The Six Sigma Revolution: How General Electric and Others Turned Process Into Profits / Edition 1 available in Hardcover
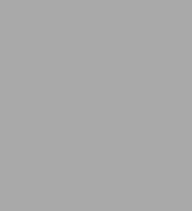
The Six Sigma Revolution: How General Electric and Others Turned Process Into Profits / Edition 1
- ISBN-10:
- 047138822X
- ISBN-13:
- 9780471388227
- Pub. Date:
- 11/24/2000
- Publisher:
- Wiley
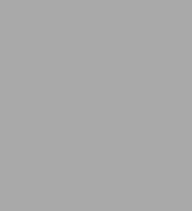
The Six Sigma Revolution: How General Electric and Others Turned Process Into Profits / Edition 1
Hardcover
Buy New
$58.00Buy Used
$34.11-
-
SHIP THIS ITEM
Temporarily Out of Stock Online
Please check back later for updated availability.
-
Overview
Currently exploding onto the American business scene, the Six Sigma methodology fuels improved effectiveness and efficiency in an organization; according to General Electric's Jack Welch, it's the "most important initiative [they] have ever undertaken." Written by the consultant to GE Capital who helped implement Six Sigma at GE and GE's General Manager of e-Commerce, Making Six Sigma Last offers businesses the tools they need to make Six Sigma work for themand cultivate long-lasting, positive results. Successful Six Sigma occurs when the technical and cultural components of change balance in an organization; this timely, comprehensive book is devoted to the cultural component of implementing Six Sigma, explaining how to manage it to maintain that balance. The authors address how to create the need for Six Sigma; diagnose the four types of resistance to Six Sigma and how to overcome them; manage the systems and structures; and lead a Six Sigma initiative. This book applies the Six Sigma approach to business operations across the organizationunlike other titles that focus on product development. Plus, it provides strategies, tactics, and tools to improve profitability by centering on the relationship between product defects and product yields, reliability, costs, cycle time, and schedule.
George Eckes (Superior, CO) is the founder and principal consultant for Eckes & Associates. His clients include GE Capital, Pfizer, Westin, Honeywell, and Volvo. Eckes has published numerous papers on the topic of performance improvement and is the author of The Six Sigma Revolution: How General Electric and Others Turned Process into Profits (0-471-38822-X) (Wiley).
Product Details
ISBN-13: | 9780471388227 |
---|---|
Publisher: | Wiley |
Publication date: | 11/24/2000 |
Pages: | 288 |
Product dimensions: | 6.26(w) x 9.47(h) x 1.03(d) |
About the Author
Read an Excerpt
Chapter 1: Introduction to Six Sigma
Organizations are constantly on the alert to gain a competitive edge, using the many tools that have long been touted as a way to beat the competition. Yet, despite the focus on innovative ways of making products and providing services, there remains one constant: Organizations that produce better quality products and services than their rivals beat the competition time and again. Six Sigma Improvement is a tried-and-tested method that has been effective in helping businesses dominate their competition.Achieving high quality has been a concern since the beginning of the twentieth century, when there was a massive shift away from an agrarian culture toward an industrial culture. As the United States evolved from a culture of craftsmanship toward one of mass production, assurance of product quality shifted from individuals personally inspecting their products to the development of a group of specialists who inspected parts and products after they were made.
This approach to quality control and its fit with customer needs worked well for many years for a variety of reasons. First, as the century progressed, the U.S. consumer's appetite for goods and services became nearly insatiable. Beginning with Henry Ford and the mass production of the automobile to William Levit's postWorld War II creation of reasonably priced homes for returning veterans, Americans everywhere desired the material goods that would contribute to making their lives better.
The emphasis on quantity of goods and services superceded the emphasis on quality. Americans at that time were more accepting, willing to put up with a creaky window or a car door thatoccasionally had trouble closing. Additionally, in 1950, only a small percentage of women worked outside the home. Today, when 50 percent' of women work outside the home, it is more difficult to find the time to get the car repaired or wait for the repairman at home.
As Americans entered the 1970s, the definition of quality began to change. Traditionally, quality had referred to features, such as the difference between a Chevrolet Impala and a Cadillac Seville. But, several key events changed the perception of Americans toward quality.
As more and more women entered the workforce, there was less time to focus on maintenance of the home and the various products that were found in it. More immediate in its effect was the gas shortage of the mid-1970s. As the gas-guzzlers produced by Detroit proved too expensive, Americans migrated to foreign imports, particularly Japanese automobiles that were fuel-efficient. While enjoying these Japanese products, Americans found an added benefit. Japanese cars performed better in terms of durability and reliability. Gone were the major service problems that had historically plagued Detroit's offerings.
Japan had a different approach to and attitude toward quality. Since the days of mass production, Americans' approach to and attitude toward quality was based on mass inspection to find and sort out nonconforming parts or products. Starting with the famed assembly line of Ford, most production in American factories was based on mass producing something and inspecting key characteristics at the "end of the production line." This approach to quality improvement was found to be highly ineffective. Experts have determined that 100 percent inspection not only adds to the cost of the product, but is 80 percent effective at best. Take the quiz below to give yourself a feel for this ineffectiveness. In the text below, identify (inspect) the number of f's that appear:
Count the number of times the letter f appears in the following:Finished files are the result of years of scientific study combined with the experience of years.
