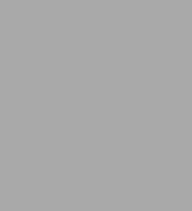
The Six Sigma Way Team Fieldbook: An Implementation Guide for Process Improvement Teams
300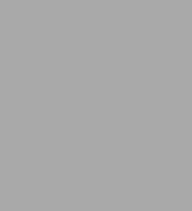
The Six Sigma Way Team Fieldbook: An Implementation Guide for Process Improvement Teams
300eBook
Available on Compatible NOOK devices, the free NOOK App and in My Digital Library.
Related collections and offers
Overview
This companion guide to the bestselling The Six Sigma Way focuses on the project improvement teams that do the real, in-the-trenches work of Six Sigma—measuring performance, improving quality and saving millions in the process.
The Six Sigma Way Team Fieldbook is a highly practical reference for team leaders and members, outlining both the methods that have made Six Sigma successful and the basic steps a team must follow in an improvement effort. Written by three veteran trainers of Six Sigma “Black Belts” and teams at GE, Sun Microsystems, and Sears, this hands-on guide helps teams obtain the skills they need to identify a product, service, or process that needs improvement or redesign; gather data on the process and the rate of defects; find ways to improve quality up to a Six Sigma level—just 3.4 defects per million; and much more.
* Includes dozens of data-gathering forms and Six Sigma tools and worksheets
* Describes key improvement methods in a concise “how-to” format with checklists and tips
Product Details
ISBN-13: | 9780071431491 |
---|---|
Publisher: | McGraw Hill LLC |
Publication date: | 11/04/2001 |
Sold by: | Barnes & Noble |
Format: | eBook |
Pages: | 300 |
File size: | 9 MB |
About the Author
Peter S. Pande, Robert S. Neuman, and Roland R. Cavanagh wrote the bestselling The Six Sigma Way. Pande is president of Pivotal Resources, Inc., a leading organizational improvement consulting and training firm. He is an experienced executive consultant and has helped guide Six Sigma initiatives at major corporations. Neuman is a consultant with Pivotal Resources, a sought-after speaker and a former professor at Amherst College and the State University of New York. Cavanagh, a professional engineer, is a consultant with Pivotal Resources, providing strategic consulting and improvement training and coaching to non-manufacturing as well as technical environments.
Read an Excerpt
The Six Sigma Way Team Fieldbook
An Implementation Guide for Project Improvement Teams
By Peter S. Pande, Robert P. Neuman, Roland R. Cavanaugh
The McGraw-Hill Companies, Inc.
Copyright © 2002The McGraw-Hill Companies, Inc.All rights reserved.
ISBN: 978-0-07-143149-1
Excerpt
CHAPTER 1The Six Sigma System A New Way to an Old Vision
Six sigma. A new name for an old vision: near-perfect products and services for customers.
Why is Six Sigma so attractive to so many businesses right now? Because being successful and staying successful in business is more challenging today than ever before. In today's economy, most people provide services rather than making goods and products. And most of those services operate at levels of inefficiency that would close down a factory in a month if it produced as many defects. Six Sigma provides power tools to improve those services to levels of accuracy and quality seen so far only in precision manufacturing.
Companies like General Electric and Sun Microsystems are flexing the Six Sigma system to create new products, improve existing processes, and manage old ones. Leaders of these and other Six Sigma companies know that Six Sigma encompasses a wide variety of simple and advanced tools to solve problems, reduce variation, and delight customers over the long haul. Six Sigma ...
* Generates quick, demonstrable results linked to a no-nonsense, ambitious goal: To reduce defects (and the costs they entail) to near zero by a target date.
* Has built-in mechanisms for holding the gains.
* Sets performance goals for everyone.
* Enhances value to the customer by exposing "defects" caused by functional bureaucracy and by encouraging managers and employees alike to focus their improvement efforts on the needs of external customers.
* Speeds up the rate of improvement by promoting learning across functions.
* Improves our ability to execute strategic changes.
You can find descriptions of successful applications of Six Sigma in The Six Sigma Way. This chapter reviews key concepts introduced in that book—as a refresher for those who have read it and background for those who have not.
What Is Six Sigma?
If Six Sigma is so great, where has it been hiding all these years? Like most great inventions, Six Sigma is not all "new." It combines some of the best techniques of the past with recent breakthroughs in management thinking and plain old common sense. For example, Balanced Scorecards are a relatively recent addition to management practices, while many of the statistical measurement tools used in Six Sigma have been around since the 1940s and earlier.
