Written by Anna C. Thornton, the well-known author who coined the phrase "variation risk management," this comprehensive book presents new methods and implementation strategies based on her research of industry practices and her personal experience with such companies as The Boeing Company, Eastman Kodak Company, Ford Motor Company, Johnson & Johnson, and many others. Step-by-step guidelines show how you can implement and apply variation risk management to real-world problems within the existing systems of an organization.
Written by Anna C. Thornton, the well-known author who coined the phrase "variation risk management," this comprehensive book presents new methods and implementation strategies based on her research of industry practices and her personal experience with such companies as The Boeing Company, Eastman Kodak Company, Ford Motor Company, Johnson & Johnson, and many others. Step-by-step guidelines show how you can implement and apply variation risk management to real-world problems within the existing systems of an organization.
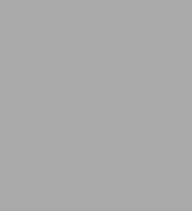
Variation Risk Management: Focusing Quality Improvements in Product Development and Production
320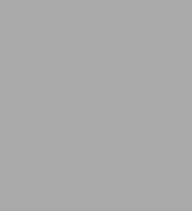
Variation Risk Management: Focusing Quality Improvements in Product Development and Production
320Hardcover
-
SHIP THIS ITEMIn stock. Ships in 1-2 days.PICK UP IN STORE
Your local store may have stock of this item.
Available within 2 business hours
Related collections and offers
Overview
Written by Anna C. Thornton, the well-known author who coined the phrase "variation risk management," this comprehensive book presents new methods and implementation strategies based on her research of industry practices and her personal experience with such companies as The Boeing Company, Eastman Kodak Company, Ford Motor Company, Johnson & Johnson, and many others. Step-by-step guidelines show how you can implement and apply variation risk management to real-world problems within the existing systems of an organization.
Product Details
ISBN-13: | 9780471446798 |
---|---|
Publisher: | Wiley |
Publication date: | 11/05/2003 |
Pages: | 320 |
Product dimensions: | 6.36(w) x 9.57(h) x 0.80(d) |
About the Author
Read an Excerpt
Variation Risk Management
Focusing Quality Improvements in Product Development and ProductionBy Anna C. Thornton
John Wiley & Sons
ISBN: 0-471-44679-3Chapter One
INTRODUCTION
The increased rate of change of technology and the speed at which companies now can adopt new technology has reduced the "new toy," or first-to-market, effect in many industries. Today, consumers take for granted that every company will incorporate the newest available technology in its products. Customers want the newest features while getting the best value for their money. This is true whether the customer is a purchaser of medical devices for a health maintenance organization, a government agent purchasing multi-million-dollar defense equipment, or an everyday consumer of digital cameras. Because of these customer expectations, operational efficiency-the ability to quickly and reliably design and produce high-quality products at low cost-is now a major differentiating factor between companies. Operational efficiency drives profit, return on investment, and ultimately, shareholder value. It is companies that can bring well-designed new products to market quickly, operate efficiently with minimal overhead, and produce high-quality products with minimal scrap or rework that will succeed and grow.
A critical factor in operational efficiency is the ability to design and build high-quality products. This book focuses on one aspect of quality: variation inproduct dimensions and features and its impact on the performance, cost, and safety of a product. Variation in production impacts many aspects of operational efficiency (Fig. 1-1): inventory, touch time, warranty and product returns, and capacity utilization. Ultimately, variation increases waste and reduces profit.
When observing quality initiatives of many companies, one sees an interesting contradiction emerge. Most companies talk about the importance of designing and building high-quality products that are robust to variation and produced at a low cost. They can quote fluently such authors as Crosby, Deming, and Taguchi (Crosby, 1979; Deming, 1986; Taguchi, 1992) and many have Six Sigma Black Belts on staff. However, when actually designing a product, they say, "Robust design is great, but we cannot apply it everywhere. We just don't have time." Schedule takes precedence, and consequently, manufacturing often is handed a product that is difficult to build reliably with a high degree of quality. The question arising from this contradiction is: "If companies understand variation reduction tools and the need for them, why do companies continually struggle to apply them?"
