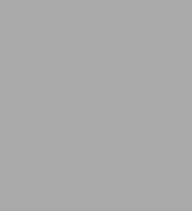
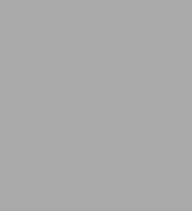
Paperback
-
SHIP THIS ITEMIn stock. Ships in 1-2 days.PICK UP IN STORE
Your local store may have stock of this item.
Available within 2 business hours
Related collections and offers
Overview
Product Details
ISBN-13: | 9783110632057 |
---|---|
Publisher: | De Gruyter |
Publication date: | 05/10/2021 |
Series: | De Gruyter Textbook |
Pages: | 362 |
Product dimensions: | 6.69(w) x 9.45(h) x (d) |
Age Range: | 18 Years |
About the Author
Table of Contents
Preface vii
Acknowledgments ix
1 Introduction 1
2 The run-up to the Industrial Revolution 3
2.1 Purpose of this chapter 3
2.2 The importance of the First and Second Industrial Revolutions 3
2.3 Population growth 4
2.4 Living conditions 6
2.5 Food 7
2.6 Clothing 8
2.7 Social structure 9
2.8 Transportation 11
2.9 Transfer of science and technology 12
2.10 Banking 14
2.11 Resume: population growth, social changes and industrialization - a virtuous circle 15
3 Historical evolution of occupational health and safety in the nineteenth century 17
3.1 Industrialization in the nineteenth century takes a high toll 17
3.1.1 Main industries: textile, railroads and mining 17
3.1.2 Statistics on accidents for railroad workers 18
3.1.3 Statistics on accidents in mining 19
3.1.4 Statistics on accidents in textile industry 20
3.2 Influence of the liberal thought in the nineteenth century 22
3.2.1 The century of the revolutions 22
3.2.2 Employers-workers: a new relationship 24
3.2.3 Contributory negligence 24
3.2.4 Fellow servant rule 25
3.2.5 Volenti non fit injuria or voluntary assumption of risk 26
3.2.6 Free agent doctrine 27
3.3 Influence of economic thought in the nineteenth century 29
3.4 Utopian socialism 33
3.5 Renewed political Insight at the end of the nineteenth century 33
3.5.1 Trade unions request for better compensation laws 33
3.5.2 The International Workingmen's Association (IWA) 35
3.5.3 New compensation laws 36
3.5.4 A first revolution in thinking about occupational health and safety 36
3.6 A more scientific approach to safety at work at the turn of the nineteenth century 42
3.6.1 Leading studies 42
3.6.2 John Calder study (1899) 43
3.6.3 The Pittsburg survey (1907-1908) 45
3.6.4 Pamphlet of the Fidelity and Casualty Company, 1909 51
3.6.5 Paradigm shift on prevention of work-re la ted accidents at the start of the twentieth century 53
3.7 The evolution of occupational health and safety in the twentieth century 54
3.7.1 Purpose of this chapter 54
3.7.2 The international Labour Organization 55
3.7.3 Technical standards 56
3.7.4 Safety and health standards and rules 58
3.7.5 Safeguarding of machinery 64
3.7.6 Safety education, training of people 65
3.7.7 Short service workers 67
3.7.8 Safety information (posters, bulletins, etc.) 67
3.7.9 Job safety analysis 69
3.7.10 Safety departments, safety committees 71
3.7.11 Management, leadership and importance of supervision-73
3.7.12 Inspection and checklists 80
3.7.13 Human behavior 81
3.7.13.1 The syndrome of accident proneness 81
3.7.13.2 Scientific management approach to human performance improvement 84
3.7.13.3 Industrial, work and organizational psychology 88
3.7.13.4 Some "old-new" simple approaches 96
3.7.13.5 Human behavior is not a root cause 98
3.8 Evidence-based safety 103
3.9 Tribute to Heinrich and Bird 105
3.9.1 Influential authors on occupational safety 105
3.9.2 Herbert William Heinrich 106
3.9.3 Frank E. Bird Jr. 107
3.9.4 Discussion on the 1-29-300 and the 1-10-30-600 rule 110
3.9.5 Is there a correlation between fatal accidents and nonfatal accidents? 114
3.9.6 Safety management systems 116
3.9.7 Safety culture 124
3.10 Some final thoughts about the evolution of OHS since 1900 133
3.10.1 Short resume of the OHS approach since 1900 133
3.10.2 Quantitative decrease in accidents in the twentieth century 134
3.10.3 New victims but same accidents 136
3.10.4 Fundamentals for occupational health and safety 139
3.10.5 Occupational health and safety is a result-oriented activity 142
3.10.6 Occupational health and safety in the twenty-first century: mental health and well-being 143
4 Technological risks 145
4.1 Introduction of new technologies 145
4.2 Discovery of major risks related to new technologies or products 145
4.2.1 What are major risks? 145
4.2.2 Discovery of major risks with steam boilers 147
4.2.3 Discovery of major risks with nuclear energy 149
4.2.4 Discovery of major risks with new products 153
4.2.5 Discovery of major risks in the process industries 154
