What You'll Find Inside
• 28 project plans and material lists for classic furniture in distinct styles
• Timeless techniques for working with power tools and hand tools
• Thorough advice and illustrations for repairing upholstered furniture
• A dedicated section on turning furniture parts with a lathe
• Tips for building and maintaining solid wood, metal and upholstered furniture
What You'll Find Inside
• 28 project plans and material lists for classic furniture in distinct styles
• Timeless techniques for working with power tools and hand tools
• Thorough advice and illustrations for repairing upholstered furniture
• A dedicated section on turning furniture parts with a lathe
• Tips for building and maintaining solid wood, metal and upholstered furniture
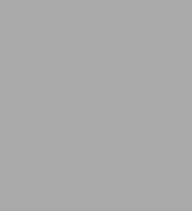
War Department Technical Manual - Woodworking & Furniture Repair: U.S. War Department Manual TM5-613, June 1946
140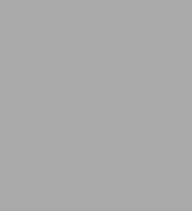
War Department Technical Manual - Woodworking & Furniture Repair: U.S. War Department Manual TM5-613, June 1946
140Paperback
-
SHIP THIS ITEMIn stock. Ships in 1-2 days.PICK UP IN STORE
Your local store may have stock of this item.
Available within 2 business hours
Related collections and offers
Overview
What You'll Find Inside
• 28 project plans and material lists for classic furniture in distinct styles
• Timeless techniques for working with power tools and hand tools
• Thorough advice and illustrations for repairing upholstered furniture
• A dedicated section on turning furniture parts with a lathe
• Tips for building and maintaining solid wood, metal and upholstered furniture
Product Details
ISBN-13: | 9781440355066 |
---|---|
Publisher: | Penguin Publishing Group |
Publication date: | 05/28/2019 |
Pages: | 140 |
Product dimensions: | 8.10(w) x 10.70(h) x 0.40(d) |
Read an Excerpt
CHAPTER 1
INTRODUCTION
1. Purpose and Scope
This Technical Manual is a guide to repair of furniture used in offices, clubs, messes, quarters, and hospitals on Army posts. It covers construction of the more common pieces of furniture, and describes tools and techniques used in furniture repair. It also includes a brief discussion of the properties and uses of various types of wood. (For policy governing furniture repair see TM 5-600.)
2. Standards
The following standards govern all repair work:
a. Materials. Use materials similar in quality to those used in the original article.
(1) Wood. Use properly seasoned wood. (See par. 5.) Match the species, color, grain, and texture of other members as closely as possible. Make sure the grain of the wood is approximately continuous across any lapped or spliced joint; if the grain in the member to be repaired cannot be matched, replace the entire member.
(2) Fabrics. Match closely the pattern, color, and texture of fabric in the original piece.
b. Workmanship. Use good workmanship, regardless of the nature of the repair. See that joints are strong and that surfaces are in condition to receive an acceptable finish. Give furniture a finish suited to its intended use.
CHAPTER 2WOOD
3. General
A general understanding of tree classification and wood structure helps the woodworker make the best use of his materials.
a. Classification of Trees. Nearly all trees are included in the most important of the four major plant groups, the Spermatophyta. This group is divided into Gymnosperms and Angiosperms.
(1) The Gymnosperms include the conifers, known in the lumber industry as softwoods.
(2) The Angiosperms include the monocotyledons (palms, yuccas, bamboos) and the dicotyledons. The latter are much more important. They include all hardwood trees.
(3) The terms hardwood and softwood should be used only in considering a group as a whole. Actually, the wood of certain softwood trees is harder than that of certain hardwood trees.
b. Tree Structure. A tree is a complex structure of roots, trunk, limbs, and leaves. Only the larger portion of the trunk or bole is used for lumber. This portion is first crosscut into logs. Figures 1 and 2 illustrate the important parts of wood.
(1) Tissue zones. A cross section of a tree trunk shows the following well-defined tissue zones in succession from the outside to the center: bark, wood, and pith, a small spot at the center, usually darker in color than the wood. (See fig. 1.)