A similar contradiction is apparent in regard to products already being manufactured. Organizations understand the need to improve product quality to save cost. They have many tools in place to do variation reduction including Six Sigma, continual process improvements, Total Quality Management (TQM), and statistical process control (SPC), to name a few, but after an initial push do not continue the efforts. They do provide adequate support to help employees understand where to apply the tools. People identify Six Sigma projects without questioning where variation is showing the most impact across the organization. Often the easy projects are identified-not the right ones. In some cases, companies are able to show polished presentations of current quality improvement projects; however, it is often the case that few projects are completed; or, if they are, returns are never as large as promised. In some cases, implications of a change on the whole organization are not understood and improvements in one area increase costs in others. For example, measurements can be added to control variation; but the step creates a bottleneck in the factory, increasing cycle time and increasing back orders. Although the cost of variation for one group goes down, the total cost to the organization goes up. Other companies with successful Six Sigma programs can demonstrate that their projects have a positive return on investment but can not demonstrate that the projects they picked were the best projects to work on. Given the cost of deploying a Six Sigma or variation reduction program, it is a waste to not assign teams to projects with the highest return on investment and ensure the projects are completed.
In a large range of companies-from automotive to aerospace to medical to component manufacturers-familiarity with tools is not the problem. Three interrelated challenges face companies that wish to successfully apply these tools. First, companies often do not know how to apply limited resources effectively. Schedules dictate time spent in product development. In production, a limited number of people are allocated to manufacturing process improvement. Second, teams do not know how to agree on the most critical issues and come to a consensus on how to address them. As a result, organizations tend to operate in a fire-fighting mode and have too many ongoing projects that are rarely finished on time. Third, quality is typically addressed on a part-by-part basis rather than optimizing quality and its impact across the entire organization.
To address these challenges, the methodology entitled variation risk management (VRM) was developed. VRM refers to the proper allocation of limited resources to variation control efforts in order to improve quality and reduce cost as efficiently and effectively as possible. In other words, given a large number of opportunities to apply variation control and reduction tools, variation risk management identifies the best opportunities on which to focus. The VRM methodology is based on two fundamental concepts: (1) a holistic view of variation and (2) the identification, assessment, and mitigation (I-A-M) process. Variation risk management can be applied either proactively in the product development process or to an existing product. Variation risk management requires the integration and participation of all functional groups that have influence over product quality, including design engineering, manufacturing, quality, system engineering, customers, procurement, and suppliers.
The existing literature on variation and quality is substantial. A simple search returned 94 books on Six Sigma, 43 books on product development and quality, and 151 books on SPC some of which are listed in the bibliography. Given the amount of material on variation reduction, why write another book? Most books on the market talk about applying specific techniques such as Six Sigma, SPC, robust design, variation reduction, and manufacturing process improvement. Still others promote the importance of quality and reducing variation, but only provide minimal guidelines on the technical and practical aspects of implementing a program.
This book presents proven quantitative methods that have helped many product development and production organizations effectively and efficiently reduce the total impact and cost of variation. The VRM methodology has helped companies identify key areas for improvement, significantly reduce cost, and improve quality. It has been used to guide where Six Sigma, robust design, and other quality improvement efforts are applied to get the best returns. The tools in this book have been used on a wide range of products and technologies including aircraft, automotive, engine design, medical devices, electromechanical devices, optical assemblies, printed wiring boards, and microelectronics.
This book is fundamentally different from other quality and product development books in that it presents quantitative methods, teaches you to look at a product as a system rather than as individual parts, shows you how to target limited resources, and provides methods for ongoing tracking and reduction of variation costs. It provides a fact-based and rigorous approach enabling teams to agree on priorities. One goal of this book is also to demystify the "magic" used by consultants to analyze organizations. It will teach the reader how to think holistically about variation in products.
Some tools presented in the book are good engineering put in a clear framework. This book will help the entire organization to behave in the same way that your best engineers do. In addition new tools that have not appeared before are presented.
