5
1
9780128102268
Preface
List of Figures
List of Tables
1 Before You Begin
1.1 Introduction
1.2 Standards
1.2.1 Standard Drawings
1.2.2 Charts
1.2.3 Drawing Templates and Drawing Standards
1.2.4 Drawing Numbering
1.2.5 3-D Model Numbering
1.2.6 Material Commodity Codes
1.3 Specifications
1.3.1 Piping Classes
1.4 Procedures
1.4.1 Stick Files
1.4.2 Inter-discipline Drawing Reviews
1.4.3 Line Numbering
1.4.4 Stress Analysis
1.4.5 CAD Set-up
1.4.6 3-D Model Reviews
1.4.7 Checking
1.4.8 Manhour Estimating
1.4.9 Progress Reporting
1.4.10 Management of Change
1.4.11 As-Builting
1.4.12 Project Close-out
1.5 Piping Execution Plan
1.5.1 Design Basis Memorandum (DBM)
1.5.2 Project Execution Plan (PEP)
1.5.3 Contracting and Procurement Plan and Construction Execution Plan
1.6 Conclusion
2 Procedures
2.1 Introduction
2.2 Master Stick Files, Working Copies, and Inter-Discipline Drawing Reviews (IDR)
2.2.1 Master Stick Files
2.2.2 Working Copies
2.2.3 Inter-Discipline Drawing Reviews
2.3 Vendor Drawing Reviews
2.4 Line Numbering
2.4.1 Line Numbering Rules
2.5 Stress Analysis
2.5.1 The Stress Analysis Procedure
2.5.2 Stress Analysis Procedure Notes
2.6 Model Reviews
2.6.1 Model Review Procedure
2.6.2 Model Review Matrix
2.7 Checking
2.7.1 Clash Check Reporting Procedure
2.7.2 Equipment Checking Procedure
2.7.3 Piping Arrangement and Isometric Checking
2.7.4 Prerequisites and Checking Procedure
2.8 Manhour Estimating and Manpower Planning
2.8.1 Manhour Estimating
2.8.2 Manpower Planning
2.8.3 Other Considerations
3 Deliverables
3.1 Introduction
3.2 Deliverables
3.2.1 Cover Sheets and Drawing Indexes
3.2.2 Plot Plan
3.2.3 Key Plans
3.2.4 Location Plans
3.2.5 Piping Arrangements
3.2.6 Isometrics
3.2.7 Isometric Logs
3.2.8 Tie-in Isometrics
3.2.9 Tie-in List
3.2.10 Demolition Drawings
3.2.11 Heat Tracing Circuit Layouts
3.2.12 Heat Tracing Logs
3.2.13 3-D Models
3.2.14 Model Indexes
3.2.15 CWP Drawing Packages and Scopes of Work (SOW)
3.2.16 Process Flow Diagrams (PFDs)
3.2.17 Piping and Instrumentation Diagrams (P&IDs)
3.2.18 Line Designation Tables (LDTs)
4 Detailed Design
4.1 Introduction
4.2 Contracting and Procurement Plan and Construction Execution Plan
4.3 Modularized and Field Erected Piping Splits and CWP Boundaries
4.3.1 Notes to Figure 4–1
4.4 Model Boundaries
4.4.1 Study Model Boundaries
4.4.2 Detailed Model Boundaries
4.5 Shop and Field Material Splits
4.6 Procurement Splits
4.7 Issued For Bid and Bid Evaluations
4.7.1 Issued for Bid
4.7.2 Clarifications from Bidders and Bid Evaluations
4.8 Equipment Coordinates and Elevations
4.9 Module Design
4.9.1 Design Considerations
4.10 Module Numbering
4.11 Drafting Practice
4.11.1 A Brief History
4.11.2 3-D CAD Drafting Practice
4.11.3 Ownership and Training
4.11.4 Piping Arrangements
4.11.5 Isometrics
4.12 Holds
4.13 Project Binders and Lists
4.13.1 Project Binders
4.13.2 Piping Job Notes and CAD Job Notes
4.13.3 Action Item List and Needs List
4.13.4 Equipment List
4.13.5 Data Sheets
