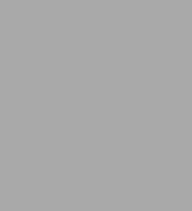
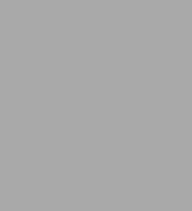
eBook
Available on Compatible NOOK devices, the free NOOK App and in My Digital Library.
Related collections and offers
Overview
Mechatronics is a multidisciplinary field combining Mechanical, Electronic, Computer, and other Engineering fields to develop intelligent processes and products. Based on thirty years of extensive work in industry and teaching, this book provides an overview of the sensors and sensor systems required and applied in mechatronics with an emphasis on understanding the physical principles and possible configurations of sensors rather than simply a discussion of particular types of sensors. Well illustrated with examples of commercially available sensors and of recent and future developments, this book offers help in achieving the best solution to various kinds of sensor problems encountered in mechatronics. In a clear and detailed manner, the author reviews the major types of transducers, presents a characterization of the state-of-the-art in sensing technology and offers a view on current sensor research. This book will be a vital resource for practicing engineers and students in the field.
- Comprehensive coverage of a wide variety of sensor concepts and basic measurement configurations encountered in the mechatronics domain
- Written by a recognized expert in the field who has extensive experience in industry and teaching
- Suitable for practicing engineers and those wanting to learn more about sensors in mechatronics
Product Details
ISBN-13: | 9780123944092 |
---|---|
Publisher: | Elsevier Science |
Publication date: | 01/17/2012 |
Sold by: | Barnes & Noble |
Format: | eBook |
Pages: | 322 |
File size: | 6 MB |
About the Author
Read an Excerpt
Sensors for Mechatronics
By Paul P.L. Regtien
ELSEVIER
Copyright © 2012 Elsevier Inc.All right reserved.
ISBN: 978-0-12-394409-2
Chapter One
Introduction
Worldwide, sensor development is a fast growing discipline. Today's sensor market offers thousands of sensor types, for almost every measurable quantity, for a broad area of applications, and with a wide diversity in quality. Many research groups are active in the sensor field, exploring new technologies, investigating new principles and structures, aiming at reduced size and price, at the same or even better performance.
System engineers have to select the proper sensors for their design, from an overwhelming volume of sensor devices and associated equipment. A well motivated choice requires thorough knowledge of what is available on the market, and a good insight in current sensor research to be able to anticipate forthcoming sensor solutions.
This introductory chapter gives a general view on sensors – their functionality, the nomenclature and global properties – as a prelude to a more in-depth discussion about sensor performance and operation principles.
1.1 Sensors in Mechatronics
1.1.1 Definitions
A transducer is an essential part of any information processing system that operates in more than one physical domain. These domains are characterized by the type of quantity that provides the carrier of the relevant information. Examples are the optical, electrical, magnetic, thermal and mechanical domains. A transducer is that part of a measurement system that converts information about a measurand from one domain to another, ideally without information loss.
A transducer has at least one input and one output. In measuring instruments, where information processing is performed by electrical signals, either the output or the input is of electrical nature (voltage, current, resistance, capacitance and so on), whereas the other is a non-electrical signal (displacement, temperature, elasticity and so on). A transducer with a non-electrical input is an input transducer, intended to convert a non-electrical quantity into an electrical signal in order to measure that quantity. A transducer with a non-electrical output is called an output transducer, intended to convert an electrical signal into a non-electrical quantity in order to control that quantity. So, a more explicit definition of a transducer is an electrical device that converts one form of energy into another, with the intention of preserving information.
According to common terminology, these transducers are also called sensor and actuator, respectively (Figure 1.1). So, a sensor is an input transducer and an actuator is an output transducer. It should be noted, however, that this terminology is not standardized. In literature other definitions are found. Some authors make an explicit difference between a sensor and a (input) transducer, stressing a distinction between the element that performs the physical conversion and the complete device – for instance, a strain gauge (the transducer) and a load cell (the sensor) with one or more strain gauges and an elastic element.
Attempts to standardize terminology in the field of metrology have resulted in the Vocabulaire International de Métrologie (VIM). According to this document a transducer is a device, used in measurement, that provides an output quantity having a specified relation to the input quantity. The same document defines a sensor as the element of a measuring system that is directly affected by a phenomenon, body or substance carrying a quantity to be measured.
Modern sensors not only contain the converting element but also part of the signal processing (analogue processing such as amplification and filtering, AD conversion and even some digital electronics). Many of such sensors have the electronics integrated with the transducer part onto a single chip. Present-day sensors may have a bus-compatible output, implying full signal conditioning on board. There is a trend to also include transmission electronics within the device, for instance for biomedical applications.
Signal conditioning may be included:
to protect the sensor from being loaded or to reduce loading errors;
to match the sensor output range to the input range of the ADC;
to enhance the S/N (signal-to-noise ratio) prior to further signal processing;
to generate a digital, bus-compatible electrical output; or
to transmit measurement data for wireless applications.
In conclusion, the boundaries between sensor and transducer as proclaimed in many sensor textbooks are disappearing or losing their usefulness: the user buys and applies the sensor system as a single device, with a non-electrical input and an electrical (e.g. analogue, digital and bus compatible) output.
1.1.2 Sensor Development
Sensors provide the essential information about the state of a (mechatronic) system and its environment. This information is used to execute prescribed tasks, to adapt the system properties or operation to the (changing) environment or to increase the accuracy of the actions to be performed.
Sensors play an important role not only in mechatronics but also in many other areas. They are widely applied nowadays in all kind of industrial products and systems. A few examples are as follows:
Consumer electronics
Household products
Public transport, automotive
Process industry
Manufacturing, production
Agriculture and breeding industry
Medical instruments
and many other areas where the introduction of sensors has increased dramatically the performance of instruments, machines and products.