1.1. THE COMPETITIVE ADVANTAGE OF VRM
The Ability to Reduce the Impact of Variation Is Critical to Being Competitive. Companies that minimize variation successfully will see lower costs and higher customer satisfaction. CEOs and Wall Street value bottom line improvements because savings accrued by a company can have a large impact on shareholder value. For example, if a company trades at a P/E (price to earnings) ratio of 10 to 1, a recurring saving of $1 million after tax can increase total equity value of the company by $10 million. An organization can use variation risk management tools to:
Develop Better Products. As has been pointed out in a large number of books and articles, the product development team has the greatest control over both cost and quality early in product development (Fig. 1-2). The earlier that variation is used as a criteria to select concepts, parts, and manufacturing processes, the better. When teams address variation late in the product delivery processes, their choices and options for reducing the impact of variation are more limited, are more expensive, and have a smaller impact. The VRM methodology helps teams efficiently identify the best opportunities to improve the design early, resulting in improved customer satisfaction, less scrap and rework, fewer defects, and a leaner production process.
Avoid Excessive Precision in Parts. To avoid potential defects, it is tempting to include expensive precision parts "just in case." Tightening the specifications limits is often used to mitigate quality issues, but this approach often adds excess costs and decreases operational efficiency. Teams must have a thorough understanding of the acceptable level of variation in order to choose the appropriate quality level of parts and manufacturing processes. The VRM methodology identifies parts that have the largest impact on product quality and allows the team to effectively prioritize where additional precision is required and identify alternative, less costly solutions.
Allow Faster Transition to Production. Transition to production is the stage in product development when the product is introduced into the factory and production rates are vamped to full production. During this time, the team works out any bugs in the product and manufacturing processes. It is expensive to redesign at this stage because equipment and tooling has already been purchased and installed. Proactive variation risk management can reduce the number of yield and quality issues that surface during transition to production as well as reduce the time to identify and fix unexpected issues.
Continually Improve Product Quality and Reduce Cost Throughout the Life Cycle of the Product. Companies can lose market share because of a real (or perceived) problem with quality. Proactive variation risk management will help organizations improve product quality before it gets into a customer's hands. In addition, VRM helps identify why products are being returned and links customer return data to manufacturing processes and, best of all, to product design.
Reduce Rework and Scrap. Rework and scrap waste time and resources without providing long term benefits. The occurrence of scrap and rework indicates potential problems, which include a less than robust product design or excessive variation in production processes. Not only do rework and scrap increase the average labor content of a product; they also impact flow through the factory. VRM ensures, through good design, that the product will have a lower scrap and rework rate. During production, VRM identifies key opportunities for reducing costs and quickly implements solutions.
Increase Interchangeability and Replaceability. In military and aerospace applications, the term "interchangeable and replaceable" refers to the ability to replace parts or systems on a product without rework tuning or custom fitting. For example, historically, doors on aircraft were built to match individual aircraft. If a door got damaged, it was not possible to simply install a new door; it had to be custom-fit specifically to the plane. Low variation in mating parts, and robust assembly schemes reduce the need for individual part adjustment, thus reducing the labor required in the manufacturing process and decreasing ongoing maintenance costs. Improving interchangeability is especially important for airlines, where delayed or grounded aircraft cause great expense and poor customer satisfaction.
The Ability to Utilize Limited Resources Effectively to Control the Impact of Variation Is a Competitive Advantage. Variation control tools are not new, nor are they proprietary or patentable. Every company has access to the same tools and methods; any company can develop or purchase a Six Sigma program or hire an SPC expert. Using variation reduction tools only brings a company to the same level playing field. If executed poorly, these programs can have no effect at best, and at worst, negative effects such as delaying the launch of a design or consuming significant resources in production.
Companies must ask themselves, "Given that my competitor has access to the same tools, how do I apply them more effectively, get better results, and spend less money?" One way to improve operational efficiency is to use variation risk management for planning and execution. This means making decisions about design concept, manufacturing processes, and part tolerances that minimize the cost, performance, and safety impacts of variation at the lowest cost with minimal impact to the product development schedule. In production, this means (among other things) picking projects that will have the highest return on investment for the entire enterprise (not just one function) and executing them to get returns quickly. In summary, organizations need to manage variation, not just reduce it.
