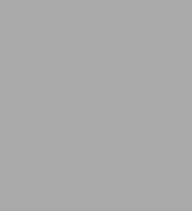
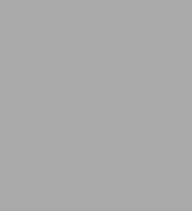
eBook
Available on Compatible NOOK devices, the free NOOK App and in My Digital Library.
Related collections and offers
Overview
Product Details
ISBN-13: | 9781567263879 |
---|---|
Publisher: | Berrett-Koehler Publishers |
Publication date: | 05/01/2004 |
Series: | Project Management Essential Library |
Sold by: | Barnes & Noble |
Format: | eBook |
Pages: | 88 |
File size: | 2 MB |
About the Author
Read an Excerpt
Six Sigma for Project Managers
By Steve Neuendorf
Management Concepts Press
Copyright © 2004 Management Concepts, Inc.All rights reserved.
ISBN: 978-1-56726-387-9
CHAPTER 1
What Is Six Sigma?
Sigma (σ) is the Greek symbol used in statistics to indicate the statistical property of a set of grouped data called "standard deviation." If you are fairly well versed in statistics, you would say that is pretty elementary; if not, you would say it's Greek to you. Either way you would be right.
"Grouped data" refers to any set of data that are somehow related. If you are rolling dice, for example, all the data from each roll for however many rolls would be grouped data, because all the data come from the same system of rolled dice. Eventually, after rolling the dice enough times and analyzing the results, you no longer need to roll the dice and collect and analyze the data to predict the likelihood of the next roll or several rolls. We would say that rolling a 7 is the most likely outcome, since there are several ways the dice can be rolled to give a 7, just as we can say that rolling a 2 or a 12 is the least likely outcome, since there is only one way to roll either of those results.
With some analysis, we could create a "probability distribution" for rolling the dice that showed the probability of rolling any particular result. Lots of statistics can be derived from this type of data, but the ones we are interested in are the standard deviation, σ, and the average or mean — that is, the most likely result.
For any given distribution, the percentage of the results that falls within 1 standard deviation of the mean is a constant. Further, the percentage of results that falls within any number of standard deviations is a constant. For a normal distribution, about 64% of the results will fall within 1 standard deviation of the mean (1s), about 95% will fall within 2 standard deviations of the mean (2s), and about 99.9% will fall within 3 standard deviations (3s) (see Figure 1-1). For the mathematical derivation of six sigma, the area under the curve is 99.999999998%; in other words, about 2 parts per billion (ppb) are not under the curve. To illustrate, 2 ppb of the world's population (as of early 2003) would be 12 people.
While six sigma is at its roots all about statistics, in its application and practice it is very little about statistics except to a very few people. It is not likely to have much, if anything, to do with statistics for project managers. By analogy, temperature is all about the average speed of molecules, but making the room warmer has more to do with starting a fire, turning up the thermostat, or shutting the window than it does with the molecules and how they are moving. In the analogy, the result — a warmer room — is what is important; in six sigma, improved quality is what is important.
Nevertheless, we should note that standard deviation is a property of the number set. Since we are attributing the results represented in the number set to the measured results of a process, we can say that standard deviation is a property of the process. Any process will also have its "design objectives" as defined by its creators. This property is the "spec limit" or the "performance standard" for that process.
If we look at a manufacturing process, the spec limit might be expressed as a range about a dimension, such as a length of 10" ± 0.1." If the process is returning a customer call, the spec limit or performance standard might be stated as "by the end of the next business day." No matter what it is, we can treat the specification limit as independent of the observed statistics (mean and standard deviation) for that process. If the process is designed so that the performance distribution falls well within the spec limit or performance standard, then we would say we have "good quality" — that is, very few defects as defined by comparing the results with the spec limit or performance standard. On the other hand, if the process is defined so that a lot of the results fall outside of the spec limit, then we would say we have poor quality in the results.
So what can we do?
Changing the spec would be effective, but tough to do in the world of interchangeable parts or the need to make a good customer first impression. Changing the results (i.e., fixing all the defects) would be effective but expensive and wasteful. Or we can change the process to make sure that the most probable outcome is a result within the specification limits. Remember, the "tighter" the process (i.e., the smaller the standard deviation), the higher the percentage of the results that falls within the specification limits or performance standards.
Six sigma, or any statistical process control tool for that matter, is really about developing a congruency between the specification limit (performance standard) and process performance, such that the process is designed to perform within the specification limit. Six sigma goes one step further in "normalizing" the measurement of quality for use in any type of process or activity.
