Five years after the MIT report, this book poses the question: What are the results of this revolution in work organization? Scientists and practitioners, many of them involved in earlier reports, evaluate the changes to the automotive industry in Europe and Japan. An insight into recent concepts in automation and the organization of production.
Five years after the MIT report, this book poses the question: What are the results of this revolution in work organization? Scientists and practitioners, many of them involved in earlier reports, evaluate the changes to the automotive industry in Europe and Japan. An insight into recent concepts in automation and the organization of production.
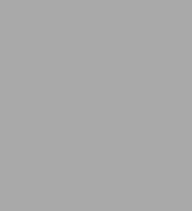
Transforming Automobile Assembly: Experience in Automation and Work Organization
414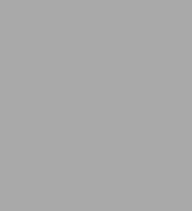
Transforming Automobile Assembly: Experience in Automation and Work Organization
414Paperback(Softcover reprint of the original 1st ed. 1997)
Product Details
ISBN-13: | 9783642643774 |
---|---|
Publisher: | Springer Berlin Heidelberg |
Publication date: | 09/22/2011 |
Edition description: | Softcover reprint of the original 1st ed. 1997 |
Pages: | 414 |
Product dimensions: | 6.10(w) x 9.25(h) x 0.03(d) |