Pollution Prevention: Methodology, Technologies and Practices / Edition 1 available in Hardcover
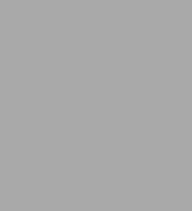
Pollution Prevention: Methodology, Technologies and Practices / Edition 1
- ISBN-10:
- 081690782X
- ISBN-13:
- 9780816907823
- Pub. Date:
- 11/15/1998
- Publisher:
- Wiley
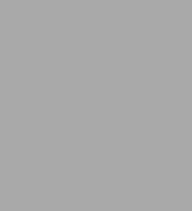
Pollution Prevention: Methodology, Technologies and Practices / Edition 1
Hardcover
Buy New
$319.95Overview
Product Details
ISBN-13: | 9780816907823 |
---|---|
Publisher: | Wiley |
Publication date: | 11/15/1998 |
Series: | AICHE Originals Series |
Pages: | 214 |
Product dimensions: | 8.80(w) x 11.30(h) x 0.75(d) |
About the Author
A 28-year veteran with DuPont, Mulholland has held positions in research, process development, and chemical engineering consulting. He holds a B.S. from Lehigh University and Ph.D. from the University of Kansas, both in chemical engineering, and is a registered professional engineer in Delaware.
Dyer has been with DuPont for 14 years, working in project and process engineering, and process development, as well as consulting on VOC emission control technologies, economic evaluations, and aqueous electrolyte thermodynamic modeling. A registered professional engineer in Delaware, Dyer received his B.S. in chemical engineering from Drexel University, and an M.S. in civil engineering at the University of Delaware. He is currently pursuing a Ph.D. in environmental soil geochemistry at Delaware.
Table of Contents
Dedication.Foreword.
Preface.
Acknowledgments.
Epigraph.
Chapter 1. Why Pollution Prevention?
1.1 Introduction
1.2 Waste As Pollution.
1.3 How is Pollution Prevention Defined?
1.4 Drivers for Pollution Prevention.
1.5 Pollution-Prevention Wisdom.
1.5.1 Waste Stream Analysis.
1.5.2 Process Analysis.
1.6 Scope of this Book.
Literature Cited.
Chapter 2. The Path to Pollution Prevention.
2.1 Introduction.
2.2 The Recipe for Success.
2.3 Program Elements.
2.3.1 Chartering Phase.
2.3.2 Assessment Phase.
2.3.3 Implementation Phase.
2.4 The Incentive for Pollution Prevention.
2.4.1 New End-of-Pipe Treatment.
2.4.2 Raw-Materials Cost.
2.4.3 Cost of Manufacture.
2.5 Pollution-Prevention Engineering Technologies and Practices.
2.6 Engineering Evaluation of the Preferred Options.
2.7 Waste Stream and Process Analyses.
2.8 Case Studies.
2.8.1 Program Elements: U.S. EPA and DuPont Chambers Works Waste-Minimization Project.
2.8.2 Incentive for Pollution Prevention—Gas-Flow-Rate Reduction.
2.8.3 Waste Stream Analysis: Nonaqueous Cleaning.
2.8.4 Process Analysis: Replace Solvent with a Process Intermediate, Product, or Feed.
Literature Cited.
Chapter 3. Pollution Prevention Program Development.
