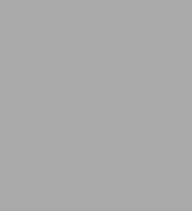
The U.S. Submarine Production Base: An Analysis of Cost, Schedule, and Risk for Selected Force Structures
203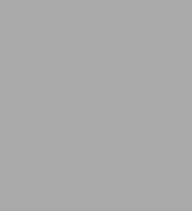
The U.S. Submarine Production Base: An Analysis of Cost, Schedule, and Risk for Selected Force Structures
203Paperback
-
SHIP THIS ITEMTemporarily Out of Stock Online
-
PICK UP IN STORE
Your local store may have stock of this item.
Available within 2 business hours
Related collections and offers
Overview
Product Details
ISBN-13: | 9780833015488 |
---|---|
Publisher: | RAND Corporation |
Publication date: | 05/17/1995 |
Pages: | 203 |
Product dimensions: | 7.00(w) x 9.98(h) x 0.59(d) |
Read an Excerpt
THE U.S. SUBMARINE PRODUCTION BASE
An Analysis of Cost, Schedule, and Risk for Selected Force StructuresBy John Birkler John F. Schank Giles K. Smith Fred Timson James Chiesa Marc Goldberg Michael Mattock Malcolm MacKinnon
Rand Corporation
Copyright © 1994 RAND CorporationAll right reserved.
Chapter One
INTRODUCTION
The security and economic well-being of the United States depend upon freedom of the seas for merchant vessels engaged in American trade and U.S. warships defending American interests around the globe. The U.S. forces beneath the world's oceans play a vital role in maintaining the American maritime preeminence necessary to guarantee freedom of the seas. However, in light of changes in the world, the accompanying reductions in threats to American interests and resources devoted to national defense, and the vigorous pace of submarine construction in the past decade, there is no longer a pressing need for production now of a new class of submarines for the U.S. fleet. - Donald J. Atwood, Jr.
Writing in 1992, then-Deputy Secretary of Defense Atwood expressed well the need for U.S. attack submarines and the sufficiency of the current submarine force to meet that need. At some point in the future, of course, it will be necessary to build more submarines to replace the current ones as they become too old to operate safely. But how difficult will it be to resume production once it has stopped? Important construction skillsmay be lost-skills that may be expensive and time-consuming to restore. Will the extra cost be greater than that saved by stopping production? Would it be wiser to maintain skills and facilities by continuing to build submarines at a low rate in the interim, even though building additional ships cannot be justified by near-term national security needs?
These and related issues were addressed in the study reported in this volume, which was undertaken by RAND's National Defense Research Institute for the Office of the Under Secretary of Defense for Acquisition (now Acquisition and Technology). RAND was asked to evaluate "the practicality and cost effectiveness of reconstitution of the submarine production base versus a continuing program for limited production." RAND's analysis built on earlier research on shutting down and restarting production in the aircraft industry and on a broad set of studies in acquisition policy.
This report begins with some background information for the reader unfamiliar with the status of the U.S. submarine fleet and the special requirements of submarine construction. We then assess the cost and schedule implications of shutting down and restarting each of the principal elements of the submarine industrial base-the shipyards, nuclear-system vendors, and nonnuclear-system vendors. Next, we show how the schedule effects of shutdown and restart interact with factors such as desired fleet size, annual production rate, and number of operating shipyards to determine the maximum feasible gap (length of time) in submarine delivery. This analysis permits the construction of different time gap scenarios. We then estimate the costs of those scenarios, including the shutdown and restart costs calculated earlier. The quantitative analysis is combined with a qualitative assessment of important risks entailed in shutdown and restart to yield the report's conclusions and final observations.
Our analyses drew on information from shipyards and vendors, components of the U.S. Navy and the Office of the Secretary of Defense, and foreign governments with shutdown experience. Sources included persons with varying perspectives on the seriousness of the delays, costs, and risks associated with a production gap. We reviewed all data critically, made adjustments where we believed it appropriate, and built and ran models to draw inferences when the nature of the data permitted. Models and other methods specific to the individual analyses are discussed in connection with those analyses in the following chapters.
Although we consider a wide variety of factors, the focus is on the production base. We do discuss some of the implications of shutdown and restart for the nation's ability to design submarines (see, in particular, Appendix A), but not nearly in as much detail as we treat production. Clearly, design is required for production, and deterioration of the design base is as critical as losses to the production base.
