5
1
9780367415716
ReducedEffort® Changeover: The Lean Way to Quickly Reduce Changeover Downtime, Second Edition / Edition 1 available in Hardcover, eBook
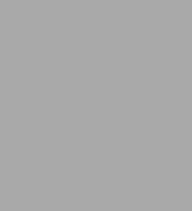
ReducedEffort® Changeover: The Lean Way to Quickly Reduce Changeover Downtime, Second Edition / Edition 1
- ISBN-10:
- 0367415712
- ISBN-13:
- 9780367415716
- Pub. Date:
- 03/31/2020
- Publisher:
- Productivity Press Inc.
- ISBN-10:
- 0367415712
- ISBN-13:
- 9780367415716
- Pub. Date:
- 03/31/2020
- Publisher:
- Productivity Press Inc.
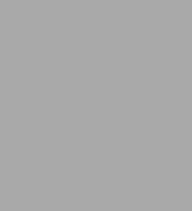
ReducedEffort® Changeover: The Lean Way to Quickly Reduce Changeover Downtime, Second Edition / Edition 1
$180.0
Current price is , Original price is $180.0. You
180.0
In Stock
Product Details
ISBN-13: | 9780367415716 |
---|---|
Publisher: | Productivity Press Inc. |
Publication date: | 03/31/2020 |
Pages: | 192 |
Product dimensions: | 7.00(w) x 10.00(h) x (d) |
About the Author
From the B&N Reads Blog