Multiphase Catalytic Reactors: Theory, Design, Manufacturing, and Applications / Edition 1 available in Hardcover
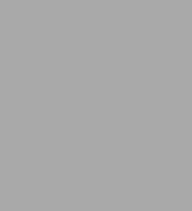
Multiphase Catalytic Reactors: Theory, Design, Manufacturing, and Applications / Edition 1
- ISBN-10:
- 1118115767
- ISBN-13:
- 9781118115763
- Pub. Date:
- 07/05/2016
- Publisher:
- Wiley
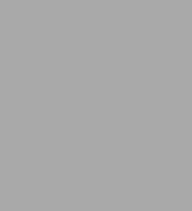
Multiphase Catalytic Reactors: Theory, Design, Manufacturing, and Applications / Edition 1
Hardcover
Buy New
$163.95Overview
- Provides a holistic approach to multiphase catalytic reactors from their modeling and design to their applications in industrial manufacturing of chemicals
- Covers theoretical aspects and examples of fixed-bed, fluidized-bed, trickle-bed, slurry, monolith and microchannel reactors
- Includes chapters covering experimental techniques and practical guidelines for lab-scale testing of multiphase reactors
- Includes mathematical content focused on design equations and empirical relationships characterizing different multiphase reactor types together with an assortment of computational tools
- Involves detailed coverage of multiphase reactor applications such as Fischer-Tropsch synthesis, fuel processing for fuel cells, hydrotreating of oil fractions and biofuels processing
Product Details
ISBN-13: | 9781118115763 |
---|---|
Publisher: | Wiley |
Publication date: | 07/05/2016 |
Pages: | 396 |
Product dimensions: | 8.70(w) x 11.30(h) x 1.00(d) |
About the Author
Ahmet Kerim Avci received BS, MS and PhD degrees in chemical engineering from Bogazici University in 1996, 1997 and 2003, respectively. He worked as an R&D manager in Procter & Gamble, Brussels-Belgium. In 2005, he joined chemical engineering department of Bogazici University, where he is currently a full professor. He is the leader of numerous research projects funded by governmental institutes and industry, and is the author of more than 25 papers in refereed SCI journals. He is the holder of Distinguished Young Scientist Fellowship (Turkish Academy of Sciences, 2009), Excellence in Research Award (Bogazici University Foundation, 2010), Eser Tumen Outstanding Achievement Award for Young Scientists (2011) and Professor Mustafa N. Parlar Research Incentive Award (2011).
Read an Excerpt
Table of Contents
List of Contributors, xPreface, xii
Part 1 Principles of catalytic reaction engineering
1 Catalytic reactor types and their industrial significance, 3Zeynep Ilsen Önsan and Ahmet Kerim Avci
1.1 Introduction, 3
1.2 Reactors with fixed bed of catalysts, 3
1.2.1 Packed-bed reactors, 3
1.2.2 Monolith reactors, 8
1.2.3 Radial flow reactors, 9
1.2.4 Trickle-bed reactors, 9
1.2.5 Short contact time reactors, 10
1.3 Reactors with moving bed of catalysts, 11
1.3.1 Fluidized-bed reactors, 11
1.3.2 Slurry reactors, 13
1.3.3 Moving-bed reactors, 14
1.4 Reactors without a catalyst bed, 14
1.5 Summary, 16
References, 16
2 Microkinetic analysis of heterogeneous catalytic systems, 17Zeynep Ilsen Önsan
2.1 Heterogeneous catalytic systems, 17
2.1.1 Chemical and physical characteristics of solid catalysts, 18
2.1.2 Activity, selectivity, and stability, 21
2.2 Intrinsic kinetics of heterogeneous reactions, 22
2.2.1 Kinetic models and mechanisms, 23
2.2.2 Analysis and correlation of rate data, 27
2.3 External (interphase) transport processes, 32
2.3.1 External mass transfer: Isothermal conditions, 33
2.3.2 External temperature effects, 35
2.3.3 Nonisothermal conditions: Multiple steady states, 36
2.3.4 External effectiveness factors, 38
2.4 Internal (intraparticle) transport processes, 39
2.4.1 Intraparticle mass and heat transfer, 39
2.4.2 Mass transfer with chemical reaction: Isothermal effectiveness, 41
