In our mechanized day of mass production, the craft of hand-forming sheet metal into compound curves and dashing fins and fenders is fast becoming a lost art. Eddie Paul is a master at sheet metal fabrication (among other accomplishments), and in this book he gives readers the means to mold their own sheet metal creations. Paul’s engagingly written book talks about the necessary tools and how to use them; how to choose, prepare and work with the right material; how to make forms and mock-ups, and much more. Whether you want to mold a fender for a custom car or just learn about this intriguing process, Sheet Metal Fabrication is a thoroughly readable reference book and guide, and a uniquely valuable resource.
In our mechanized day of mass production, the craft of hand-forming sheet metal into compound curves and dashing fins and fenders is fast becoming a lost art. Eddie Paul is a master at sheet metal fabrication (among other accomplishments), and in this book he gives readers the means to mold their own sheet metal creations. Paul’s engagingly written book talks about the necessary tools and how to use them; how to choose, prepare and work with the right material; how to make forms and mock-ups, and much more. Whether you want to mold a fender for a custom car or just learn about this intriguing process, Sheet Metal Fabrication is a thoroughly readable reference book and guide, and a uniquely valuable resource.
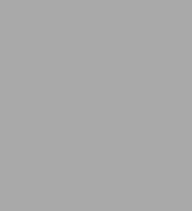
Sheet Metal Fabrication: Techniques and Tips for Beginners and Pros
160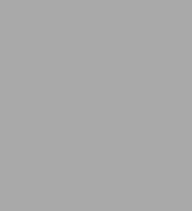
Sheet Metal Fabrication: Techniques and Tips for Beginners and Pros
160Paperback(First)
Product Details
ISBN-13: | 9780760327944 |
---|---|
Publisher: | Motorbooks |
Publication date: | 03/15/2008 |
Series: | Motorbooks Workshop Series |
Edition description: | First |
Pages: | 160 |
Product dimensions: | 8.25(w) x 11.12(h) x 0.50(d) |