Just in the examples we have used so far — the dice, the temperature, the length, and the call return — we have four different units of measure: integers, degrees, inches, and business day. To the people responsible for any of these processes, the units of measure have meaning and usefulness, but to someone with responsibility for all of these processes collectively, the measures would only confuse whatever information is needed to manage these disparate processes effectively.
What six sigma does at the result level is express measurement as "defects," which can be defined as any failure to meet the specification limit or performance standard, and opportunities for defects, which can be defined as any place where the measurement could have indicated that a defect occurred. Further, the quality level is usually expressed as "defects per million opportunities for defects" (DPMO), or more succinctly as ppm (parts per million). With any activity's quality performance expressed as defects per million opportunities, one can effectively compare performance between very different activities and make decisions about where and how to focus improvement activity and resources.
As noted, if we measure any process, the results will be a set of grouped data. If we are measuring the number of defects produced by our process, we quantitatively know how much the process produced and how many defects were contained in that process.
Processes are somewhat like the concept of inertia in physics, which is that an object will remain in a constant state until it is acted upon by an outside force. Processes will tend to reproduce the same results until they are acted upon by an outside force. So, if you have a process that tends to produce so many defects in some measured amount of its output, that process can be expected to continue to produce that same number of defects until someone does something to change it. Once the process is changed and it has a new characteristic for producing defects (or for producing defect-free output), it will continue to operate at that level until it is acted upon again.
Organizations tend to think that projects are the alternative to process. That is, if something is done routinely there is no need to initiate a project to get it done. If we need something done just once or done differently from what we have done in the past, we might charter a project.
CHAPTER 2Six Sigma As a Metric
Measures are raw data; metrics comprise one or more measures expressed in a context that gives them meaning or usefulness that the measures by themselves may not have.
Metrics can be grouped into categories according to what types of activities and decisions they tend to reflect and support. Figure 2-1 identifies the general categories of measurement. Interestingly, the six sigma metric DPMO can be considered in the efficiency measurement category, especially when we look at the efficiency of matching the defect removal rate to the defect introduction rate for products and services. Alternatively, it can be considered in the effectiveness measurement category, where eliminating the production of defects is considered the right thing to do.
DEFINING DEFECTS
At its roots, six sigma is a metric; that is, two measures are used to derive the sigma value for quality for any given product or process:
1. The number of defects in that product or within an execution of that process
2. The number of opportunities for defects within that product or within an execution of that process.
As shown in Figure 2-2, some of the opportunities for defects are realized as defects. Much like "realized" and "recognized" in taxes, they are evident as defects only if they are measured at the appropriate control points in or after the process; otherwise, they manifest themselves as failures in subsequent steps of the process or in the hands of the end customer.
This sounds simple enough, but rigor must be used in defining a defect. Once a defect is defined, it is fairly easy to identify the number of opportunities; again, one must be rigorous.
Major problems with quality and quality management often arise as a result of the lack of some common operating definitions of terms. Figure 2-3 shows the terms used throughout this book, and how they relate.
Figure 2-3 distinguishes between internal and external and between errors and defects, but we generally refer to them collectively as defects. In practice it will be necessary to make these defect classification distinctions to evaluate the effectiveness of improving process (i.e., eliminating faults) with the resultant reduction or elimination of errors. In essence, achieving six sigma is much more about discovering and eliminating faults, which would eliminate all types of defects and all types of failures associated with defects.
The quality of a product or process is expressed as its defect density. This defect density is then compared with a standard determination of the sigma level associated with that particular value of defect density. The lower the observed defect density, the higher the sigma level for the quality of that set of products or process results.
A defect is not a direct measure. For example, say a manufacturing process produces a part that is supposed to be a certain length. The length of parts is measured as they are produced. Although the measures vary, the parts that fall within the range of the specified length plus or minus an also-specified length tolerance range are deemed "good" while those parts where the measured length falls outside of the specification range are considered defects. Each part produced is an opportunity for a defect with respect to its length. The defect density is the number of defective parts with respect to length divided by the total number of parts produced (or opportunities for defects).
Length is not the only aspect of the part that has a specification associated with it. A requirement for width may also be associated with the piece. Just as with length, when one part falls outside the width specification, it is counted as a defect. Again, each piece produced represents an opportunity for a width defect.
Defects do not have to be associated with a quantitative measure. A subjective specification such as "free of scratches" may be verified by an optical inspection step in the process. Any piece that is scratched in a manner that it would be considered not to meet this requirement would be counted as a defect; each piece produced would be counted as an opportunity for this type of defect.