How long did it take to identify the 9 f's? Oh, you didn't get all 9? You may have missed f's that sound like v's. Or you may have misinterpreted the instuctions and just read below the first paragraph. If you did catch all the Ps, how long did it take you? Either way, inspecting something is no guarantee that you will find defective parts or product. Second, think of the costs associated with inspection. The act of inspection does not add to the quality of the part or product. It simply verifies that it meets some specification or function. It's like going to the coroner when you are sick. The coroner will only tell you if you are dead or alive. Inspection alone does not add value and can be prohibitively expensive, whether we are talking about labor costs or the machines that are used to inspect. Furthermore, if you rely on inspection alone, there is no guarantee that you will improve performance.
On the other hand, the Japanese automobile was produced using an entirely different approach. Instead of mass producing a part or product and inspecting it after the fact, the Japanese automakers were committed to never-ending 'improvement of the product and the process that created it. (What is a process? A process is defined as those series of steps and activities that take inputs, add value, and produce an output.)
The way the Japanese were producing cars at that time was revolutionary. Their approach made management and autoworkers focus on continually making something better.
Measurement methods began to focus on the amount of variation that existed in a process and its subsequent part or product. Instead of measuring something to see if it was good or bad, the measurement of the part was an indicator of how well the process was performing.
This dramatic approach to production remained largely a Japanese phenomenon until 1980. In that year, NBC produced a documentary entitled If Japan Can, Why Can't We? Journalist Lloyd Dobbins profiled how an American statistician had a major impact on Japanese organizations. The man was W. Edwards Deming, a statistician who in the 1930s and 1940s had worked in the Census Bureau. As part of the armistice with the Japanese in 1945, the United States agreed to provide Japan with assistance in demilitarizing their country while simultaneously rebuilding their economic base. Deming was one of many who visited Japan and conducted seminars, at first primarily on statistics, to assist the Japanese in their effort to re-industrialize.
Deming made repeated trips to Japan and gradually shaped his message to include various management principles that company after company embraced...
Table of Contents
Introduction to Six Sigma.The Strategy of Six Sigma: Eight Steps to Strategic Improvement.
Profits = Customer + Process + Employee.
Project Start-Up: Tactical Six Sigma.
Measuring Project Sigma: How Close are You to Perfection?
Data and Process Analysis: The Keys to the Project.
Root Cause Analysis: Never Stop Asking "Why".
Selecting Solutions That Drive Sigma Performance.
Holding the Gains: Making Sure Your Solutions Stick.
How Six Sigma Initiatives Fail and How to Avoid Mistakes.
Appendix.
Index.
Preface
Six Sigma is a quantitative approach that fuels improved effectiveness and efficiency in an organization. This approach was first created in the 1980s by Motorola. Then, in the 1990s, companies like AlliedSignal and General Electric contributed to making Six Sigma the most popular quality improvement methodology in history.
This book is different than any other on the market. Rather than tout how important Six Sigma is, The Six Sigma Revolution addresses those executives and implementers interested in creating and sustaining a Six Sigma initiative in their organization.
This book begins with a discussion of the quality movement in the twentieth century, describing the limitations with previous efforts, and how Six Sigma came to be the management approach of choice for those interested in making their organizations world class.
What makes Six Sigma different, in part, is its focus on the involvement of management at all levels of an organization. This book addresses the elements management must institute to create an infrastructure for Six Sigma to work.
The second major component of Six Sigma addresses the tactics that drive improved effectiveness and efficiency in an organization. This method uses a simple but detailed approach to improve the performance of existing processes.
The journey through the tactical aspects of Six Sigma begins with how to charter teams so they are working on processes that directly impact the strategic business objectives of the organization.
Later chapters address how tocalculate sigma at the process level, how to create specific, measurable problem statements that the project team will then attempt to improve, as well as how to utilize the analysis and improvement tools that will assist teams in their efforts to improve sigma performance. The final tactical chapter describes how a team transfers an improved process so that improvement will be sustained over time.
Another aspect of this book that you will not see elsewhere is the recognition of managing cultural change in the Six Sigma initiative. Six Sigma initiatives involve a cultural transformation toward managing with facts and data. For some organizations, this transformation will be a dramatic change from current management methods. It is probable that there will be resistance. This book addresses four major types of resistance, indicating how to diagnose the type of resistance and then providing strategies to overcome resistance.
The later chapters provide both executives and implementers with methods on how to sustain Six Sigma initiatives. The reader will learn how to create and manage Business Quality Councils where management has continuing responsibilities for the success of Six Sigma within their organization. We discuss how to change the systems and structures of an organization so that Six Sigma is successful.
Finally, the last chapter addresses 10 ways in which Six Sigma initiatives fail. Each failure is discussed to illustrate how to overcome failure to create a Six Sigma success story.
George Eckes