The term "Six Sigma" is a reference to a particular goal of reducing defects to near zero. Sigma is the Greek letter statisticians use to represent the "standard deviation of a population." The sigma, or standard deviation, tells you how much variability there is within a group of items (the "population"). The more variation there is, the bigger the standard deviation. You might buy three shirts with the "same" sleeve length only to discover that none them are exactly the length printed on the label: two are shorter than the stated length, and the other is nearly an inch longer—quite a bit of "standard deviation."
In statistical terms, therefore, the purpose of Six Sigma is to reduce variation to achieve very small standard deviations so that almost all of your products or services meet or exceed customer expectations.
Variation and Customer Requirements
Traditionally, businesses have described their products and services in terms of averages: average cost, average time to deliver a product, and so on. Even hospitals have a measure for the average number of patients who pick up a new infection during their stay.
Trouble is, averages can hide lots of problems. With the way that most processes operate today, if you promise customers to deliver packages within two working days of getting their order, and your average delivery time is two days, many of the packages will be delivered in more than two days—having an average of two days means some packages take longer and some take less. If you want all packages to be delivered in two days or less, you'll have to dramatically eliminate problems and variations in your process.
Here's an example from The Six Sigma Way: you want your "drive to work" process to produce defects (early or late arrivals) no more often than 3.4 trips out of every million trips you make. Your target arrival time at work is 8:30 a.m., but you're willing to live with a few minutes either way, say 8:28 to 8:32 a.m. Since your drive normally takes you 18 minutes, this means your target commute time is anywhere between 16 and 20 minutes. You gather data on your actual commute times, and create a chart like that shown in Figure 1-1.
There will always be some variation in a process: the core issue is whether that variation means your services and products fall within or beyond customer requirements. If you want to be a Six Sigma commuter, the problem is that your process produces a lot of defects (late or early arrival times).
So you set about improving your process. You find the route that is most reliable (has the least traffic and fewest stop lights), you get up when your alarm clock first goes off, you recalibrate your cruise control, etc. After all your changes have been implemented, you gather more data. And voilà, you have become a Six Sigma commuter. The new standard deviation of just 1/3 of a minute means the variation in your process practically guarantees that you will always arrive within 16 to 21 minutes of leaving your house (see Figure 1-2).
This example has direct meaning for the business world. If we promise on-time airline departures, but actual departures vary from 5 to 30 minutes late, customers will understandably be angry and take their business elsewhere (except it might be hard to find an airline that does that good!). And an electric toaster that toasts the bread today but burns it tomorrow—at the same darkness setting—will find its way back to the store, along with an unhappy purchaser.
What happens when we achieve Six Sigma performance? For a Six Sigma commuter, it means predicting commute time very precisely every day. And a "defect"—a commute taking less than 16 or more than 21 minutes—would happen only 3.4 out of every 1 million commutes (may we live that long!).
Defects and Sigma Levels
One virtue of Six Sigma is that it translates the messiness of variation into a clear black-or-white measure of success: either a product or service meets customer requirements or it doesn't. Anything that does not meet customer requirements is called a defect. A hotdog at the fair with mustard is a defect if the customer asked for ketchup. A rude reception clerk is providing defective service. A bad paint job on a new car is a defect; a late delivery is a defect; and so on.
If you can define and measure customer requirements, you can calculate both the number of defects in your process and outputs as well as the process yield, the percentage of good products and services produced (meaning they are without defects). There are simple tables that let you convert yield into sigma levels.
Another approach to determining a sigma level is to calculate how many defects occur compared to the number of opportunities there are in the product or service for things to go wrong. The outcome of this calculation is called Defects per Million Opportunities (DPMO), which is another way to calculate the Sigma Level or yield of a process.
System Alignment: Tracking the Xs and Ys
Six Sigma companies commonly use shorthand to describe some key id
(Continues...)
Excerpted from The Six Sigma Way Team Fieldbook by Peter S. Pande. Copyright © 2002 by The McGraw-Hill Companies, Inc.. Excerpted by permission of The McGraw-Hill Companies, Inc..
All rights reserved. No part of this excerpt may be reproduced or reprinted without permission in writing from the publisher.
Excerpts are provided by Dial-A-Book Inc. solely for the personal use of visitors to this web site.