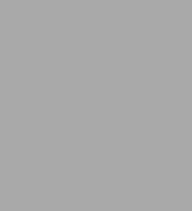
Process Engineering: Addressing the Gap between Study and Chemical Industry
574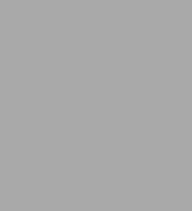
Process Engineering: Addressing the Gap between Study and Chemical Industry
574Paperback(3rd, Revised and Extended Edition)
-
PICK UP IN STORECheck Availability at Nearby Stores
Available within 2 business hours
Related collections and offers
Overview
Process Engineering is based on almost 30 years of practical experience of the author in process simulation, design and development. The book is a missing link between students and practitioners. The author has coached many graduates in their first months and knows what the typical questions are.
Coming from the university, graduates often do not know which relevance their knowledge has and how to apply it in real life, whereas established practitioners often stick to the narrow way of their experience, forgetting that science continuously makes progress. There is a gap to be bridged.
From his own professional experience, the author covers many topics of the process engineering business, but three guest contributions are a valuable supplement to the content of the third edition. Already in the 2nd edition, Verena Haas from BASF SE wrote an excellent chapter on dynamic process simulation. For the new 3rd edition, Gökce Adali and Michael Benje added two chapters on digitalization and patents, respectively.
Preparing the reader for the everyday business!
Product Details
ISBN-13: | 9783111028118 |
---|---|
Publisher: | De Gruyter |
Publication date: | 11/20/2023 |
Series: | De Gruyter Textbook |
Edition description: | 3rd, Revised and Extended Edition |
Pages: | 574 |
Product dimensions: | 6.69(w) x 9.45(h) x (d) |
Age Range: | 18 Years |
About the Author
Table of Contents
Preface vii
Preface to the 2nd edition ix
1 Engineering projects 1
1.1 Process engineering activities 1
1.2 Realization of a plant 8
1.3 Cost estimation 18
2 Thermodynamic models in process simulation 25
2.1 Phase equilibria 27
2.2 φ-φ-approach 32
2.3 γ-φ-approach 40
2.3.1 Activity coefficients 40
2.3.2 Vapor pressure and liquid density 49
2.3.3 Association 54
2.4 Electrolytes 56
2.5 Liquid-liquid equilibria 59
2.6 Solid-liquid equilibria 62
2.7 φ-φ-approach with gE mixing rules 64
2.8 Enthalpy calculations 66
2.9 Model choice and data management 69
2.10 Binary parameter estimation 73
2.11 Model changes 75
2.12 Transport properties 76
3 Working on a process 81
3.1 Flowsheet setup 82
3.2 PID discussion 92
3.3 Heat integration options 97
3.4 Batch processes 105
3.5 Equipment design 109
3.6 Troubleshooting 110
3.7 Dynamic process simulation 113
3.7.1 Basic considerations for dynamic models 115
3.7.2 Basics of Process Control for Dynamic Simulations 118
4 Heat exchangers 127
4.1 Something general 127
4.2 Shell-and-tube heat exchangers 129
4.3 Heat exchangers without phase change 130
4.4 Condensers 141
4.5 Evaporators 143
4.6 Plate heat exchangers 152
4.7 Double pipes 154
4.8 Air coolers 154
4.9 Fouling 156
4.10 Vibrations 158
5 Distillation and absorption 163
5.1 Thermodynamics of distillation and absorption columns 166
5.2 Packed columns 168
5.3 Maldistribution in packed columns 179
5.4 Tray columns 181
5.5 Comparison between packed and tray columns 201
5.6 Distillation column control 203
5.7 Constructive issues in column design 208
5.8 Separation of azeotropic systems 211
5.9 Rate-based approach 214
5.10 Dividing wall columns 216
5.11 Batch distillation 219
5.12 Troubleshooting in distillation 221
6 Two liquid phases 225
6.1 Liquid-liquid separators 225
6.2 Extraction 228
6.2.1 Mixer-settler arrangement 231
6.2.2 Extraction columns 232
6.2.3 Centrifugal extractors 235
7 Alternative separation processes 237
7.1 Membrane separations 237
7.2 Adsorption 245
7.3 Crystallization 252
8 Fluid flow engines 257
8.1 Pumps 257
8.2 Compressors 265
8.3 Jet pumps 274
8.4 Vacuum generation 277
9 Vessels and separators 283
10 Chemical reactions 291
10.1 Reaction basics 291
10.2 Reactors 299
11 Mechanical strength and material choice 307
12 Piping and measurement 313
12.1 Pressure drop calculation 313
12.1.1 Single-phase flow-through pipes 313
12.1.2 Pressure drops in special piping elements 318
12.1.3 Pressure drop calculation for compressible fluids 318
12.1.4 Two-phase pressure drop 321
12.2 Pipe specification 327
12.3 Valves 329
12.3.1 Isolation valves 329
12.3.2 Control valves 332
12.4 Measurement devices 334
13 Utilities and waste streams 339
13.1 Steam and condensate 339
13.2 Heat transfer oil 346
13.3 Cooling media 346
13.4 Exhaust air treatment 348
13.4.1 Condensation 351
13.4.2 Combustion 354
13.4.3 Absorption 359
13.4.4 Biological exhaust air treatment 361
13.4.5 Exhaust air treatment with membranes 362
13.4.6 Adsorption processes 363
13.5 Waste water treatment 364
13.6 Biological waste water treatment 367
14 Process safety 371
14.1 HAZOP procedure 375
14.2 Pressure relief 380
14.2.1 Introduction 380
14.2.2 Mass flow to be discharged 384
14.2.3 Fire case 386
14.2.4 Actuation cases 392
14.2.5 Safety valve peculiarities 399
14.2.6 Maximum relief amount 402
14.2.7 Two-phase-flow safety valves 411
14.3 Explosions 414
Glossary 419
List of Symbols 427
Bibliography 431
A Some numbers to remember 443
B Pressure drop coefficients 447
Index 451