2.4.3 Heat and mass transfer with chemical reaction, 45
2.4.4 Impact of internal transport limitations on kinetic studies, 47
2.5 Combination of external and internal transport effects, 48
2.5.1 Isothermal overall effectiveness, 48
2.5.2 Nonisothermal conditions, 49
2.6 Summary, 50
Nomenclature, 50
Greek letters, 51
References, 51
Part 2 Two-phase catalytic reactors
3 Fixed-bed gas–solid catalytic reactors, 55João P. Lopes and Alírio E. Rodrigues
3.1 Introduction and outline, 55
3.2 Modeling of fixed-bed reactors, 57
3.2.1 Description of transport–reaction phenomena, 57
3.2.2 Mathematical model, 59
3.2.3 Model reduction and selection, 61
3.3 Averaging over the catalyst particle, 61
3.3.1 Chemical regime, 64
3.3.2 Diffusional regime, 64
3.4 Dominant fluid–solid mass transfer, 66
3.4.1 Isothermal axial flow bed, 67
3.4.2 Non-isothermal non-adiabatic axial flow bed, 70
3.5 Dominant fluid–solid mass and heat transfer, 70
3.6 Negligible mass and thermal dispersion, 72
3.7 Conclusions, 73
Nomenclature, 74
Greek letters, 75
References, 75
4 Fluidized-bed catalytic reactors, 80John R. Grace
4.1 Introduction, 80
4.1.1 Advantages and disadvantages of fluidized-bed reactors, 80
4.1.2 Preconditions for successful fluidized-bed processes, 81
4.1.3 Industrial catalytic processes employing fluidized-bed reactors, 82
4.2 Key hydrodynamic features of gas-fluidized beds, 83
4.2.1 Minimum fluidization velocity, 83
4.2.2 Powder group and minimum bubbling velocity, 84
4.2.3 Flow regimes and transitions, 84
4.2.4 Bubbling fluidized beds, 84
4.2.5 Turbulent fluidization flow regime, 85
4.2.6 Fast fluidization and dense suspension upflow, 85
4.3 Key properties affecting reactor performance, 86
4.3.1 Particle mixing, 86
4.3.2 Gas mixing, 87
4.3.3 Heat transfer and temperature uniformity, 87
4.3.4 Mass transfer, 88
4.3.5 Entrainment, 88
4.3.6 Attrition, 89
4.3.7 Wear, 89
4.3.8 Agglomeration and fouling, 89
4.3.9 Electrostatics and other interparticle forces, 89
4.4 Reactor modeling, 89
4.4.1 Basis for reactor modeling, 89
4.4.2 Modeling of bubbling and slugging flow regimes, 90
4.4.3 Modeling of reactors operating in high-velocity flow regimes, 91
4.5 Scale-up, pilot testing, and practical issues, 91
4.5.1 Scale-up issues, 91
4.5.2 Laboratory and pilot testing, 91
4.5.3 Instrumentation, 92
4.5.4 Other practical issues, 92
4.6 Concluding remarks, 92
Nomenclature, 93
Greek letters, 93
References, 93
Part 3 Three-phase catalytic reactors
5 Three-phase fixed-bed reactors, 97Ion Iliuta and Faïçal Larachi
5.1 Introduction, 97
5.2 Hydrodynamic aspects of three-phase fixed-bed reactors, 98
5.2.1 General aspects: Flow regimes, liquid holdup, two-phase pressure drop, and wetting efficiency, 98
5.2.2 Standard two-fluid models for two-phase downflow and upflow in three-phase fixed-bed reactors, 100
5.2.3 Nonequilibrium thermomechanical models for two-phase flow in three-phase fixed-bed reactors, 102
5.3 Mass and heat transfer in three-phase fixed-bed reactors, 104
5.3.1 Gas–liquid mass transfer, 105
5.3.2 Liquid–solid mass transfer, 105
5.3.3 Heat transfer, 106
5.4 Scale-up and scale-down of trickle-bed reactors, 108
5.4.1 Scaling up of trickle-bed reactors, 108
5.4.2 Scaling down of trickle-bed reactors, 109
5.4.3 Salient conclusions, 110
5.5 Trickle-bed reactor/bioreactor modeling, 110
5.5.1 Catalytic hydrodesulfurization and bed clogging in hydrotreating trickle-bed reactors, 110
5.5.2 Biomass accumulation and clogging in trickle-bed bioreactors for phenol biodegradation, 115
5.5.3 Integrated aqueous-phase glycerol reforming and dimethyl ether synthesis into an allothermal dual-bed reactor, 121
Nomenclature, 126
Greek letters, 127
Subscripts, 128
Superscripts, 128
Abbreviations, 128
References, 128