(2) Heartwood and sapwood. In most species, w'ood at the center of the trunk (heartwood) is darker than wood in the outer part (sapwood) and varies from it slightly in physical properties. The relative proportions of heartwood and sapwood in a tree vary with species and environment. Sapwood normally can be seasoned more easily than heartwood. It is more susceptible to fungus and insect attacks, but is more easily impregnated with wood preservatives. There is no difference in strength.
c. Tree Growth. Wood is not a homogeneous substance, but a composite structure similar in many respects to a honeycomb. It is formed by the accretion of countless numbers of small units known as cells.
(1) Formation of growth rings. When growth is interrupted each year by cold weather or drought, the structure of cells formed at the end and at the beginning of the growing season is different enough to define sharply the annual layers or growth rings. (See fig. 2.)
(2) Structure of growth rings. In many species, each annual ring is divided more or less distinctly into two layers. The inner one, the springwood, consists of cells having relatively large cavities and thin walls. The outer layer, the summerwood, is composed of smaller cells. The transition from springwood to summerwood may be abrupt or gradual, depending on the kind of wood and growing conditions at the time it was formed. In most species, springwood differs from summerwood in physical properties, being lighter in weight, softer, and weaker. Species such as the maples, gums, and poplars do not show much difference in the structure and properties of the wood formed early or later in the season.
d. Strength. Strength of wood depends on the species, growth rate, specific gravity, and moisture content. Extremely slow growth produces a weaker wood. Softwoods (conifers) also are weakened by extremely rapid growth. Wood with low specific gravity or high moisture content is generally weaker. Defects such as grain deviation caused by spiral growth, knots, and burls, also result in weaker wood.
e. Appearance. Structural defects frequently enhance the appearance of wood. Spiral growth results in a winding stripe on turnings. Butt wood shows the assembly of root branches and crotch wood has a merging or diverging pattern. A burl produces attractive boards showing tissue distortion. The bird's-eye figures resulting from the elliptical arrangement of wood fibers around a series of central spots do not weaken maplewood appreciably. Some quarter-sawed woods show pronounced whitish and sycamore.
f. Composition of Wood. Wood is composed mainly of cellulose and lignin. Cellulose is the flakes where the wood rays are exposed. This basic substance; the lignin acts as a stiffening forms an interesting pattern, especially moak and bonding agent.
4. Lumber
a. Ways of Cutting. Lumber is sawed from a log in two distinct ways, with the plane of the cut either radial or tangential to the annual rings.
(1) When the cut is tangent to the annual rings, the lumber is known as plain-sawed (hardwoods) or flat-grain lumber (softwoods). (See fig. 3.)
(2) When the cut is in a radial plane (parallel to the wood rays) the lumber is known as quarter-sawed lumber (hardwoods), or edge or vertical grain lumber (softwoods). (See fig. 3.)
(3) It is commercial practice to call lumber with annual rings at angles from 45° to 90° with the board surface "quarter-sawed," while lumber with rings at angles from 0° to 45° with the surface is called "plain-sawed." Unless the logs are very large, the average sawmill output consists mainly of plain-sawed lumber.
b. Relative Advantages. The relative advantages of plain-sawed and quarter-sawed lumber are:
(1) Plain-sawed lumber, (a) Usually cheaper than quarter-sawed lumber because it can be cut from the log faster and with less waste.
(b) Is less likely to collapse in drying.
(c) Shakes and pitch pockets extend through fewer boards.
(d) Round or oval knots affect surface appearance and strength less than the spike knots in quarter-sawed boards.
(e) Figures formed by annual rings and other grain deviations are more conspicuous.
(2) Quarter-satved lumber, (a) Shrinks and swells less in width than plain-sawed lumber.
(b) Cups and twists less.
(c) Does not surface-check or split as badly in seasoning and use.
(d) Wears more evenly.
(e) Raised grain caused by the annual rings is not as pronounced.
(f) Is less pervious to liquids.
(g) Most species hold paint better.
(h) Figures resulting from pronounced rays, interlocked grain, and wavy grain are more conspicuous.
(i) Width of the sapwood appearing in a board is no greater than that of the sapwood ring in the log.