4.14 Managing Standard Drawings
4.15 Project Meetings
4.16 Progress Monitoring
4.17 Design Change Notice (DCN)
4.18 Field Change Notice (FCN)
4.19 Request For Information (RFI)
5 Shop Fabrication
5.1 Introduction
5.2 Kick-off Meetings
5.3 Scopes of Work (SOW)
5.3.1 Example of Pipe Spool Fabrication Scope of Work
5.3.2 Example of Module Fabrication and Assembly Scope of Work
5.4 Instruction to the Fabricator
5.4.1 Example of Instruction to Fabricator
5.5 Requests For Information (RFI)
5.6 Visits with the Fabricators
5.6.1 The Value of Shop Visits
5.6.2 Supporting the Fabricators
5.7 Automatic Spool Generation
5.8 Conclusion
6 Field Construction
6.1 Introduction
6.2 Support from the Home Office
6.2.1 Kick-off Meetings
6.2.2 Field Erection of Piping Scope of Work
6.2.3 Computers, 3-D Software Set-ups, and Maintenance
6.2.4 Request for Information
6.3 Support in the Field
6.3.1 Utilizing the 3-D Models
6.3.2 Problem Solving
6.3.3 Punch Lists and Deficiency Reports
6.3.4 Compiling and Submitting RFIs
6.3.5 Investigating Back Charges and Extras
6.3.6 Progress Monitoring
6.3.7 Maintaining the Master Stick Files
6.3.8 As-Builting
6.4 Lessons Learned
6.5 Safety
Abbreviations
Index
The Planning Guide to Piping Design available in Paperback
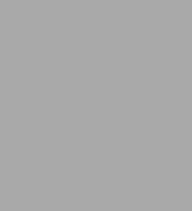
The Planning Guide to Piping Design
by Richard Beale, Paul Bowers
Richard Beale
- ISBN-10:
- 0128102268
- ISBN-13:
- 9780128102268
- Pub. Date:
- 08/19/2016
- Publisher:
- Elsevier Science
- ISBN-10:
- 0128102268
- ISBN-13:
- 9780128102268
- Pub. Date:
- 08/19/2016
- Publisher:
- Elsevier Science
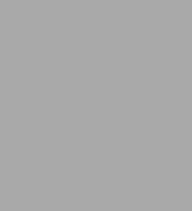
The Planning Guide to Piping Design
by Richard Beale, Paul Bowers
Richard Beale
Paperback
$185.0
Current price is , Original price is $185.0. You
Buy New
$185.00
$185.00
-
PICK UP IN STORE
Your local store may have stock of this item.
Available within 2 business hours
185.0
In Stock
Overview
Peter Smith has joined forces with skilled consultants to take his piping series to the next level. The Planning Guide to Piping Design covers the entire process of planning a plant model project from conceptual to mechanical completion, and explains where the piping lead falls in the process along with his roles and responsibilities. Piping Engineering Leads (or PEL's) used to only receive on-the-job training to learn the operation of producing a process plant. Over time, more schools and programs have developed a more advanced curriculum for piping engineers and designers. However, younger generations of engineers and designers are growing up with a much more technological view of piping design and are in need of a handbook that will explain the proven methods of planning and monitoring the piping design in step-by-step processes. This handbook will provide mentors in the process piping industries the bridge needed for the upcoming engineer and designer to grasp the requirements of piping supervision in the modern age.