3.1 Introduction.
3.2 Regulations.
3.3 A Successful Pollution-Prevention Program.
3.4 Program Elements.
3.5 Chartering Phase.
3.5.1 Business Leadership Decision to Start.
3.5.2 Establishing the Program.
3.5.3 Selecting the Waste Streams.
3.5.4 Creating a Core Assessment Team.
3.6 Assessment Phase.
3.6.1 Collect Data.
3.6.2 Set Goals.
3.6.3 Define the Problem.
3.6.4 Show Stoppers.
3.6.5 Generate Options.
3.6.6 Screening the Options.
3.6.7 Evaluate the Screened Options.
3.7 Implementation Phase.
3.7.1 Select Options for Implementation.
3.7.2 Create Preliminary Implementation Plan.
3.7.3 Secure Approval for Implementation and Begin Implementation Projects.
3.7.4 Keep People Involved.
3.8 Resources.
3.9 When Should You Do Pollution Prevention?
3.9.1 Pollution Prevention during Research and Development.
3.9.2 Pollution Prevention during Process and Design Engineering.
3.9.3 Pollution Prevention during Process Operation.
3.10 Case Studies.
3.10.1 R&D Phase.
3.10.2 Process and Design Engineering Phase.
3.10.3 Existing Process Operation.
Literature Cited.
Chapter 4. Economics of Pollution Prevention.
4.1 Introduction.
4.2 End-of-Pipe Treatment Cost as the Incentive for Pollution Prevention.
4.3 Economic Criteria for Technology Comparisons.
4.3.1 Net Present Value.
4.3.2 Investment.
4.4 End-of-Pipe VOC and HVOC Treatment Technology Selection.
4.4.1 Cost Associated with Permit Applications.
4.4.2 Investment, Cash Operating Cost, and Net Present Cost.
4.5 Particulate Control Technologies.
4.5.1 Investment, Cost, and Economics.
4.5.2 technology Description.
4.5.3 Technology Selection.
4.6 Biological Wastewater Treatment Technologies.
4.6.1 Applicable technologies.
4.6.2 Incentive for Source Reduction for New Facilities.
4.6.3 Investment and Costs for Aerobic Deep-Tank Activated-Sludge Treatment Facilities.
4.7 Nonbiological Wastewater Treatment technologies.
4.7.1 Incentive for Pollution Prevention.
4.7.2 Nonbiological End-of-Pipe Technology Selection Map.
4.7.3 Investment, Cost, and Economics for Individual Technologies.
4.8 Solid-Waste Treatment Costs.
4.9 Examples.
4.9.1 High-Flow, VOC-Laden Air Stream.
4.9.2 Moderate-Flow, HVOC-Laden Air Stream.
4.9.3 Waste-Gas Stream with VOCs and particulates.
4.9.4 New Biotreatment Facility for an Existing Manufacturing Site.
4.10 Engineering Evaluations and Pollution Prevention.
4.10.1 What is Engineering Evaluation?
4.10.2 How Does It Work?
4.10.3 Where Is It Valuable.
4.11 The 10-Step Method.
4.11.1Define Problem and Set Goals (Step 1 and 2).
4.11.2 Identify the Alternatives (Step 3).
4.11.3 Define the Alternatives (Steps 4 and 5).
4.11.4 Evaluate the Alternatives (Steps 6 through 10).
4.12 Shortcut NPV Method.
4.12.1Data Requirements.
4.12.2 Calculating NPV.
4.12.3 Basis of the Shortcut Method.
4.12.4 Adjustments to the NPV Estimations Dues to Project Timing.
4.12.5 Comments on NPV Method.
4.12.6 An Example.
4.13 Waste-Management Economics: A Balanced Approach.
4.13.1 The Path to Better Solutions.
4.13.2 Incremental Costs of Waste Treatment.
4.13.3 How Should You Use These Incremental Costs?
4.13.4 Characteristics of a Balanced Approach.
Literature Cited.
Chapter 5. Case Study.
5.1 Introduction.
5.2 Background of Case Study.
5.3 Chartering Phase.
5.3.1 Incentive Based On End-of-Pipe Treatment.
5.3.2 Lost-Product Value Incentive for Pollution Prevention.
5.4 Assessment Phase.
5.4.1 Collect Data.
5.4.2 Set Goals.
5.4.3 Define the Problem.
5.4.4 Generate Ideas.
5.4.5 Screen Ideas.
5.4.6 Evaluate the Screened Ideas.
5.5 Implementation Phase.
5.6 Results.
Literature Cited.
Chapter 6. Pollution-Prevention Technologies and Practices.