5. Seasoning Lumber
a. Purpose of Seasoning. As it comes from the sawmill, lumber has a high moisture content and is unsuited for most shop use. Moisture content is the weight of water contained in the wood, expressed as a percentage of the weight of the oven-dry wood. It is important that lumber be seasoned until the moisture content is in equilibrium with the conditions under which the wood will be in service. When a condition of equilibrium moisture content is reached, the lumber has no tendency to shrink, expand, or warp. Because of normal changes in atmospheric moisture, this condition never holds constant. It is desirable, however, that an approximate equilibrium moisture content be reached.
(1) Causes of shrinkage and expansion. As the moisture content of a piece of wood decreases, the wood shrinks. Shrinkage begins when the moisture content drops below the fiber-saturation point. In most woods this is about 30 per cent, the moisture content at which all free water disappears from the cell cavity, while the cell walls are still saturated. Normal air-seasoning practices reduce the moisture content of lumber to between 12 and 15 per cent. If this wood is made into an article which is subjected to further drying action, shrinkage continues. Conversely, if the moisture content of a piece of wood is increased, the piece swells.
(2) Extent of shrinkage and expansion. Wood expands or shrinks only 0.01 to 0.02 of 1 per cent along the grain in length, but can change considerably across gain in width and thickness. Limits vary by species between 4 and 14 per cent for tangential shrinkage and between 2 and 8 per cent for radial shrinkage. The variation in expansion is about the same. Even when painted, wood continues to absorb and lose moisture according to long-time changes in atmospheric humidity. Therefore, it is always good policy to keep a small stock of lumber in the room in which it is going to be worked.
b. Determination of Method. Lumber can be seasoned by natural air-drying, by kiln-drying, or by various chemicals (common salt, urea, and so on) in combination with the first two methods. The time available for drying, the species of wood, and the ultimate use of the wood are important factors in determining the method of seasoning.
(1) Time. If the lumber must be dried and ready for use in a limited time, it is seasoned by kiln-drying. Depending on species and size of stock, kiln-drying requires at least 3 days, while air seasoning normally requires at least 2 months.
(2) Species. Some species need special treatment to prevent checking and warping. For example, black and tupelo gum boards can be kiln-dried slowly with excellent results, but usually warp badly when air-dried if the lumber is not properly piled.
(3) Ultimate use. The moisture content of cabinet woods must be within a range of 5 to 7 per cent. Since this percentage cannot be reached with normal air seasoning, such wood must be kiln-dried.
c. Kiln-drying. Kiln-drying is the common commercial practice.
(1) Types of kilns. The modern compartment kiln has positive control over temperature, relative humidity, and air movement. Progressive type kilns are satisfactory for some kinds of lumber but are not so readily controlled as compartment kilns.
(2) Effects of improper kiln-drying. Seasoning defects are made worse by improper kiln-drying. The most common seasoning defects caused by faulty kilns or poor operation are:
(a) Casehardening, a condition in which such stresses are developed in a board that the outside is in compression and the inside is in tension even when both are equally dry. A flat casehardened board cups when sawed.
(b) Honeycombing (interior checking).
(c) Collapse of cell structure, manifested by an irregular cross section and surface corrugations.
(d) Warping in any or all of four forms:
1. Crook — edge of board convex or concave along its length.
2. Bow — face of board convex or concave along its length.
3. Cup — face of board convex or concave across its width.
4. Twist — the turning or winding of the edge of a board so that the four corners of any face are no longer in the same plane.
(e) Brashness, a condition characterized by low resistance to shock; caused in part by exposure to excessive heat.
(f) Surface and end checking (longitudinal radial cracks or separations formed to relieve drying stresses).
d. Chemical Seasoning. Chemical seasoning in combination with air- or kiln-drying is used by certain lumber companies for seasoning high-quality lumber. Green lumber is taken directly from the grading table and treated with one of several chemicals. Urea is relatively cheap and has proved particularly effective in kiln-drying Douglas fir timbers. There should be a fairly high concentration of the chemical in the surface of the lumber. The zone of chemical concentration has a lower vapor pressure than water, so the surface layer is water-hungry and pulls the moisture from the interior of the board to the surface. Theoretically, the surface zone remains moist at the expense of the interior. This is a reversal of the usual method of seasoning, in which the surface dries first. It sometimes makes possible seasoning of large timbers without the serious surface checking formerly accepted as inevitable.
