Operations Engineering and Management: Concepts, Analytics and Principles for Improvement
Discover how to apply engineering thinking and data analytics to business operations
This comprehensive textbook shows readers how to develop their engineering thinking and analytics to support making strategic and tactical decisions in managing and control of operations systems and supply chains. The book is created in a modular fashion so that sections and chapters can stand alone and be used within operations courses across the spectrum.
Operations Engineering and Management: Concepts, Analytics and Principles for Improvement is based on the author’s successful classes in both business and engineering. The book presents concepts and principles of operations management, with a strong emphasis on analytics and a sharp focus on improving operations. You will explore both the engineering approach to operations (e.g., analytics and engineering thinking) and the classic management approach.
• Focuses on teaching and developing strong problem-solving analytics skills
• Each section is designed to stand alone and can be used in a wide variety of courses
• Written by an operations management and engineering expert
1136470721
This comprehensive textbook shows readers how to develop their engineering thinking and analytics to support making strategic and tactical decisions in managing and control of operations systems and supply chains. The book is created in a modular fashion so that sections and chapters can stand alone and be used within operations courses across the spectrum.
Operations Engineering and Management: Concepts, Analytics and Principles for Improvement is based on the author’s successful classes in both business and engineering. The book presents concepts and principles of operations management, with a strong emphasis on analytics and a sharp focus on improving operations. You will explore both the engineering approach to operations (e.g., analytics and engineering thinking) and the classic management approach.
• Focuses on teaching and developing strong problem-solving analytics skills
• Each section is designed to stand alone and can be used in a wide variety of courses
• Written by an operations management and engineering expert
Operations Engineering and Management: Concepts, Analytics and Principles for Improvement
Discover how to apply engineering thinking and data analytics to business operations
This comprehensive textbook shows readers how to develop their engineering thinking and analytics to support making strategic and tactical decisions in managing and control of operations systems and supply chains. The book is created in a modular fashion so that sections and chapters can stand alone and be used within operations courses across the spectrum.
Operations Engineering and Management: Concepts, Analytics and Principles for Improvement is based on the author’s successful classes in both business and engineering. The book presents concepts and principles of operations management, with a strong emphasis on analytics and a sharp focus on improving operations. You will explore both the engineering approach to operations (e.g., analytics and engineering thinking) and the classic management approach.
• Focuses on teaching and developing strong problem-solving analytics skills
• Each section is designed to stand alone and can be used in a wide variety of courses
• Written by an operations management and engineering expert
This comprehensive textbook shows readers how to develop their engineering thinking and analytics to support making strategic and tactical decisions in managing and control of operations systems and supply chains. The book is created in a modular fashion so that sections and chapters can stand alone and be used within operations courses across the spectrum.
Operations Engineering and Management: Concepts, Analytics and Principles for Improvement is based on the author’s successful classes in both business and engineering. The book presents concepts and principles of operations management, with a strong emphasis on analytics and a sharp focus on improving operations. You will explore both the engineering approach to operations (e.g., analytics and engineering thinking) and the classic management approach.
• Focuses on teaching and developing strong problem-solving analytics skills
• Each section is designed to stand alone and can be used in a wide variety of courses
• Written by an operations management and engineering expert
112.5
In Stock
5
1
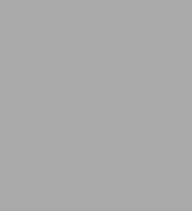
Operations Engineering and Management: Concepts, Analytics and Principles for Improvement
704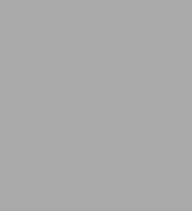
Operations Engineering and Management: Concepts, Analytics and Principles for Improvement
704
112.5
In Stock
Product Details
ISBN-13: | 9781260461848 |
---|---|
Publisher: | McGraw Hill LLC |
Publication date: | 10/16/2020 |
Sold by: | Barnes & Noble |
Format: | eBook |
Pages: | 704 |
File size: | 52 MB |
Note: | This product may take a few minutes to download. |
About the Author
From the B&N Reads Blog