We assume in our cost and schedule analyses that the motivation for restarting or continuing production is to replace obsolescent ships-or to preserve the capacity to replace them. We do not attempt to analyze the implications of a threat to national security dramatic enough to warrant some sort of crash program to bolster the attack submarine force. While the events of the past few years indicate the volatility of the geostrategic environment, we believe that the emergence of such a threat in the near future is unlikely and, in any event, its implications are unclear. Suffice it to say that a national emergency could provide the impetus to build the submarine force up more quickly than we indicate, given sufficient resources.
The study's principal outputs were the analyses and conclusions specific to submarines, but we believe the approach we took is another important product. The overall conceptual framework and the individual models of workforce buildup and fleet dynamics could be used in analogous studies of other types of ships facing similar acquisition decisions. With appropriate modification for different production quantities, maintenance policies, and so forth, the analytical tools developed here could also be applied to other types of major weapon systems.
Chapter Two
BACKGROUND
This chapter provides some general background that may be helpful in understanding the analyses that follow. After reviewing the history and current status of U.S. submarine production and fleet composition, we discuss various pertinent aspects of submarine design, production, and operational life. Finally, we describe the evolution and organization of the submarine production base.
U.S. SUBMARINE PRODUCTION TO DATE
The nuclear submarine propulsion system emerged in the early 1950s as the successor to the then-prevalent diesel-electric system, which used diesel engines on the surface and electric batteries while submerged. Nuclear power permitted a technical solution to the submarine's greatest vulnerabilities-the need to surface or snorkel periodically to recharge the batteries, and the submerged- speed constraint enforced by limited battery capacity. When the first nuclear submarine, USS Nautilus, was commissioned, the U.S. submarine fleet consisted of about 140 diesel-electric boats. New submarine classes were rapidly prepared for construction (see Figure 2.1). The Skate and Skipjack classes were begun in the 1950s as refinements of the Nautilus concept. In 1958, construction started on the Thresher (now Permit) class, which was the first of what would today be considered the modern, front-line submarine. As the cold war with the Soviet Union raged, the development of the ballistic missile submarine became a national priority. Five classes of ballistic-missile-carrying submarines (SSBNs) were fielded, representing step improvements in propulsion technology and ship and missile design. In all, 41 SSBNs were commissioned between 1960 and 1967. During this same period, 24 nuclear attack submarines (SSNs) were commissioned to augment the eight nuclear-powered submarines built before 1960.
Meanwhile, the number of diesel submarines was rapidly reduced as World War II vintage subs were scrapped or sold to allies (see Figure 2.2). The Navy's avid pursuit of nuclear-powered submarines through the 1970s permitted the total fleet size to remain relatively constant as the remainder of the diesel-electric ships were removed from service. Now, the submarine force in active service is completely nuclear, comprising about 90 SSNs and 20 SSBNs.
The early nuclear submarine classes were small, often comprising only a few ships; some one-of-a-kind submarines were built. The concepts were new and many unique designs were explored in searching for the best combination of hull form, size, and propulsion and other internal systems. As submarines evolved, class sizes became larger-a result of the early engineering and learning process that discarded unworkable ideas and retained high performance characteristics. Large classes of multimission submarines gained a cost advantage from repeated construction of the same design.
Several classes of submarines are now in service or are being built (see Table 2.1). The current version of SSBN in production is the Ohio class (sometimes referred to as the SSBN 726 class or as the Trident class, after the name of its missile system). Fourteen Ohio-class submarines have been completed, with four more being built. Some older SSBNs of the Lafayette class and the Benjamin Franklin class remain in the inventory and are scheduled for deactivation in the next few years. Two older SSBNs have been converted to carry out special-forces delivery missions.
The oldest attack submarines in the active fleet are those of the Sturgeon class (SSN 637), whose construction was begun in the early 1960s. This submarine incorporated advanced quieting and sensor systems to make it one of the most successful classes of attack submarines in the fleet's history. In all, 37 of these submarines and one variant (USS Glennard P. Lipscomb) were built. Some Sturgeon-class submarines have been deactivated and all remaining ships of this class are scheduled for removal from the fleet by 2000.
In the early 1970s, construction began on the Los Angeles-class (SSN 688) submarine. This submarine was designed with an advanced propulsion plant to give the ship increased speed and maneuverability. In 1980, a major modification was begun with the USS Providence (SSN 719) and all following ships (31 in all), in which 12 tubes for Tomahawk land-attack cruise missiles were mounted in the ballast tanks in the bow. In 1983, work was begun on USS San Juan (SSN 751), the first of what became known as the improved Los Angeles class. In these 688Is, the forward diving planes were moved from the sail to the bow and the sail was strengthened, allowing ice penetration. Also, the combat system was improved. In all, 62 Los Angeles-class submarines have been authorized, with seven remaining in various stages of construction.