4.2.6 Discovery of major risks in renewable energy: BESS 157
4.3 Technological accidents are complex and complicated because of uncertainties 160
4.4 Why do we have to deal with risks? 161
4.5 How to deal with risks? 163
4.5.1 Different risk approaches 163
4.5.2 Psychological risk approach 164
4.5.3 Sociological risk approach 166
4.5.4 Cultural risk approach 168
4.5.5 Actuarial approach of risk 168
4.5.6 Toxicological and epidemiological approach of risk 169
4.5.7 Economic approach of risk 172
4.5.8 Engineering approach of risk 173
5 Process safety: an engineering discipline 175
5.1 Engineering 175
5.2 Process installations 176
5.3 The framework to perform risk management of process installations 177
5.4 Application of industry standards and best practices 177
5.4.1 Engineering standards 177
5.4.2 The role of the process safety engineer 179
5.5 Hazard identification 181
5.5.1 Hazard, danger and hazardous event 181
5.5.2 Hazard identification techniques 183
5.5.3 Overview of some specific hazard identification techniques 185
5.5.3.1 Prior to starting to use a specific hazard identification technique 185
5.5.3.2 Most recommended method 185
5.5.3.3 How to be sure that all hazardous events have been identified? 187
5.5.3.4 Preliminary hazard analysis 188
5.5.3.5 HAZID 188
5.5.3.6 Hazard and operability study 189
5.5.3.7 Safety audit and checklist review 199
5.5.3.8 Structured What If Checklist Technique 199
5.5.3.9 Failure mode and effect analysis 200
5.5.4 Selection of an appropriate specific hazard identification technique 205
5.6 Developing scenarios 206
5.6.1 Undesired event versus accidental scenario 206
5.6.2 Fault tree analysis 207
5.6.3 Event tree analysis 210
5.6.4 Cause-consequence diagram and bow-tie method 210
5.6.5 Generic scenario generation 210
5.7 Probability analysis 213
5.7.1 Understanding the use of probabilities in risk studies 213
5.7.2 Types of probabilities used in quantitative risk analysis 214
5.7.3 Sources of data 215
5.7.4 Engineering approach for selecting failure data 223
5.7.5 Frequency, fractional dead time and failure on demand 226
5.8 Consequence analysis 228
5.8.1 Qualitative approach 228
5.8.2 The use of (mathematical) models 229
5.8.3 Effect analysis 232
5.8.3.1 Terminology 232
5.8.3.2 Methods and models for the calculation of the physical effects 234
5.8.3.3 Current challenges with effect modeling 236
5.8.4 Impact analysis 237
5.8.4.1 Methods for impact analysis 237
5.8.4.2 Single value criteria for impact analysis 238
5.8.4.3 Statistical approach (use of probits) 246
5.8.4.4 Mathematical analysis of impact on buildings and structures 255
5.9 Risk analysis and risk assessment for individual scenarios 260
5.9.1 Risk analysis versus risk assessment 260
5.9.2 Criteria for risk assessment 261
5.9.3 Risk matrix 264
5.9.4 Aggregate risk analysis and assessment 268
5.10 Pitfalls in risk assessments 270
5.11 Risk reduction measures 271
5.11.1 The basic assumption of risk reduction measures 271
5.11.2 Defense-in-depth principle: multiple layer approach 272
5.11.3 The first layer of protection: design and engineering, inherent safe design 278
5.11.4 The second layer of protection: operations 284
5.11.5 The third layer of protection: automated active protection and passive protection systems 294
5.11.5.1 Purpose of the third layer 294
5.11.5.2 Active versus passive protection systems 294
5.11.5.3 Automated active protection systems and functional safety systems 295
5.11.5.4 Passive protection systems 299
5.11.6 The fourth layer of protection: incident management system 299
6 Process safety risk-based management 303
6.1 Major disasters are organizational accidents 303
6.2 The pillars of a risk-based management strategy 304
6.3 Can we use the recipes of management of occupational health and safety? 306
6.4 The senior process safety engineer 309
6.4.1 The role and positioning of the senior process safety engineer 309
6.4.2 Relation with the process engineer 310
6.4.3 Relation with technical inspection 310
6.4.4 Relation with maintenance 311
6.4.5 Relation with operations 311
6.4.6 STEM 311
6.4.7 Legal requirements 312
6.4.8 Automatization and instrumentation 312
6.4.9 Reliability 312
6.4.10 Metallurgy 312
6.4.11 Social science 313
6.4.12 Structural engineering 313
6.4.13 Specific knowledge 313
6.4.14 Main tasks of the senior process safety engineer 314
7 Conclusion 315
7.1 Occupational Health and Safety 315
7.2 Process safety 317
Appendix I SWIFT categories and questions 319
References 331
Index 345