6.1 Introduction.
6.2 Engineering Technologies, Operating Practices, and Unit Operations.
6.3 Dyelate Process Case Study.
6.3.1 Condensation.
6.3.2 Ring Closure.
6.3.3 Extraction.
6.3.4 Acidification and Halogenation.
6.3.5 Filtration and Drying.
6.3.6 Observations and Potential Process Improvement Options.
Literature Cited.
Chapter 7. Pollution Prevention In Batch Operations.
7.1 Introduction.
7.2 Nature and Sources of Emissions.
7.3 Pollution-Prevention Strategies.
7.3.1 Reactor Charging.
7.3.2 Reactor Operation.
7.3.3 Reactor Discharging.
7.3.4 Reactor Cleaning.
7.4 Modeling Batch Processes.
7.5 Batch vs. Continuous Operation.
7.6 Case Studies.
7.6.1 Replace an Organic Solvent with an Aqueous Solvent for Cleaning.
7.6.2 Methylene Chloride Emissions Reduction.
7.6.3 Conversion from Batch to Continuous Operation.
Literature Cited.
Chapter 8. Equipment and Parts Cleaning.
8.1 Introduction.
8.2 Nature of Emission Sources.
8.3 The Pollution-Prevention Continuum.
8.3.1 More Than 95% Pollution Prevention.
8.3.2 More Than 90% Pollution Prevention.
8.3.3 More Than 75% Pollution Prevention.
8.3.4 More Than 50% Pollution Prevention.
8.3.5 More Than and Less Than 10% Pollution Prevention.
8.3.6 Employee Awareness.
8.4 Cleaning Research.
8.5 Case Studies.
8.5.1 Minimize the Need for Cleaning.
8.5.2 Procedural Changes Relaxed Product Specifications.
8.5.3 High-Pressure Washing.
8.5.4 Waste Solvent Used For Flushing Equipment.
Literature Cited.
Chapter 9. High-Value Waste.
9.1 Introduction.
9.2 Regulations.
9.3 Conversion to a High-Value Waste.
9.3.1 Process and Waste-Stream Constituents.
9.3.2 Modify the Waste-Stream.
9.4 The Waste-Value Continuum.
9.4.1 Eliminate From the Process.
9.4.2 Reuse in the Process.
9.4.3 Convert to Feed.
9.4.4 Convert to Product.
9.4.5 End-of-Pipe Treatment.
9.5 Case Histories.
9.5.1 Organic Solvents Eliminated from the Process.
9.5.2 Acid Scavengers Eliminated from the Process.
9.5.3 Reusing Small Quantities of Solvents in a Process.
9.5.4 Wash-Solvent Reuse in Paint Formulation.
9.5.5 Vinyl Acetate Recovery and Reuse.
9.5.6 Reuse Sample Waste In the Process.
9.5.7 Reuse, Waste Elimination and Conversion to a Feed Material for a Herbicide Process.
9.5.8 Waste Segregation and Conversion to Products in Dairy Production.
9.5.9 Reintroduction of Waste Solids into a Polymer Process.
9.5.10 Nonwoven Waste Fabric Turned into a High-Value Product.
Literature Cited.
Chapter 10. Reactor Design and Operation.
10.1 Introduction.
10.2 Pollution-Prevention Strategies.
10.2.1 Consider the Impact of Solvent Selection.
10.2.2 Improve the Quality of Raw Materials.
10.2.3 Redesign the Reactor.
10.2.4 For Equilibrium Reactions, Recycle Byproducts.
10.2.5 For Sequential Reactions, Remove Product as it Forms.
10.2.6 Match the Mixing to the Reaction.
10.2.7 Improve the Way Reactants Are Added to the Reactor.
10.2.8 Modify Reactor Cooling or Heating.
10.2.9 Consider More Forgiving Regions of Operation.
10.2.10 Add, Change, or Optimize the Catalyst.
10.2.11 Optimize Reactant Feed Ratios and Addition Sequence.
10.2.12 Know, Analyze, and Control Critical Parameters.
10.2.13 Routinely Calibrate Instrumentation.
10.2.14 Other Strategies.
Literature Cited.