1.2. GUIDE TO READERS
This book teaches the reader how to determine where to apply variation reduction and quality tools given a limited set of resources. It describes quantitative tools and methods (illustrated with examples) that will provide a competitive advantage in developing, producing, and delivering products. These methods can be applied during either product development or production. Ideally, variation risk management should be included in the way of doing business rather than as a separate program.
Continues...
Excerpted from Variation Risk Management by Anna C. Thornton Excerpted by permission.
All rights reserved. No part of this excerpt may be reproduced or reprinted without permission in writing from the publisher.
Excerpts are provided by Dial-A-Book Inc. solely for the personal use of visitors to this web site.
Table of Contents
Preface.Figures.
Tables.
Text Boxes.
Nomenclature.
Acronyms.
1. Introduction.
1.1. The Competitive Advantage of VRM.
1.2. Guide to Readers.
2. Basics of Variation Risk Management.
2.1. Basic Principles of VRM.
2.1.1. VRM Must Be Holistic.
2.1.2. VRM Must Be Process Oriented.
2.1.3. VRM Must Be Data Driven.
2.2. Variation and Its Impact on Quality.
2.3. Summary.
3. Identification.
3.1. Definition of Key Characteristics and Variation Flowdown.
3.1.1. Key Characteristics.
3.1.2. Variation Flowdown.
3.2. Defining the Scope of the VRM Application.
3.3. Identifying Critical System Requirements.
3.3.1. Identify the Voice of the Customer.
3.3.2. Identify Specifications and Requirements.
3.3.3. Identify Critical System Requirements.
3.4. Identifying System Key Characteristics.
3.4.1. What Is a System Key Characteristic?
3.4.2. Examples of System Key Characteristics.
3.5. Creating the Variation Flowdown.
3.5.1. What Information to Gather.
3.5.2. How to Conduct the Top-Down Process.
3.5.3. How to Conduct the Bottom-Up Process.
3.5.4. How to Conduct and Document the Identification Procedure.
3.6. Summary.
4. Overview of Assessment.
4.1. Assessment during Product Development.
4.2. Assessment during Production.
5. Assessment of Defect Rates.
5.1. Predicting the Frequency of Defects.
5.1.1. Variation Models.
5.1.2. Prediction Tools.
5.2. Estimating the Contributions of Part and Process KCs.
5.2.1. Qualitative Analysis of Variation Contribution.
5.2.2. Quantitative Analysis of Variation Contribution.
5.3. Measuring the Frequency of Defects.
5.4. Measuring the Contributions of Part and Process KCs.
5.5. Summary.
6. Assessment of Cost and Risk.
6.1. Cost and Risk Assessment during Product Development.
6.1.1. Qualitative Assessments.
6.1.2. Step Cost Functions.
6.1.3. Continuous Cost Functions.
6.2. Total Cost of Variation Assessment during Production.
6.2.1. Cost Sources.
6.2.2. Representation of the Total Cost of Variation.
6.2.3. Cost Analysis and Aggregation.
6.3. Summary.
7. Assessment of the Quality Control System.
7.1. QC Plan Maturity.
7.1.1. Detection Capability and Effectiveness.
7.1.2. Diagnosis Capability.
7.1.3. Efficient Resource Utilization.
7.2. QC Location in the Manufacturing Process.
7.3. QC Effectiveness Matrix.
7.4. Summary.
8. Mitigation.
8.1. Mitigation during Product Development and Production.
8.1.1. Mitigation during Product Development.
8.1.2. Mitigation during Production.
8.2. Identifying Mitigation Strategies.
8.2.1. Design Changes.
8.2.2. Manufacturing Process Changes.
8.2.3. Manufacturing Process Improvements.
8.2.4. Monitoring and Controlling Manufacturing Processes.
8.2.5. Testing and Inspection.
8.3. Selecting a Mitigation Strategy.
8.4. Selecting a Project Portfolio.
8.5. Executing Mitigation Strategies.
8.6. Summary.
9. Integration of Variation Risk Management with Product Development.