6. Defects in Lumber
Most lumber has some defect. The most common defects are:
a. Warp. (See par. 5c.).
b. Grain Deviation. Grain deviation is a condition in which the grain does not run parallel to the plane of the board. It may be due to natural or artificial causes. Spiral, wavy, curly, or bird's-eye figures and distortions caused by an injury or knot are natural grain deviations. Artificial deviations result when the plane of the saw cut is not parallel to the outside surface, of the log. Grain deviation weakens a board; so, if strength is an important consideration, lumber with grain deviations must not be used, particularly if the grain slope exceeds 1 in 15.
c. Knots. Knots are portions of what once were limbs. As the tree grows, they become embedded in the trunk. If the limb is alive when the tree is cut, the knot is sound and tight. If the limb is dead, the knot is usually loose, at least in the part of the trunk that grew after the limb died. The grain deviation around a knot, rather than the knot itself, weakens lumber. Knots are round, oval, or spike-shaped, depending on whether the log is plain- or quarter-sawed.
d. Compression Wood. Compression wood is frequently found in conifers on the underside of branches and leaning trunks. It is often characterized by an eccentric pattern of annual rings with an excess of opaque summerwood. The higher specific gravity of compression wood does not mean that this wood is stronger than normal wood. On the contrary, it is weaker and shrinks more in length.
e. Injuries from Handling.If a log is dropped across a rock, or a falling tree strikes a stump, the fibers are likely to be crushed and much of their tensile strength is lost. This defect, known as compression failure, appears on a board as afine irregular line across the grain.
f. Shakes. A shake is a separation of wood along the annual ring. All causes of this defect are not known.
g. Checks. See paragraph 5c.
h. Molds, Stains, Wood Rots. Wood is subject to the destructive action of a large number of fungi. These are microscopic saprophytic plant growths. Molds attack only the surface of the wood, and do little more damage than a layer of dirt. Since penetration is slight, molds often may be dressed off lumber. Stain fungi discolor wood but do not destroy much of the structure. Wood-rotting fungi break down the wood structure and in time reduce the wood to dust. Warmth, moisture, and air are necessary for fungus growth.
i. Insect Damage. Insect damage to seasoned or even partially seasoned lumber is usually slight. Certain woods are susceptible to Lyctus (powder-post) beetles. If a powdery substance is noticed coming from small holes, these beetles have attacked the wood. (See TM 5-632.)
7. Preservation
This term usually refers to the treatment of wood to make it resistant to fungi and insects. The most common method is to treat the wood with a substance poisonous to the destructive organism. Creosote, salts such as zinc chloride, and organic compounds such as beta naphthol are effective.
8. Furniture Woods
The following characteristics are desirable in wood used to make or repair furniture:
a. Stability, or ability to keep its shape without shrinking, swelling, or warping.
b. East of fabricating, surfacing, and finishing.
c. Pleasing appearance.
d. Suitable strength and grain characteristics.
e. Availability.
(Continues…)
Excerpted from "Woodworking & Furniture Repair"
by .
Copyright © 2019 F+W Media.
Excerpted by permission of F+W Media, Inc..
All rights reserved. No part of this excerpt may be reproduced or reprinted without permission in writing from the publisher.
Excerpts are provided by Dial-A-Book Inc. solely for the personal use of visitors to this web site.
Table of Contents
CHAPTER 1. INTRODUCTION, 1,
CHAPTER 2. WOOD, 2,
CHAPTER 3. FURNITURE CONSTRUCTION, 10,
CHAPTER 4. WOODWORKING MACHINERY, 54,
Section I. INTRODUCTION, 54,
II. CIRCULAR SAW BENCHES, 54,
III. OVERARM SAW, 75,
IV. WOOD JOINTER, 84,
V. SINGLE SURFACER, 88,
VI. WOOD SHAPER, 93,
VII. BAND SAW, 96,
VIII. HOLLOW-CHISEL MORTISER, 100,
IX. WOOD LATHE, 103,
CHAPTER 5. GLUES AND GLUING TECHNIQUE, 108,
CHAPTER 6. WOOD FURNITURE, 114,
CHAPTER 7. UPHOLSTERED FURNITURE, 117,
CHAPTER 8. REFINISHING, 120,
CHAPTER 9. METAL FURNITURE, 125,
APPENDIX I. DEFINITIONS, 126,
II. REFERENCES, 127,
INDEX, 128,