The world sensor market is still growing substantially. The worldwide sensor market offers over 100,000 different types of sensors. This figure not only illustrates the wide range of sensor use but also the fact that selecting the right sensor for a particular application is not a trivial task. Reasons for the increasing interest in sensors are as follows:
Reduced prices: the price of sensors not only depends on the technology but also on production volume. Today, the price of a sensor runs from several ten thousands of euros for single pieces down to a few eurocents for a 100 million volume.
Miniaturization: the IC-compatible technology and progress in micromachining technology are responsible for this trend. Pressure sensors belong to the first candidates for realization in silicon (early 1960s). Micro-ElectroMechanical Systems (MEMS) are gradually taking over many traditionally designed mechanical sensors. Nowadays, solid-state sensors (in silicon or compatible technology) for almost every quantity are available, and there is still room for innovation in this area.
Smart sensing: the same technology allows the integration of signal processing and sensing functions on a single chip. Special technology permits the processing of both analogue and digital signals ('mixed signals'), resulting in sensor modules with (bus compatible) digital output.
Popular MEMS sensors are accelerometers and gyroscopes. A MEMS accelerometer can be made completely out of silicon, using micromachining technology. The seismic mass is connected to the substrate by thin, flexible beams, acting as a spring. The movement of the mass can be measured by, for instance, integrated piezoresistors positioned on the beam at a location with maximum deformation (Chapter 4) or by a capacitive method (Chapter 5).
In mechatronics, mainly sensors for the measurement of mechanical quantities are encountered. The most frequent sensors are for displacement (position) and force (pressure), but many other sensor types can be found in a mechatronic system.
Many sensors are commercially available and can be added to or integrated into a mechatronic system. This approach is preferred for systems with relatively simple tasks and operating in a well-defined environment, as commonly encountered in industrial applications. However, for more versatile tasks and specific applications, dedicated sensor systems are required, which are often not available. Special designs, further development or even research are needed to fulfil specific requirements, for instance with respect to dimensions, weight, temperature range and radiation hardness.
1.1.3 Sensor Nomenclature
In this book, we follow a strict categorization of sensors according to their main physical principle. The reason for this choice is that sensor performance is mainly determined by the physics of the underlying principle of operation. For example, a position sensor can be realized using resistive, capacitive, inductive, acoustic and optical methods. The sensor characteristics are strongly related to the respective physical transduction processes. However, a magnetic sensor of a particular type could be applied as, for instance, a displacement sensor, a velocity sensor or a tactile sensor. For all these applications the performance is limited by the physics of this magnetic sensor.
Apparently, position and movement lead the list of measurement quantities. Common parlance contains many other words for position parameters. Often, transducers are named after these words. Here is a short description of some of these transducers.
Distance sensor Measures the length of the straight line between two defined points Position sensor Measures the co-ordinates of a specified point of an object in a specified reference system Displacement Measures the change of position relative to a reference point sensor Range sensor Measures in a 3D space the shortest distance from a reference point (the observer) to various points of object boundaries in order to determine their position and orientation relative to the observer or to get an image of these objects Proximity (a) Determines the sign (positive or negative) of the linear distance sensor between an object point and a fixed reference point; also called a switch (b) A contact-free displacement or distance sensor for short distances (down to zero) Level sensor Measures the distance of the top level of a liquid or granular substance in a container with respect to a specified horizontal reference plane Angular sensor Measures the angle of rotation relative to a reference position Encoder Displacement sensor (linear or angular) containing a binary coded ruler or disk Tilt sensor Measures the angle relative to the earth's normal Tachometer Measures rotational speed Vibration Measures the motion of a vibrating object in terms of displacement, sensor velocity or acceleration Accelerometer Measures acceleration
Transducers for the measurement of force and related quantities are as follows:
Pressure sensor Measures pressure difference, relative to either vacuum (absolute pressure), a reference pressure or ambient pressure Force sensor Measures the (normal and/or shear) force exerted on the active point of the transducer Torque sensor Measures torque (moment) Force–torque Force or pressure sensor, for measuring weight sensor Load cell Strain gauge Measures linear relative elongation (positive or negative) of an object, caused by compressive or tensile stress Touch sensor Detects the presence or (combined with a displacement sensor) the position of an object by making mechanical contact Tactile sensor Measures 3D shape of an object by the act of touch, either sequentially using an exploring touch sensor or instantaneously by a matrix of force sensors
Many transducers have been given names according to their operating principle, construction or a particular property. Examples are as follows:
Hall sensor Measures magnetic field based on the Hall effect, after the American physicist Edwin Hall (1855–1938) Coriolis mass flow Measures mass flow of a fluid by exploiting the Coriolis force sensor exerted on a rotating or vibrating channel with that fluid; after Gustave-Gaspard de Coriolis, French scientist (1792–1843)
(Continues...)
Excerpted from Sensors for Mechatronics by Paul P.L. Regtien Copyright © 2012 by Elsevier Inc.. Excerpted by permission of ELSEVIER. All rights reserved. No part of this excerpt may be reproduced or reprinted without permission in writing from the publisher.
Excerpts are provided by Dial-A-Book Inc. solely for the personal use of visitors to this web site.
Table of Contents
1: Introduction
2: Sensor fundamentals
3: Uncertainty aspects
4: Resistive sensors
5: Capacitive sensors
6: Inductive and magnetic sensors
7: Optical sensors
8: Piezoelectric sensors
9: Acoustic sensors
Appendix A Symbols and Notations
Appendix B Relations between quantities
Appendix C Basic interface circuits
What People are Saying About This
Provides a clear and practical overview of sensor use in mechatronics for all levels of engineers and students