6 Three-phase slurry reactors, 132Vivek V. Buwa, Shantanu Roy and Vivek V. Ranade
6.1 Introduction, 132
6.2 Reactor design, scale-up methodology, and reactor selection, 134
6.2.1 Practical aspects of reactor design and scale-up, 134
6.2.2 Transport effects at particle level, 139
6.3 Reactor models for design and scale-up, 143
6.3.1 Lower order models, 143
6.3.2 Tank-in-series/mixing cell models, 144
6.4 Estimation of transport and hydrodynamic parameters, 145
6.4.1 Estimation of transport parameters, 145
6.4.2 Estimation of hydrodynamic parameters, 146
6.5 Advanced computational fluid dynamics (CFD)-based models, 147
6.6 Summary and closing remarks, 149
Acknowledgments, 152
Nomenclature, 152
Greek letters, 153
Subscripts, 153
References, 153
7 Bioreactors, 156Pedro Fernandes and Joaquim M.S. Cabral
7.1 Introduction, 156
7.2 Basic concepts, configurations, and modes of operation, 156
7.2.1 Basic concepts, 156
7.2.2 Reactor configurations and modes of operation, 157
7.3 Mass balances and reactor equations, 159
7.3.1 Operation with enzymes, 159
7.3.2 Operation with living cells, 160
7.4 Immobilized enzymes and cells, 164
7.4.1 Mass transfer effects, 164
7.4.2 Deactivation effects, 166
7.5 Aeration, 166
7.6 Mixing, 166
7.7 Heat transfer, 167
7.8 Scale-up, 167
7.9 Bioreactors for animal cell cultures, 167
7.10 Monitoring and control of bioreactors, 168
Nomenclature, 168
Greek letters, 169
Subscripts, 169
References, 169
Part 4 Structured reactors
8 Monolith reactors, 173João P. Lopes and Alírio E. Rodrigues
8.1 Introduction, 173
8.1.1 Design concepts, 174
8.1.2 Applications, 178
8.2 Design of wall-coated monolith channels, 179
8.2.1 Flow in monolithic channels, 179
8.2.2 Mass transfer and wall reaction, 182
8.2.3 Reaction and diffusion in the catalytic washcoat, 190
8.2.4 Nonisothermal operation, 194
8.3 Mapping and evaluation of operating regimes, 197
8.3.1 Diversity in the operation of a monolith reactor, 197
8.3.2 Definition of operating regimes, 199
8.3.3 Operating diagrams for linear kinetics, 201
8.3.4 Influence of nonlinear reaction kinetics, 202
8.3.5 Performance evaluation, 203
8.4 Three-phase processes, 204
8.5 Conclusions, 207
Nomenclature, 207
Greek letters, 208
Superscripts, 208
Subscripts, 208
References, 209
9 Microreactors for catalytic reactions, 213Evgeny Rebrov and Sourav Chatterjee
9.1 Introduction, 213
9.2 Single-phase catalytic microreactors, 213
9.2.1 Residence time distribution, 213
9.2.2 Effect of flow maldistribution, 214
9.2.3 Mass transfer, 215
9.2.4 Heat transfer, 215
9.3 Multiphase microreactors, 216
9.3.1 Microstructured packed beds, 216
9.3.2 Microchannel reactors, 218
9.4 Conclusions and outlook, 225
Nomenclature, 226
Greek letters, 227
Subscripts, 227
References, 228
Part 5 Essential tools of reactor modeling and design
10 Experimental methods for the determination of parameters, 233Rebecca R. Fushimi, John T. Gleaves and Gregory S. Yablonsky
10.1 Introduction, 233
10.2 Consideration of kinetic objectives, 234
10.3 Criteria for collecting kinetic data, 234
10.4 Experimental methods, 234
10.4.1 Steady-state flow experiments, 235
10.4.2 Transient flow experiments, 237
10.4.3 Surface science experiments, 238
10.5 Microkinetic approach to kinetic analysis, 241
10.6 TAP approach to kinetic analysis, 241
10.6.1 TAP experiment design, 242
10.6.2 TAP experimental results, 244
10.7 Conclusions, 248
References, 249
11 Numerical solution techniques, 253Ahmet Kerim Avci and Seda Keskin
11.1 Techniques for the numerical solution of ordinary differential equations, 253
11.1.1 Explicit techniques, 253
11.1.2 Implicit techniques, 254
11.2 Techniques for the numerical solution of partial differential equations, 255
11.3 Computational fluid dynamics techniques, 256