Product Details
ISBN-13: | 9780128102268 |
---|---|
Publisher: | Elsevier Science |
Publication date: | 08/19/2016 |
Series: | Process Piping Design Handbook |
Pages: | 227 |
Product dimensions: | 6.00(w) x 9.00(h) x 0.53(d) |
About the Author
Richard Beale has over 40 years of plant layout and piping design experience on upstream, midstream and downstream oil and gas industry projects in the employ of engineering, fabrication, construction and producer companies. His career started as a junior piping draftsman in 1974, and over the years he has held the roles of piping drafter, piping designer, piping squad leader, project piping lead, design and drafting department manager, and technical support to fabrication and construction. He is currently employed by a major oil and gas producer in Engineering Information Management. Having witnessed the technological transition from manual design and drafting to 2D CAD and 3D CAD, he holds a firm belief that a key ingredient to full realization of successful project execution through the adoption of new design technology is being lost. This being a corresponding erosion of experienced design and drafting practitioners possessing of the abilities to develop, modify, and execute new and existing design and drafting procedures that complement the changing technology. It is this belief that has stirred him to write this book as a way of filling the experience gap
Paul Bowers is a senior piping designer with over 30 years of experience working on major process plant projects including refining, cryogenics, pulp & paper, petrochemical, industrial gas installations and SAGD as well as CAD/engineering automation administration. As a software and technology enthusiast Paul believes that machines must adapt to humans and not the other way around.
Currently residing in the Montreal area, Paul has been owner of the PipingDesign.com domain since 1998 is currently webmaster / web developer / "Digital Administrator" and a director with the Houston-based Society of Piping Engineers and Designers as well as founder and past president of the Calgary chapter of the same organization.
Paul Bowers is a senior piping designer with over 30 years of experience working on major process plant projects including refining, cryogenics, pulp & paper, petrochemical, industrial gas installations and SAGD as well as CAD/engineering automation administration. As a software and technology enthusiast Paul believes that machines must adapt to humans and not the other way around.
Currently residing in the Montreal area, Paul has been owner of the PipingDesign.com domain since 1998 is currently webmaster / web developer / "Digital Administrator" and a director with the Houston-based Society of Piping Engineers and Designers as well as founder and past president of the Calgary chapter of the same organization.
Table of Contents
ForewordPreface
List of Figures
List of Tables
1 Before You Begin
1.1 Introduction
1.2 Standards
1.2.1 Standard Drawings
1.2.2 Charts
1.2.3 Drawing Templates and Drawing Standards
1.2.4 Drawing Numbering
1.2.5 3-D Model Numbering
1.2.6 Material Commodity Codes
1.3 Specifications
1.3.1 Piping Classes
1.4 Procedures
1.4.1 Stick Files
1.4.2 Inter-discipline Drawing Reviews
1.4.3 Line Numbering
1.4.4 Stress Analysis
1.4.5 CAD Set-up
1.4.6 3-D Model Reviews
1.4.7 Checking
1.4.8 Manhour Estimating
1.4.9 Progress Reporting
1.4.10 Management of Change
1.4.11 As-Builting
1.4.12 Project Close-out
1.5 Piping Execution Plan
1.5.1 Design Basis Memorandum (DBM)
1.5.2 Project Execution Plan (PEP)
1.5.3 Contracting and Procurement Plan and Construction Execution Plan
