heavy-duty plastic. Never attempt to make soap in aluminum containers — you will ruin both your containers and your batch of soap. Strong plastic spoons are preferable to wood, because the lye will eat away at the wood fibers and eventually ruin the spoon.
You will use the glass measuring cup to measure the water. The spoons and spatula will be needed to stir ingredients and scrape the sides of the pans. You will mix the lye and water in the 2quart stainless-steel saucepan and melt the fat in the 8-quart stainless-steel saucepan.
Accurate temperature control is a vital part of the saponification process, so a good glass candy thermometer is a must.
Cover your entire working area with either plastic wrap or newspaper to protect work surfaces. Lye is corrosive and can damage areas on which it splashes.
Depending on your type of mold or molds, a good plastic ladle may be necessary to pour small amounts of the liquid soap.
Lye
The lye used in the soapmaking process is a chemical called sodium hydroxide. You can purchase sodium hydroxide in your grocery store in 12-ounce (340 g) containers. This is the exact amount needed for the recipes in this book, and it is convenient to have your sodium hydroxide pre-measured in a disposable container.
Be absolutely certain that the product you purchase contains only sodium hydroxide. You must read the label, since some brands contain additives that will interfere with the saponification process.
Molds
Before making your soap, you need to consider what your mold or molds will be and prepare them.
The recipes in this book make approximately 8 pounds (3.6 kg) of soap each. If you plan on your bars being 4 ounces (113 g) each, a typical size, you'll get 32 bars of soap per batch.
Molds can be obtained from many sources. Several companies (see suppliers list) specialize in making candy or candle molds that work well as soap molds, giving you a variety of shapes and sizes. Because soap is inclined to absorb color and even corrode as it saponifies, make sure the molds are clear; preferably they will be made of or lined with plastic. However, it may be a bit too expensive to start out buying enough molds for 8 pounds of soap.
An easier, less expensive mold is one made out of wood with dimensions of 20 inches by 14 inches and a depth of at least 2 inches (51 x 36 x 5 cm). If you can find a cardboard or Styrofoam box of this relative size, it will work well also.
Whether made of wood, cardboard, or Styrofoam, you will need to line your mold with plastic, snugging the plastic into the corners, making it as flat as possible on the bottom and sides, and taping it over the edges to hold it in place. Now lubricate the mold using spray-on corn oil, mineral oil, or petroleum jelly. The spray-on corn oil is the most convenient to use and works the best. Spray a light coating on the bottom and all sides, or use a napkin to rub on a light coating of mineral oil or petroleum jelly.
It is possible to make a grid form to insert into the square mold so the soap will be in forms or bars; this eliminates the need to hand-cut the large block of soap into bars. But you will find that hand-cutting your soap is a very satisfying task; it also results in smoother edges and a better product with much less preparation time.
Water
Using soft water in soapmaking is very important. The mineral deposits found in hard water work against achieving a soap that lathers well. How do you know if you have hard water? Most water, whether it's from a country well or a city waterworks, contains mineral deposits such as lime, iron, sulfur, and more. The amount of mineral deposits always varies with the geographical area but those deposits, no matter how small, will prevent the optimal outcome of your soapmaking. So it is preferable to use water from a water softener, or even rainwater.
If soft water is unavailable, add 1 ounce (28.4 g) of borax to the soap recipe. Borax is a naturally occurring mineral made up of sodium, boron, oxygen, and water. Also called desert salts, it is known to have been used for over 4,000 years. Among other things, it is a famous household cleaning agent. Because of its exceptional water-softening qualities, borax is an excellent soap ingredient that enhances foaming action.
Fats
There are two basic sources of fat for soapmaking: animal and vegetable.
Vegetable oils. Fine cosmetic soaps are often made with a combination of liquid vegetable oils and vegetable shortening. Vegetable shortening usually comes from soybeans. It is economical and readily available at grocery stores. A variety of vegetable oils can be used for soapmaking; each one brings with it its own special qualities. The best and easiest-to-find oils are canola, olive, soy, and corn. As you gain experience and proficiency in soapmaking, the variety of vegetable oils available will offer many avenues for experimentation.
Animal fats. Animal fats have been used in soapmaking since time immemorial. Both pig and beef fat are common, and most soapmakers combine 1 part pork fat with 2 parts beef fat. Before you can use animal fat in soapmaking, it must be rendered. Rendering is the process of melting fat and clarifying it, making it free of impurities. You can buy clean rendered lard from your grocer, but it will usually be all pork fat. Soap that is made from all pork fat will be softer and not as white, and it will not last as long as soap made from beef fat. Soap made from all beef fat will be very hard (almost too hard) and nearly white. So it is best when making soap with animal fats to use a combination of both beef and pork.
Do not try to recycle old or used fats such as bacon fat for soapmaking. Although used and even rancid fats will work to make soap, you will lose considerable quality since it is nearly impossible to remove all objectionable odors and get a nice clean color.
If you choose to render your own fat for soapmaking, the time needed for the project will vary according to the amount of fat you render and whether you are using ground fat (ask your butcher to do this for you) or chopped-up chunks. The fat will have to "cook" on low heat for 1 to 2 hours, and you cannot leave it unattended.
If you are rendering animal fat for the first time, don't overwhelm yourself by working with too large an amount. Start out by using the amount you will need for one batch of soap and render approximately 1 pound (454 g) of fat more than what you need (e.g., 7 pounds instead of 6), to allow for the weight of the discarded waste.
(Continues…)
Excerpted from "Milk-Based Soaps"
by .
Copyright © 1997 Storey Publishing, LLC.
Excerpted by permission of Storey Publishing.
All rights reserved. No part of this excerpt may be reproduced or reprinted without permission in writing from the publisher.
Excerpts are provided by Dial-A-Book Inc. solely for the personal use of visitors to this web site.
Table of Contents
Chapter 1: A Glance BackChapter 2: The Fundamentals of Soapmaking
Chapter 3: What Is Milk?
Chapter 4: Preparing to Put Milk into Soap
Chapter 5: The Standard Milk-Based Soap Method
Chapter 6: Specialty Recipes
Chapter 7: Recipes for Other Milk-Based Soap Method
Chapter 8: Package It with Appeal
Chapter 9: Making Soap, Making Money
Resource Information
IndeX