11.3.1 Methodology of computational fluid dynamics, 256
11.3.2 Finite element method, 256
11.3.3 Finite volume method, 258
11.4 Case studies, 259
11.4.1 Indirect partial oxidation of methane in a catalytic tubular reactor, 259
11.4.2 Hydrocarbon steam reforming in spatially segregated microchannel reactors, 261
11.5 Summary, 265
Nomenclature, 266
Greek letters, 267
Subscripts/superscripts, 267
References, 267
Part 6 Industrial applications of multiphase reactors
12 Reactor approaches for Fischer–Tropsch synthesis, 271Gary Jacobs and Burtron H. Davis
12.1 Introduction, 271
12.2 Reactors to 1950, 272
12.3 1950–1985 period, 274
12.4 1985 to present, 276
12.4.1 Fixed-bed reactors, 276
12.4.2 Fluidized-bed reactors, 280
12.4.3 Slurry bubble column reactors, 281
12.4.4 Structured packings, 286
12.4.5 Operation at supercritical conditions (SCF), 288
12.5 The future?, 288
References, 291
13 Hydrotreating of oil fractions, 295Jorge Ancheyta, Anton Alvarez-Majmutov and Carolina Leyva
13.1 Introduction, 295
13.2 The HDT process, 296
13.2.1 Overview, 296
13.2.2 Role in petroleum refining, 297
13.2.3 World outlook and the situation of Mexico, 298
13.3 Fundamentals of HDT, 300
13.3.1 Chemistry, 300
13.3.2 Reaction kinetics, 303
13.3.3 Thermodynamics, 305
13.3.4 Catalysts, 306
13.4 Process aspects of HDT, 307
13.4.1 Process variables, 307
13.4.2 Reactors for hydroprocessing, 310
13.4.3 Catalyst activation in commercial hydrotreaters, 316
13.5 Reactor modeling and simulation, 317
13.5.1 Process description, 317
13.5.2 Summary of experiments, 317
13.5.3 Modeling approach, 319
13.5.4 Simulation of the bench-scale unit, 320
13.5.5 Scale-up of bench-unit data, 323
13.5.6 Simulation of the commercial unit, 324
Nomenclature, 326
Greek letters, 327
Subscripts, 327
Non-SI units, 327
References, 327
14 Catalytic reactors for fuel processing, 330Gunther Kolb
14.1 Introduction—The basic reactions of fuel processing, 330
14.2 Theoretical aspects, advantages, and drawbacks of fixed beds versus monoliths, microreactors, and membrane reactors, 331
14.3 Reactor design and fabrication, 332
14.3.1 Fixed-bed reactors, 332
14.3.2 Monolithic reactors, 332
14.3.3 Microreactors, 332
14.3.4 Membrane reactors, 333
14.4 Reformers, 333
14.4.1 Fixed-bed reformers, 336
14.4.2 Monolithic reformers, 337
14.4.3 Plate heat exchangers and microstructured reformers, 342
14.4.4 Membrane reformers, 344
14.5 Water-gas shift reactors, 348
14.5.1 Monolithic reactors, 348
14.5.2 Plate heat exchangers and microstructured water-gas shift reactors, 348
14.5.3 Water-gas shift in membrane reactors, 350
14.6 Carbon monoxide fine cleanup: Preferential oxidation and selective methanation, 350
14.6.1 Fixed-bed reactors, 352
14.6.2 Monolithic reactors, 352
14.6.3 Plate heat exchangers and microstructured reactors, 353
14.7 Examples of complete fuel processors, 355
14.7.1 Monolithic fuel processors, 355
14.7.2 Plate heat exchanger fuel processors on the meso- and microscale, 357
Nomenclature, 359
References, 359
15 Modeling of the catalytic deoxygenation of fatty acids in a packed bed reactor, 365Teuvo Kilpiö, Päivi Mäki-Arvela, Tapio Salmi and Dmitry Yu. Murzin
15.1 Introduction, 365
15.2 Experimental data for stearic acid deoxygenation, 366
15.3 Assumptions, 366
<>15.4 Model equations, 36715.5 Evaluation of the adsorption parameters, 368
15.6 Particle diffusion study, 369
15.7 Parameter sensitivity studies, 369
15.8 Parameter identification studies, 370
15.9 Studies concerning the deviation from ideal plug flow conditions, 371
15.10 Parameter estimation results, 372
15.11 Scale-up considerations, 372
15.12 Conclusions, 375
Acknowledgments, 375
Nomenclature, 375
Greek letters, 375
References, 376
Index, 377