1.6 Conclusion
2 Procedures
2.1 Introduction
2.2 Master Stick Files, Working Copies, and Inter-Discipline Drawing Reviews (IDR)
2.2.1 Master Stick Files
2.2.2 Working Copies
2.2.3 Inter-Discipline Drawing Reviews
2.3 Vendor Drawing Reviews
2.4 Line Numbering
2.4.1 Line Numbering Rules
2.5 Stress Analysis
2.5.1 The Stress Analysis Procedure
2.5.2 Stress Analysis Procedure Notes
2.6 Model Reviews
2.6.1 Model Review Procedure
2.6.2 Model Review Matrix
2.7 Checking
2.7.1 Clash Check Reporting Procedure
2.7.2 Equipment Checking Procedure
2.7.3 Piping Arrangement and Isometric Checking
2.7.4 Prerequisites and Checking Procedure
2.8 Manhour Estimating and Manpower Planning
2.8.1 Manhour Estimating
2.8.2 Manpower Planning
2.8.3 Other Considerations
3 Deliverables
3.1 Introduction
3.2 Deliverables
3.2.1 Cover Sheets and Drawing Indexes
3.2.2 Plot Plan
3.2.3 Key Plans
3.2.4 Location Plans
3.2.5 Piping Arrangements
3.2.6 Isometrics
3.2.7 Isometric Logs
3.2.8 Tie-in Isometrics
3.2.9 Tie-in List
3.2.10 Demolition Drawings
3.2.11 Heat Tracing Circuit Layouts
3.2.12 Heat Tracing Logs
3.2.13 3-D Models
3.2.14 Model Indexes
3.2.15 CWP Drawing Packages and Scopes of Work (SOW)
3.2.16 Process Flow Diagrams (PFDs)
3.2.17 Piping and Instrumentation Diagrams (P&IDs)
3.2.18 Line Designation Tables (LDTs)
4 Detailed Design
4.1 Introduction
4.2 Contracting and Procurement Plan and Construction Execution Plan
4.3 Modularized and Field Erected Piping Splits and CWP Boundaries
4.3.1 Notes to Figure 4–1
4.4 Model Boundaries
4.4.1 Study Model Boundaries
4.4.2 Detailed Model Boundaries
4.5 Shop and Field Material Splits
4.6 Procurement Splits
4.7 Issued For Bid and Bid Evaluations
4.7.1 Issued for Bid
4.7.2 Clarifications from Bidders and Bid Evaluations
4.8 Equipment Coordinates and Elevations
4.9 Module Design
4.9.1 Design Considerations
4.10 Module Numbering
4.11 Drafting Practice
4.11.1 A Brief History
4.11.2 3-D CAD Drafting Practice
4.11.3 Ownership and Training
4.11.4 Piping Arrangements
4.11.5 Isometrics
4.12 Holds
4.13 Project Binders and Lists
4.13.1 Project Binders
4.13.2 Piping Job Notes and CAD Job Notes
4.13.3 Action Item List and Needs List
4.13.4 Equipment List
4.13.5 Data Sheets
4.14 Managing Standard Drawings
4.15 Project Meetings
4.16 Progress Monitoring
4.17 Design Change Notice (DCN)
4.18 Field Change Notice (FCN)
4.19 Request For Information (RFI)
5 Shop Fabrication
5.1 Introduction
5.2 Kick-off Meetings
5.3 Scopes of Work (SOW)
5.3.1 Example of Pipe Spool Fabrication Scope of Work
5.3.2 Example of Module Fabrication and Assembly Scope of Work
5.4 Instruction to the Fabricator
5.4.1 Example of Instruction to Fabricator
5.5 Requests For Information (RFI)
5.6 Visits with the Fabricators
5.6.1 The Value of Shop Visits
5.6.2 Supporting the Fabricators
5.7 Automatic Spool Generation
5.8 Conclusion
6 Field Construction
6.1 Introduction
6.2 Support from the Home Office
6.2.1 Kick-off Meetings
6.2.2 Field Erection of Piping Scope of Work
6.2.3 Computers, 3-D Software Set-ups, and Maintenance
6.2.4 Request for Information
6.3 Support in the Field
6.3.1 Utilizing the 3-D Models
6.3.2 Problem Solving
6.3.3 Punch Lists and Deficiency Reports
6.3.4 Compiling and Submitting RFIs
6.3.5 Investigating Back Charges and Extras
6.3.6 Progress Monitoring
6.3.7 Maintaining the Master Stick Files
6.3.8 As-Builting
6.4 Lessons Learned
6.5 Safety
Abbreviations
Index
What People are Saying About This
From the Publisher
Step-by-step resource assisting the piping engineer/piping lead in the effective organization and management of piping systems designs
From the B&N Reads Blog
Page 1 of