The newest class of attack submarine is the Seawolf (SSN 21), designed to combat the most advanced Soviet submarine threat. It incorporates advances in quieting, firepower, diving depth, sonar, and propulsion. Two Seawolf-class submarines have been authorized and are under construction. The first is scheduled for delivery in 1996.
As for the future, it is anticipated that the SSBN fleet will consist of 18 Ohio-class submarines; all earlier class SSBNs will be decommissioned or modified for other service. Some of the early Los Angeles-class submarines are to be decommissioned early as a cost-cutting effort by the Navy to reduce the size of the fleet. It is unlikely that large numbers of Seawolf-class submarines will be built because of their cost (in the neighborhood of $2 billion). A third ship is planned for a 1996 construction start, though it is conceivable that no more than the two currently authorized will be funded. The Navy is also planning a new SSN class, referred to as the "new attack submarine" (NSSN), more affordable than the Seawolf, to begin construction around 1998. Whether to build the third Seawolf and when to begin the NSSN are the key issues in defining a production gap for attack submarines.
Regardless of what start date is chosen, there is no doubt that a new class of submarines will be needed at some point. Observers disagree on the number of attack submarines sufficient to achieve U.S. national security goals in the early part of the next century. But the numbers mentioned within the defense community generally fall between about 40 and 60. As Figure 2.3 illustrates, without any new starts, the number of attack submarines in the fleet will fall below 60 in 2008 and below 40 in 2013, as early Los Angeles-class submarines are decommissioned at age 30.
EVENTS IN THE LIFE OF A SUBMARINE
Time required to design and build, cost to maintain, and when to deactivate are among the factors that must be taken into account in deciding whether to restart production or continue at a low rate. For example, restarting production without an experienced workforce would lengthen design and construction times. Fewer or more maintenance actions may be needed if submarines are decommissioned earlier or later than usual in an attempt to sustain a given fleet size as efficiently as possible. An understanding of the events that take place during a submarine's life is also necessary for an appreciation of the complexity of the tasks involved and thus of the risks entailed in shutting down production and dispersing the workforce. Here, we discuss construction, maintenance, and deactivation of typical attack submarines by an active industrial base. We begin with design, which is not part of the life history of an individual submarine but which must precede construction of the first ship of a new class.
Design
The time required to design a nuclear submarine class has varied greatly. To some degree, design time has been related to technical complexity of the submarine and its systems and the perceived military necessity for fielding the new class. Nautilus was designed and engineered in a relatively short time-only three to four years were required to begin construction from the time the Navy made the decision to proceed with the project. The first SSBN experienced an even faster design period. Military necessity demanded rapid development of the SSBN force and the first ship started life as an SSN in the construction phase. During the construction process, systems were altered and the missile compartment was added in order to develop the class more rapidly.
Design periods today (see Figure 2.4) are longer for a number of reasons. As weapon systems have grown in complexity and expense, DoD has instituted rigorous schedules for their review and approval. The acquisition system requires specific milestones to approve the start of concept development, to approve the concept and begin design and R&D, and to approve the design and begin construction. The other major factor contributing to more lengthy design periods is the technical complexity of the submarine. The Seawolf design team had been working for six years before construction started. Extensive investigation was needed to achieve the desired advances in quieting, sonar and combat system capability, and hull form and maneuverability. (For more information on design, see Appendix A.)
Construction
The construction process begins after a contract is awarded to a shipbuilder. The Navy's practice has been to procure long-lead-time equipment (for example, the reactor vessel and other large nuclear components) two years prior to the expected contract award. After contract award, the shipbuilder procures the necessary material and subcontracted equipment and begins fabrication.
In constructing the submarine classes of the past, the hull was erected and openings were cut to enable installation of major equipment. Cramped working spaces and constrained access made running electrical cable, installing machinery, and welding difficult. In addition, one trade had to finish its work before another could start, contributing to construction inefficiencies.
By the early to mid 1980s, the industry had switched to a modular construction approach, in which steel is rolled and welded into hull cylinders and frames. Decks and supports are built into the cylinders, and equipment is loaded into both ends. Completed cylinders of up to 1000 tons are positioned and welded together and the internal piping and wiring are joined. Access difficulties and "waiting time" are minimized, effecting significant cost and time savings.
(Continues...)
Excerpted from THE U.S. SUBMARINE PRODUCTION BASE by John Birkler John F. Schank Giles K. Smith Fred Timson James Chiesa Marc Goldberg Michael Mattock Malcolm MacKinnon Copyright © 1994 by RAND Corporation. Excerpted by permission.
All rights reserved. No part of this excerpt may be reproduced or reprinted without permission in writing from the publisher.
Excerpts are provided by Dial-A-Book Inc. solely for the personal use of visitors to this web site.