9.1. Basics of Product Development.
9.1.1. Stage Gate Product Development Process.
9.1.2. VRM during Product Development.
9.1.3. Metrics.
9.2. Requirements Development.
9.3. Concept Development.
9.4. Product Architecture Design.
9.5. System Concept Design.
9.6. Detail Design.
9.7. Product Testing and Refinement.
9.8. Transition to Production.
9.8.1. Handling Customer Complaints.
9.8.2. Wrap-Up.
9.8.3. Documenting the Key Characteristic Plan.
9.9. Production.
9.9.1. Continually Monitor Total Cost of Variation.
9.9.2. Track Customer Complaint Data.
9.9.3. Review Quality Control Data.
9.9.4. Track Impact of Changes.
9.10. Summary.
10. Roles and Responsibilities in Variation Risk Management.
10.1. Product Development.
10.1.1. The Integrated Product Team Approach.
10.1.2. Expert Teams.
10.1.3. Coaches.
10.2. Production.
10.2.1. Production Teams.
10.2.2. Expert Teams.
10.3. Suppliers’ Roles and Responsibilities.
10.3.1. Role of Suppliers during Product Development.
10.3.2. Role of Suppliers during Production.
10.3.3. What Does a KC Mean to a Supplier?
10.4. Summary.
11. Planning and Implementing a Variation Risk Management Program.
11.1. Planning a VRM Program.
11.1.1. Gathering Management Support.
11.1.2. Gathering Organizational Support.
11.1.3. Baselining the Existing VRM Processes.
11.1.4. Formalizing VRM.
11.1.5. Developing KC Tracking Methods.
11.1.6. Identifying Lead Users.
11.1.7. Developing Training Materials.
11.2. Implementing the VRM Program.
11.2.1. Identifying Initial Projects.
11.2.2. Training the Team.
11.2.3. Applying VRM.
11.2.4. Gathering Feedback.
11.3. Summary.
12. Summary.
Appendix A: Maturity Models.
Appendix B: Process Capability Databases.
B.1. Background on Process Capability Data.
B.1.1. Importance of Using Process Capability Data.
B.1.2. Structure and Content of a Process Capability Database.
B.1.3. Difficulties in Implementing Process Capability Databases.
B.2. The Right Structure.
B.2.1. Designing the Indexing Scheme.
B.2.2. Choosing the Database Implementation Approach.
B.2.3. Creating the User Interfaces and Data Analysis.
B.3. The Right Data.
B.4. The Right Management Support.
B.5. The Right Usage.
B.6. Implementation of a Process Capability Database.
B.6.1. Who Should Be Involved.
B.6.2. What Decisions Should Be Made.
B.6.3. Implementation Steps.
B.7. Summary.
Appendix C: Other Initiatives.
C.1. Six Sigma.
C.2. Design for Six Sigma.
C.3. Lean Manufacturing.
C.4. Continual Improvement, TQM, and Kaizen.
C.5. Dimensional Management.
C.6. Design for Manufacturing.
C.7. Quality Function Deployment (House of Quality).
C.8. FMEA.
C.9. Summary.
Appendix D: Summary of Process Diagrams.
Glossary.
Bibliography.
Index.
What People are Saying About This
Dr. Thornton has developed a straightforward and simple way to use this process for aligning customer requirements, product design, process capability, and quality inspections. It works well in the real world!
Thomas Gonzalez, Divisional Vice President, Quality Assurance and Regulatory Affairs, Immunoassay and Clinical Chemistry, Abbott Diagnostics Division
A thoughtful, complete, and very readable approach to robust engineering. It presents insights that correlate with those learned at Ford while developing and executing Design for Six Sigma. Having this book three years ago could've helped with that effort.
David Amos, DFSS Deployment Director, Ford Motor Company
A must-read road map . . . Dr. Thornton cogently explains the importance and the effective implementation of variation risk management across the enterprise to managers, designers, and customers alike.
Mike Vander Wel, PE, Build Integration/Final Assembly Manager, 7E7 Commercial Airplane Program, Boeing Commercial Aircraft Group