Thus, each part may have many opportunities for defects and each part may also have many defects. This should also raise the question of what to do in the case where a part that contains a defect is rejected. Is the rejected part checked for defects against the other possible opportunities? The process of determining the right defect density level for a particular product or process can be complicated and is a possible source of error. An erroneous measure of defect density can cause a problem to be overlooked or create a situation where something that is not a problem is "corrected."
It is also important to make the distinction between a defect and a failure. A computer crash, a customer complaint, and a car that won't start are all failures. The relationship between defects and failures is "zero one or many to zero one or many." That is, a failure can occur even if there are no defects. Conversely, a defect may not result in a failure. Moreover, many defects can cause a single failure and one defect can cause many failures. In the calculation of the defect density using six sigma conventions, the distinction between defects and failures is very important.
SIX SIGMA AS A STRATEGIC-LEVEL METRIC
The different levels of an organization's metrics program identify a minimum of three levels: a strategic level, a tactical level, and a technical or operational level. Six sigma is a strategic-level metric. It can be used to express the quality of a product or of a process. More specifically, six sigma describes the characteristic of a process to produce defects or the results of a process (products) to contain defects. While it is possible to consider the quality of production or delivery of services an operational and tactical endeavor, six sigma treats it as a long-term strategic goal (see Figure 2-4).
To understand the usefulness of six sigma as a metric, it is necessary to understand that any process has certain properties or constants, including the cost required to execute the process (generally referred to as efficiency (E) or productivity), the quality of the results of the process (measured here as the defect density expressed in units of sigma (σ)), and the time it takes for that process to execute under defined conditions (referred to as the cycle-time (T)). It usually gets a smile when you tell someone "good, fast, or cheap — pick two," but this proposition reflects the nature and the interrelationship of these properties (dependent variables) for a process. The following expression describes the general relationship between these parameters for any selected process:
f(E, σ, T) = K where K is a constant for that process.
Defining "process" as a group of steps, methods, and means that are used to produce a result, it could be said that everything done is the result of a process. Certainly in business or in the endeavors of any organization, success depends on having the processes and executing them at the right level, time, and place.
Since every process has the property of quality, it is possible to apply six sigma measurement to evaluate the quality performance of that process. So, as a strategic metric, sigma quality metrics can be used to compare quality performance and performance improvement between departments or product lines using valid and accurate measures without the need to understand or interpret the differences between the underlying processes being evaluated and compared.
While sigma-level metrics work very well at the strategic level, they are not particularly well-suited for use as tactical or operational metrics. You would not get the desired result, for example, if you were to tell the operator of a machine that a higher level of sigma was needed in the next quarter. But if you focused the instruction on a particular type of defect and the operator was able to reduce the number of rejects for that type of defect without changing the rate of production for other types of defects, then the quality performance, as measured in sigma units, would improve.
By the same reasoning, sigma metrics use measures that are also used to produce other tactical and operational metrics that are more specifically focused on process control and decision points. If these other metrics are used to execute effective control and make the right decisions that improve processes, the later analysis evaluating the sigma level of the process and the effects of the changes should reflect the improvements. In and of themselves, however, the sigma metrics are only the quantitative assessment of performance and change, not insight into what constitutes quality or the nature of the changes.
It is as important that sigma quality measures evaluate the quality performance of a process as it is that they evaluate the changes in the quality performance for a process. As a strategic metric, sigma quality metrics are useful to an organization in evaluating efforts to improve the processes used to fulfill the organization's mission. So, sigma metrics can be unambiguously used to evaluate the performance and the change in performance between any processes employed by the organization and over any time period selected to evaluate the effectiveness of efforts to improve.
Six sigma is expressed and reported as the sigma level associated with the observed ratio of defects per opportunity for defects, or more specifically, defects per million opportunities. The sigma level of quality is generally expressed analogous to the chemical terminology of parts per million (ppm).
(Continues...)
Excerpted from Six Sigma for Project Managers by Steve Neuendorf. Copyright © 2004 Management Concepts, Inc.. Excerpted by permission of Management Concepts Press.
All rights reserved. No part of this excerpt may be reproduced or reprinted without permission in writing from the publisher.
Excerpts are provided by Dial-A-Book Inc. solely for the personal use of visitors to this web site.
Table of Contents
Contents
Preface,CHAPTER 1 What Is Six Sigma?,
CHAPTER 2 Six Sigma As a Metric,
CHAPTER 3 Six Sigma As a Goal,
CHAPTER 4 Six Sigma "by the Belts",
CHAPTER 5 Implementing a Formal SixSigmaProgram,
CHAPTER 6 "Ultimate" Six Sigma,
CHAPTER 7 Applying Six Sigma to Project Management,
CHAPTER 8 Organizing for Six Sigma,
Index,