Chapter 11. Use of Water as a Solvent and Heat Transfer Fluid.
11.1 Introduction.
11.2 The Incentive for Source Reduction of Water Use.
11.3 Waste Reuse.
11.4 The Pollution-Prevention Continuum.
11.5 Pollution-Prevention Strategies.
11.6 Water Pinch Analysis.
11.7 Case Histories: Water as a Solvent.
11.7.1 Water Reuse as a Solvent.
11.7.2 pH Control.
11.7.3 Water Scrubbing.
11.7.4 Nonaqueous Cleaning.
11.8 Case Histories: Water as a Heat-Transfer Fluid.
11.8.1 Noncontact Cooling.
11.8.2 Water Monitoring.
11.8.3 Water Reuse for Energy.
Literature Cited.
Chapter 12. Organic Solvents.
12.1 Introduction.
12.2 Cost as a Driver for Pollution Prevention.
12.3 Regulations.
12.4 The Pollution-Prevention Continuum.
12.5 Source Reduction of Solvents.
12.6 Solvent Selection.
12.6.1. Step 1: Identify Important Chemical and Physical Solvent Properties.
12.6.2 Step 2: Identify Constraints on Important Solvent Properties.
12.6.3 Step 3: Compile Data for all Properties and Rank Solvents Satisfying the Target Constraints.
12.6.4 Step 4: Evaluate the Top Solvent Candidates Using Simulation.
12.7 Solvent-Selection Databases.
12.8 Case Histories.
12.8.1 Solventless Process.
12.8.2 Replace Replace Solvent with a Process Intermediate, Product, or Feed.
12.8.3 Water as a Solvent.
12.8.4 Improve Solvent Recovery.
12.8.5 Implement Solvent Recovery.
12.8.6 Process and Equipment Improvements.
12.8.7 Organic Solvent Selection.
Literature Cited.
Chapter 13. pH Control as a Pollution-Prevention Tool.
13.1 Introduction.
13.2 Pollution-Prevention Strategies.
13.2.1 Understand Whether Your Plant Adds Acid or Base to Control pH.
13.2.2 Avoid Excessive Carbon Dioxide Scrubbing in Caustic Scrubbers.
13.2.3 Know the pKa and pKb of Weak Organic Acids and Bases in Your Process and Their Impact on Waste Emissions.
13.3 Metals Solubility and pH.
13.3.1 Hydrolysis of Metal Cations.
13.3.2 Methodology of Dyer et al. Study.
13.3.3 The OLI Software System.
13.3.4 Overall Metal Solubility Diagrams.
13.3.5 The Important Role of Source Reduction and Pretreatment.
13.4 Case Histories.
13.4.1 Plugging of Feed Preheater and Column with Tars.
13.4.2 Tar Formation Due to Acidity in an Incoming Raw Material.
13.4.3 Metals Emissions in Wastewater Effluent.
13.4.4 Copper Emissions from Reaction Step.
Literature Cited.
Chapter 14. Pollution Prevention in Vacuum Processes.
14.1 Introduction.
14.2 Background.
14.3 Nature or Emission Sources.
14.4 Regulatory Outlook.
14.5 How Do Emissions Originate?
14.5.1 Entrainment.
14.5.2 Temperature of Operation.
14.5.3 Inert Level.
14.6 The Pollution-Prevention Continuum.
14.7 Source Reduction of Vacuum System Emissions.
14.7.1 Entrainment.
14.7.2 Temperature of Operation.
14.7.3 Inerts Level.
14.7.4 Vacuum Device.
14.8 Case Histories and Economics.
14.8.1 Case History #1: Degassing at High Vacuum During Polymer Production.
14.8.2 Case History #2: Vacuum Distillation.
Literature Cited.
Chapter 15. Ventilation of Manufacturing.
15.1 Introduction.
15.2 The Bottom Line.
15.3 Nature and Sources of Emissions.
15.4 Regulatory Outlook.
15.5 The Pollution-Prevention Continuum.
15.5.1 Process Modifications to Eliminate the Contaminants.
15.5.2 Minimize the Volume of Contaminated Air.
15.5.3 Recirculation of Ventilation Air.
15.5.4 Dilution or General Building Ventilation.
15.5.5 Personal Protective Equipment.
15.6 The Incentive for Pollution Prevention.
15.7 Case Histories.
15.7.1 Printing Facility.
15.7.2 Semiconductor and Pharmaceutical Industries.
15.7.3 Parts Cleaner.
15.7.4 Film Facility.
Literature Cited.
Chapter 16. Volatile Organic-Liquid Storage.
16.1 Introduction.
16.2 Nature of Emissions Sources.
16.3 Regulatory Outlook.
16.4 How Do Emissions Originate?
16.4.1 Roof Tanks.
16.4.2 Floating Roof Tanks.
16.4.3 Stratification.
16.4.4 Estimating Emissions.
16.4.5 Fugitive Emissions (Equipment Leaks).
16.5 The Pollution-Prevention Continuum.
16.6 Discussion.
16.6.1 Source Reduction of Breathing Losses.
16.6.2 Source Reduction of Working Losses.
16.6.3 Other Source Reduction Approaches.
16.6.4 Floating Roofs.
16.6.5 Pressure Vessels.
16.6.6 End-of-Pipe Controls.
16.7 Technology Selection Criteria.
16.7.1 Floating Roofs.
16.7.2 Dedicated Control Device.
16.7.3 Pressure Vessel.
16.7.4 Headered Control Device.
16.7.5 Source Reduction Options.
16.8 Case Histories.
16.8.1 Refrigerated Vent Condenser.
16.8.2 Headered Vent System.
16.8.3 Floating Roofs.
16.8.4 Pressure Vessels.
Literature Cited.
Chapter 17. Separation Technology Selection.
17.1 Introduction.
17.2 Pollution-Prevention Strategies.
17.2.1 Selection Heuristics.
17.2.2 Separation Unit-Operation Selection.
17.3 Unit Operation Parameters.
17.3.1 Distillation.
17.3.2 Crystallization.
17.3.3 Liquid-Liquid Extraction.
17.3.4 Adsorption.
17.3.5 Membranes.
17.4 Case Histories.
17.4.1 Distillation: New Design Criteria.
17.4.2 Distillation: Recovery of Waste.
17.4.3 Crystallization: New Technology.
17.4.4 Extraction: Thermodynamic Review.
17.4.5 Adsorption: Technology Selection.
17.4.6 Membranes: Process Simplification.
Literature Cited.
Chapter 18. Equipment Leaks: Regulations, Impacts, and Strategies.
18.1 Fugitive Emissions.
18.2 New Regulations in Mid-1994.
18.3 Recordkeeping Setup.
18.4 Strategy for Valves.
18.5 Learnings from a Study of Pump Seals.
18.6 Strategy from Pumps.
Literature Cited.
Appendix A. A Collection of Pollution-Prevention Opportunities.
A.1 Introduction.
A.2 Did You Know That…
A.3 Pollution-Prevention Opportunities List.
A.3.1 Process/Product Conceptualization and Development.
A.3.2 Plant Design.
A.3.3 Plant Operation.
Literature Cited.
Appendix B. Description of Screened Ideas From Case Study.
What People are Saying About This
“…an instructional manual for debugging the chemical process industries…helps the chemical engineer recognize pollution prevention as nothing more than a reformulation of traditional chemical engineering problem-solving…”—Scott Butner, Senior Research Scientist, Environmental technology Division, Pacific Northwest National Laboratory
“…an excellent nuts, bolts, pumps, and pipes P2 guidance test for process engineers. The engineer or manager charged with developing P2 solutions for his or her company would be well advised to consider the advice and suggestions offered by Mulholland and Dyer.”—Harry Freeman, Director, Louisiana Environmental Leadership Pollution Prevention Program